The Acceptable Quality Level (AQL)
The acceptable quality level determines the highest acceptable defect percentage, the stated defect ratio calculated as a percentage clarifies the value that the consumer can generally accept in most situations by using a certain sampling procedure.
Defects are classified into three levels based on their severity ratings:
Fatal Defects: does not comply with the product’s mandated regulations and/or endangers consumer safety during use.
Serious Defects: evident exterior defects that can lead to product malfunction, decrease product usability, and reduce product revenue.
Minor Defects: defects that do not impair product usability but may impact sales revenue or differs from the required quality standard.
While most clients endorse these criteria, we can also customize our standards to your particular preferences.
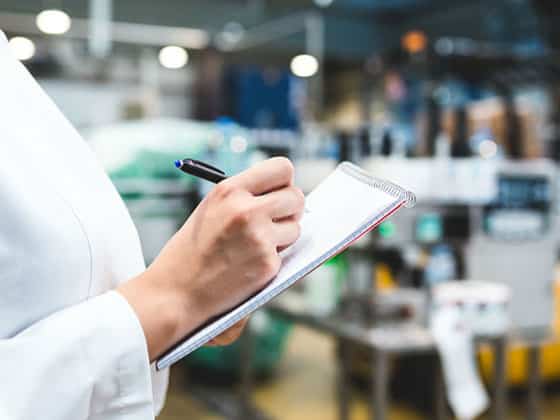
Sampling Table
AQL Sampling tables are a set of charts that enable users to quickly calculate the number of samples required for quality inspection testing as well as the number of permissible faulty units depending on the given AQL.
How To Calculate The Appropriate Sample Size And Acceptance Number?
For example, in a theoretical quality inspection of 5000 units, the client chooses level III normal inspection and an AQL of 4.0.
The intersection of the respective Lot Size and General Inspection Level in Table A below shows sample size code letter M. Then, in Table B, we find row M, which shows the requisite sample size of 315. No more than 21 units from the sample size may fail inspection to meet AQL 4.0.
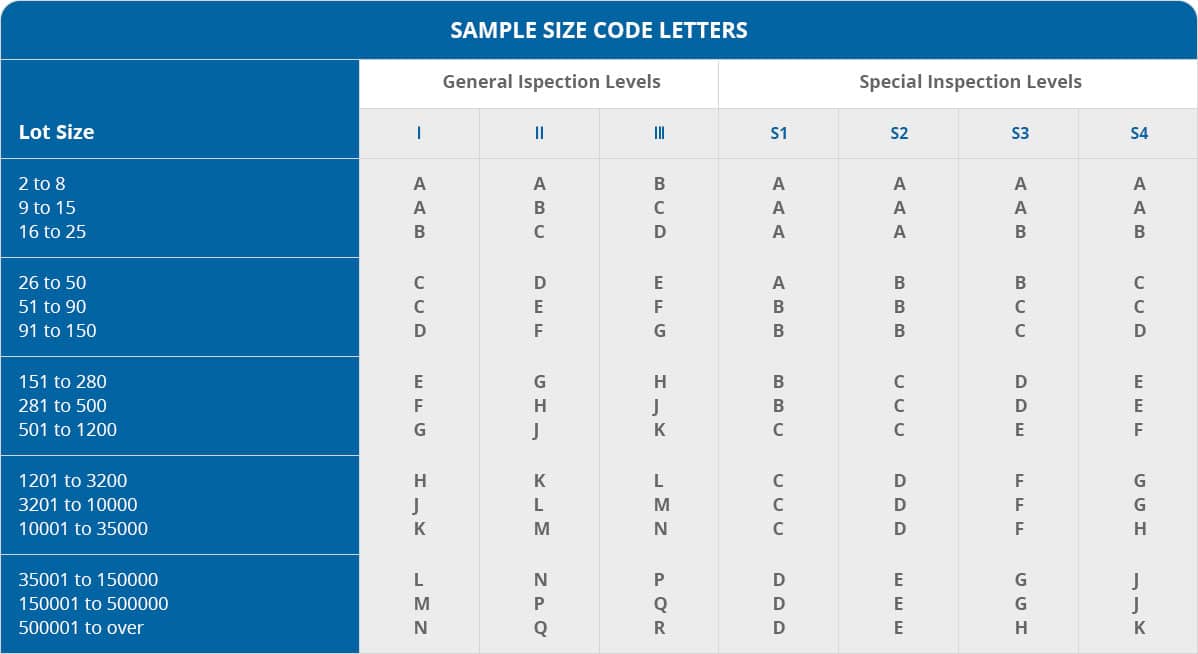
ANSI/ASQ Standard Z1.4 -2008
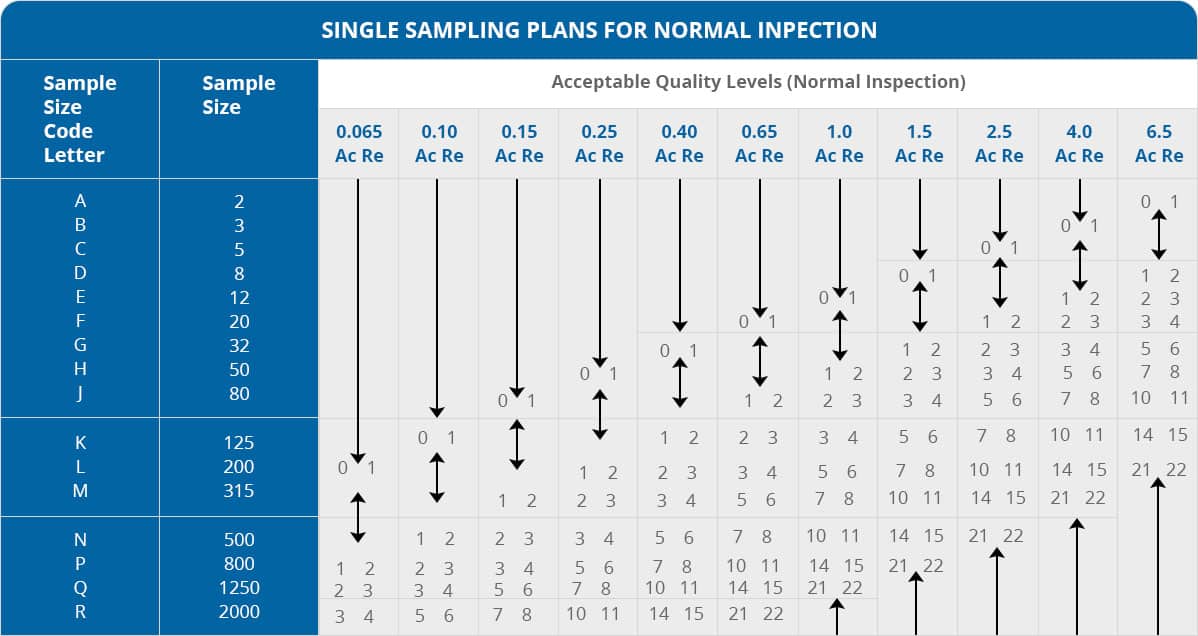
Use first sampling plan above arrow, if sample size equals or exceeds lot or batch size,do 100 percernt inspection.
Use first sampling plan below arrow AC: Acceptance number Re: Rejection number