Form Tracing & Roundness Testing Services
The measurement of shape and position errors plays a very important role in the precise measurement of geometric quantities. A roundness tester (from tracer or Talyround) is a necessary measuring instrument to ensure the quality of workpiece behavior error in the precision machinery industry. It can measure multiple form and position errors, equipped with proprietary tracking and covering nominal or covering parts to parts, automatic alignment, data processing, and rapid automatic measurement. It is a technology-intensive high-precision and high-efficiency automatic testing equipment integrating machinery, light, electricity, liquid and gas.
The Do We Need Roundness Testing & Forming Tracing
The circular cross-section of an engineering component is one of the most fundamental and significant types of engineering components. Circles may be found in a variety of applications, particularly on bearing surfaces such as rotating shafts and ball bearings, which are often used. An exceedingly significant assessment is the measuring of out of roundness (sometimes known as “roundness” in certain circles). Examples include rotating bearings with inaccurate circular components, which tend to make noise and may fail early if not maintained properly. To guarantee that such components perform as intended, it is critical to test their roundness with precision before using them.
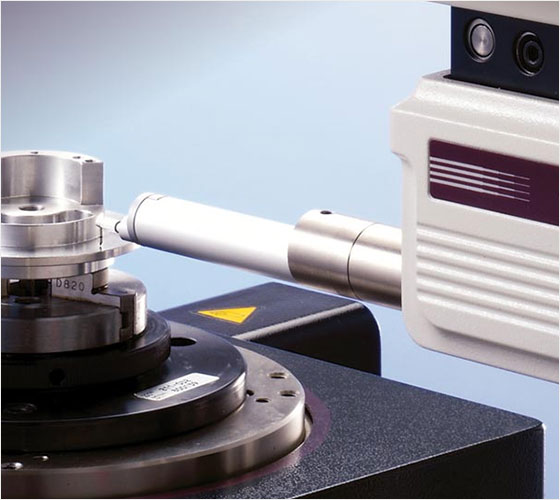
Form & Roundness Measurement Types
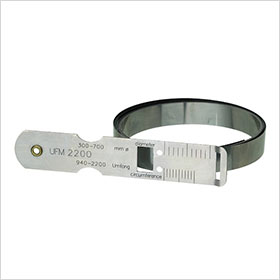
Diameter measurement
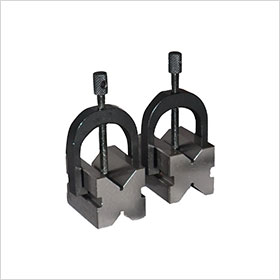
Vee-block
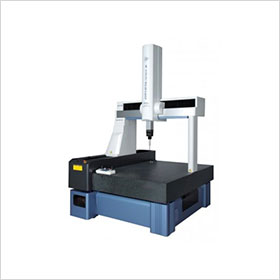
Coordinate Measuring Machine
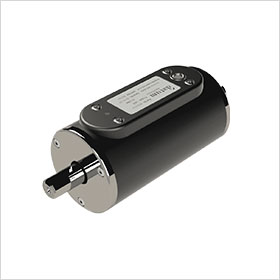
Rotational Datum
The Advantages of Using Roundness Testing & Forming Tracing
With the form tracing and roundness testing machines, they can measure form more precisely and efficiently than they ever have in the past! They have the ability to measure roundness, straightness, concentricity, runout, and cylindricity with extreme precision down to.00004″ or.001 mm. Surface inspection with high accuracy allows you to get a deeper understanding of your components and identify the source of any problems you may be experiencing. Working with delicate materials, such as rubber and thin polymers, that may be damaged by human contact is a breeze. By holding the component in a tight yet delicate fixture in the form tracing, the forming tracer can get the most exact measurements without distorting the component.
The Disadvantages of Using Roundness Testing & Forming Tracing
A restriction to the precision of this measurement exists due to the fact that the value is an average of two-point measurements. It is also possible that inaccuracy will develop as a result of changes in how the micrometer measuring terminal is positioned on the target surface. In order to examine the data collected, it is also necessary to input it into a computer.