The object of ISO9001 certification is the enterprise’s quality system, and the evaluation focuses on the operation process. This encourages organizations to improve the quality of products and services and helps to reduce waste and customer complaints. Encourage internal communication and improve employee morale. ISO 9001 certification is used to prove that the organization has the ability to provide products that meet customer requirements and applicable regulatory requirements, with the purpose of improving customer satisfaction. Therefore, we have sorted out 20 common problems in the process of ISO9001 certification audit and daily audit.
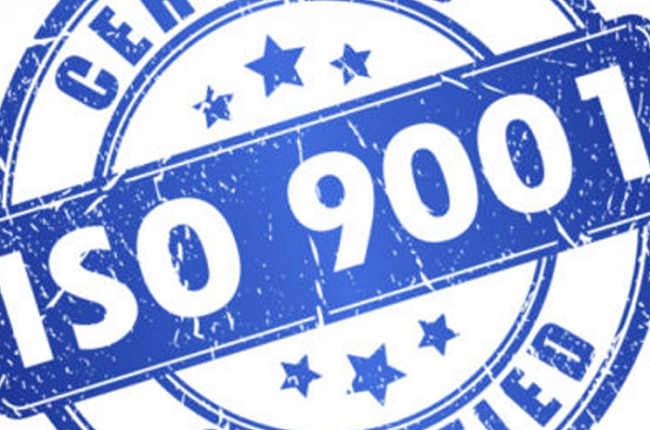
Common Problems Of ISO 9001 Certification Audit
1. Document control
A. Approval, distribution and change of internal documents:
- Engineering drawings have been issued and used without approval.
- The operation instructions are not distributed to specific operation posts.
- The operation instructions hanging on the posts at the production site are not controlled.
- The process document is changed directly on the document, and the document change procedure is not implemented.
B. Identification, collection and distribution of external documents:
- Fail to fully identify and collect national / international and industrial standards related to products.
- Failure to distribute external documents to relevant departments, such as quality control department and production department.
2. Filling, management and preservation of quality records
1) The quality records are altered.
2) Quality records are not kept for a specified period.
3) Failure to keep according to the storage period and failure to provide destruction records upon expiration.
3. Statistics and analysis of quality objectives
1) The quality objective statistics failed to provide the original data and failed to grasp the authenticity of the final objective statistics.
2) There are statistics on quality objectives, but no analysis is carried out.
4. Management review
1) Incomplete input information of management review or failure to provide input data.
2) The management review host is not the top management, and fails to provide the authorization certificate of the top management to the host (when it is not the top management itself).
3) Relevant evidence that no measures have been taken for the matters decided in the management review, such as corrective or preventive measures.
4) There is no record of the tracking results of the matters decided in the last management review.
Human resource management
1) Failure to specify the responsibilities, authorities and ability requirements of each post according to the actual post.
2) The training was planned and implemented as planned, but the implementation effect of the training was not evaluated
3) No competency requirements are specified for personnel in special posts, and the training and assessment evidence of these personnel are not provided.
4) The requirements for annual qualification examination of special operation personnel (electricians, welding/cutting workers, lifting workers, etc.) were not tracked in time, and the qualification certificates of individual special operation personnel were not reviewed or expired.
6. Infrastructure management
1) New production equipment is put into use without acceptance;
2) No maintenance requirements are specified for the equipment;
3) Special equipment fails to provide evidence of regular verification.
7. Work environment management
1) For the site with temperature and humidity requirements, there is no thermometer and hygrometer, so it is impossible to master the temperature and humidity status.
2) The lighting of the post of color difference inspection is not a special light source for inspection, which does not meet the requirements.
3) There are dust-proof requirements on the production site and storage site, but it is found that there is dust on the products stored on the site.
8. Product realization planning
1) Failure to set quality objectives according to product categories or characteristics.
2) Although there is product realization planning, the data are scattered and disorderly, and the relevant responsible person is not familiar with (or even unclear) the requirements of product realization planning.
3) The modification of relevant documents caused by engineering change is not carried out in accordance with the requirements of the approval procedure, and there is the phenomenon of private change. Some relevant documents have been modified and some have not been modified, and the modification is not complete.
4) The quality control points of products are not planned, and the time for verification, confirmation, monitoring, measurement, inspection and test is not determined.
9. Customer related processes
1) The requirements of laws and regulations related to products (including national / international, industrial standards and specifications of products) are not determined or identified adequately.
2) Unclear post delivery activities (including measures such as those specified in the warranty terms, contractual obligations) and additional requirements deemed necessary by the company.
3) When the customer does not provide documented requirements, there is no evidence to confirm these customer requirements. The oral contract was not reviewed.
4) The enterprise fails to plan the operation requirements of contract review according to the characteristics of its own business process, which is too formalistic and has no practical significance.
5) When the product requirements are changed, the relevant personnel are not informed of the changed requirements in time.
6) The customer’s feedback (including customer complaints) was handled, but the handling results were not communicated with the customer.
10. Design and development
1) General problems in design and development planning:
- The responsibilities and authorities of the members of the design team are not specified.
- The requirements of design and development progress are not clear, and the design and development plan is not adjusted in time according to the progress of design and development.
- The timing of review, verification and confirmation activities was not planned during planning.
2) The input information of design and development is insufficient, such as the requirements of laws and regulations applicable to the product are not fully identified.
3) The approval of design and development output before release is not perfect, for example, the drawing only has the name of the preparer, but the reviewer and reviewer have no signature.
4) The records of design and development review, verification and confirmation are incomplete and fail to be carried out according to the planning requirements. The improvement proposed in these processes is not recorded.
5) Failure to conduct appropriate review, verification and confirmation as required after design and development changes.
6) The design and development change causes the change of relevant documents, fails to revise the relevant documents in time, and fails to notify the relevant personnel of the change requirements in time.
11. Procurement process control
1) The type and degree of control of suppliers and purchased products are not determined according to the impact of purchased products on final products.
2) The selection and evaluation of suppliers does not cover all material suppliers and outsourcers, especially the evaluation of outsourcers.
3) Relevant supporting documents provided by the supplier (such as quality assurance, material inspection report, qualification certificate, etc.) are not updated in time to ensure their effectiveness.
4) Failure to timely inform the supplier of the requirements for purchased products, or incomplete requirements, resulting in the supplier’s failure to supply as required.
5) The quality problems of the supplier are fed back to the supplier, but the effectiveness of the improvement measures taken is not verified in time.
6) The verification requirements (verification method and timing) of purchased products are not clear, and there is a phenomenon of warehousing before verification.
12. Process control of production and service provision
1) The operation instructions required by the production and service site are not issued / hung / posted in time, and the operation instructions used on site are not replaced in time according to the actual products produced.
2) The fault equipment is not marked with its status.
3) The inspection instruments and monitoring equipment used on site have no identification of verification/calibration status.
4) Failure to provide evidence of monitoring process parameters in the production process.
5) The operators of special processes fail to work with certificates or work without training.
6) The special process was not confirmed, and the special process was not reconfirmed after the production conditions changed.
7) The identification of product status (inspection status and processing status) in the production process is incomplete.
8) The production batch, order number, production date and other information of the product are incomplete.
9) Lack of product protection, such as damage to bottom products and product packaging caused by high stacking of products.
10) The identification of customers’ property is unclear, and any abnormality is not reported to customers in time.
13. Control of monitoring and measuring equipment
1) Incomplete identification of the equipment included in the control scope of monitoring and measuring equipment, such as pressure gauge/temperature control gauge in the machine, Ammeter/speed control gauge of electric welding machine, temperature control gauge, tachometer of conveyor belt and other monitoring equipment failed to be included in the control scope.
2) There is no plan for the calibration/verification of monitoring and measuring equipment, and it is not determined whether it is internal calibration or external calibration.
3) There is no calibration/verification specification for internal calibration, nor can it be traced back to national standards or international standards.
4) The internal school staff have not received professional training and have no internal school staff qualification certificate.
5) The monitoring and measuring equipment is lack of status identification, so it is impossible to determine whether it is within the validity period of calibration/verification.
6) The protection of precision instruments is not enough, such as anti-vibration, dust prevention and other measures.
14. Customer satisfaction
1) The monitoring and measurement method of customer satisfaction is too single, and only the investigation method of customer satisfaction form is adopted, without considering customer complaints/complaints, return of goods, return visit to customers, evaluation report of customers on suppliers and other information.
2) The coverage of customer satisfaction survey is not representative, and only important customers are investigated.
3) Customer satisfaction is investigated, but no evidence of how to use this information is provided, such as how to improve the work.
15. Internal audit
1) The audit scope of internal audit is reflected in the plan, but the checklist is not fully covered, especially in the terms that need to be audited are clearly stated in the plan, but the checklist and records are not reflected.
2) The arrangement of auditors is unreasonable and fails to consider the professional ability of auditors.
3) The time arrangement in the audit schedule is unreasonable, and the time is not arranged in combination with the complexity and scope of responsibility of the audited department.
4) The top management did not attend the first and last meetings.
5) The fact of nonconformity in the nonconformity report issued by the internal audit is not clearly described and has no re-inspection, and the specific circumstances of nonconformity are not clearly described.
6) Insufficient rectification of nonconforming items: the cause analysis is not in place and the corrective measures are unreasonable.
7) The follow-up verification of nonconforming items was not arranged in time, and the verification result report was not clear.
16. Process monitoring and measurement
1) The production process is monitored, but the analysis of the monitored data is insufficient, and the ability to monitor the production process is not available.
2) The monitoring of the system operation process is not planned and monitored, and only the evidence of internal audit can be provided.
3) The statistics of process performance indicators are insufficient and the process capability is not mastered.
17. Product monitoring and measurement
1) The inspection post has not obtained the inspection/test operation instruction.
2) The ability of inspectors is insufficient and they do not know enough about the use of AQL.
3) The test data in the inspection report is insufficient, and the items with specific values have no specific values.
4) Failure to conduct 100% inspection and test according to the items specified in the inspection and test specifications/standards.
5) In case of emergency release (or exceptional release), the evidence approved by authorized personnel is not provided, and the traceability identification is insufficient.
6) The inspection report lacks the signature of the person authorized to release.
18. Control of nonconforming products
1) At the production site, the identification of nonconforming products produced in the production process is unclear and not recorded in time.
2) The nonconforming products were disposed of, but the supplier was not required to take improvement measures. Some delivered the nonconforming report to the supplier, but failed to track and verify its effectiveness in time.
3) The nonconforming products in the production process are reworked or not verified again after repair. Some have been verified but failed to provide re-verification records after rework/repair.
4) There are rework and repair phenomena in the manufacturing process, but there is no record of the rework and repair process.
5) There is special purchase (concession acceptance) of materials in the production process, but the evidence of approval by authorized personnel is not provided.
6) The products returned by customers were directly returned to the warehouse without re-inspection and non-conforming product procedures.
19. Data analysis
1) Customer satisfaction was investigated and counted, but the evidence of analysis was not provided.
2) The quality control department has made statistics on the qualified rate and unqualified rate, but failed to provide evidence for the analysis of unqualified conditions.
3) Insufficient understanding of the requirements for data analysis of process performance, only statistics and analysis of the performance of the production process, such as rework rate, repair rate and scrap rate, but there is no evidence of data analysis for the process performance of other departments.
4) Make statistical analysis on the qualified rate and timely rate of incoming goods, but fail to analyze the supply capacity of a single supplier separately.
5) The statistical analysis of quality objectives is only carried out for the items that fail to meet the objectives and requirements, the lack of data analysis for the achieved items, and the failure to make efforts to find opportunities to take preventive measures.
6) The application of statistical methods and technologies is narrow, and the statistical methods are too monotonous and lack of scientificity.
20. Improvement
1) Most enterprises have no record of the implementation of preventive measures. Failure to grasp the timing of the implementation of preventive measures.
2) The regulations on when to take corrective and preventive measures are not clear and arbitrary.
3) The cause analysis in the improvement report is not in place, stays on the surface, and lacks comprehensive and in-depth analysis.
4) When formulating corrective measures, many personnel only consider emergency measures – correction, but lack measures to prevent a recurrence.
5) Many people are confused about the concepts of correction, corrective measures and preventive measures. There is the coexistence of corrective measures and preventive measures in the report of corrective measures.
6) Corrective/preventive measures have been implemented, but the implementation results are not recorded.
7) After the implementation of corrective/preventive measures, the implementation effect is not verified.