Even if shape data is acquired with a 3D scanner, it cannot be used for design and inspection as it is. You need to edit the 3D scanning data. In this post, we will introduce the basic tasks of data processing after 3D scanning.
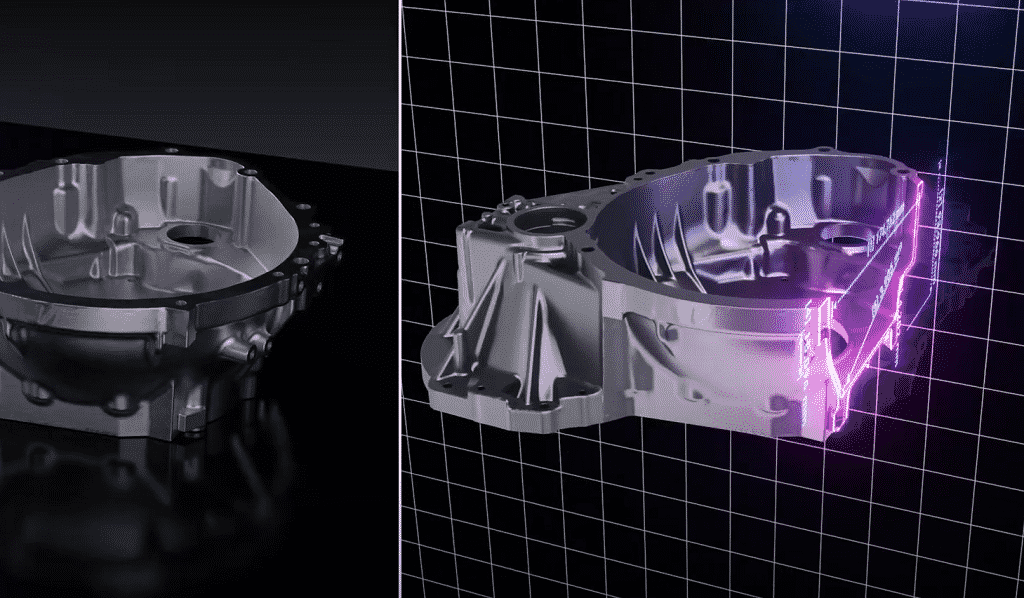
Necessity of Data Processing after 3D Scanning
The state of the data just acquired by the 3D scanning is “point data” with 3D coordinates of X, Y, and Z. The collection of point data is called a point cloud. This time, as a process after 3D scanning, we will introduce the process of point cloud data, conversion from point cloud data to mesh data, and editing of converted mesh data.
How to use the data acquired by the 3D scanner is described in the previous article. For example, it can be used in quality inspection, 3D printing, CAE, and 3D CAD data to help with design. In order to do this, the data acquired by the 3D scanner must be processed properly and passed to the next step. This time, we will take a closer look at the basic data processing work (point cloud data processing, mesh data processing) after 3D scanning.
Processing of 3D Scanning Point Cloud Data
- 1. Delete unnecessary parts
When scanning in 3D, tables and peripherals on which the measurement material was placed may also be converted into point data, or extra noise may enter as data. We will delete this unnecessary data. As a specific task, select the place you want to delete and erase it, select the part you want to keep, and delete the other superfluous things at once.
- 2. Synthesis / thinning
The data acquired by the 3D scanner can be said to be a state in which multiple photos taken many times overlap. By combining the acquired data by shooting from multiple angles, 3D data of one part shape is created. Taking a photo as an example, it is an image that recognizes the same parts of the image when compositing, aligns them, and stitches them together.
If you want to digitize all part shapes by 3D scanning, you may need to measure the top side of the shape first, and then measure the back side, etc., and then synthesize multiple measurement results later. The synthesis work itself may be performed while performing a 3D scan, or after a 3D scan. In addition, there are some that perform synthesis work manually and those performed automatically, and it depends on the model and software of the 3D scanner used, or the object and situation to be measured.
If synthesis does not work, accurate data cannot be produced. Basically, the same part is recognized and aligned on the software, but in the case of a shape that is difficult to align, accuracy may not work and the accuracy may be reduced. To prevent this, some 3D scanners use “markers” to make it easier to synthesize later (see previous article).
As you can see from the above explanation, if you want to synthesize later, you must 3D scan while changing the angle so that the previously taken part enters. Therefore, a lot of point data is collected in the part where it overlaps by all means. At this rate, the handling is bad and the data is heavy, so unnecessary points must be thinned out and the point density uniform.
- 3. Mesh data conversion
After processing 1. and 2. step, you can create mesh data such as STL data, which is triangulated by connecting the acquired points with straight lines and pasting faces, or polygon data, which is formed by a set of polygonal faces. In most cases, you can easily convert the data by clicking the [Export] button. However, depending on the amount of 3D scanned data, it may take from a few minutes to several dozen minutes to process.
Processing of 3D Scanning Mesh Data
While tasks 1. to 3. are mainly performed on the software that comes with the 3D scanner, tasks (4) and later, which will be explained here, are often performed on other software, such as “mesh editing software”, “polygon/STL editing software”, and “reverse engineering software”. These are called “mesh editing software,” “polygon/STL editing software,” or “reverse engineering software. In some cases, these software programs are used to perform the tasks 1. through 2. above. In particular, for “Delete unnecessary parts”, we sometimes remove minute edges and faces that have been created by the mesh data.
We will now explain the work from process 4. First of all, we would like to add that the work from Smoothing onwards can be done on the entire data or on a part of it. Also, please read this article with the image in your mind that mesh data is a collection of surface data that is created by connecting points with straight lines to form a polygon. The key is to use “straight lines” instead of curved lines between points.
- 4. Smoothing
Data acquired by a 3D scanner may have minute bumps on the surface due to noise and other factors, resulting in a rattling and rough surface, so we use a function called “smoothing” to smooth the surface.
The smoothing process is performed by specifying the length and angle of edges and strings, and setting tolerances for how much precision is to be maintained. However, be careful not to overdo the smoothing, as it may result in a large error from the original shape. For example, corners that should be rounded may become rounded, or the R-value may become larger than the original fillet. If you have a good software program that pays attention to details, it will automatically recognize and smooth the image nicely.
- 5. Mesh division (remesh)
Basically, the process is to simplify the data by thinning it out, etc. to lighten the mesh data. However, if the data acquired from the 3D scan is too coarse and choppy, it is necessary to perform mesh splitting to set up finer meshes and increase the number of meshes.
For example, imagine a circle. If there are only six points that make up the mesh, the mesh will be a hexagon instead of a circle because it is linear data. In this case, you can make it closer to a circle by doubling or tripling the number of points, right?
In the case of STL, which is triangular surface data, it is desirable for the post-processing to have an equilateral triangle mesh shape, so the mesh is sometimes re-divided and repaired so that it is as equilateral as possible. This process is called “remeshing”
- 6. Fill in the blanks
3D scanners are generally not good at capturing the depths of holes or intricate shapes because they measure surface shapes by triangulation, which uses reflections and distortions of light and lasers. As a result, the areas where data could not be acquired are holes (missing), which can be a problem when using the data for inspection, reverse engineering, or 3D printing. This is where the hole-filling process comes in.
The hole filling process is done by predicting the shape of the missing part based on the shape of the surrounding area, so that the hole is smoothly connected. How well the software can fill in the holes without causing any discomfort will indicate its capabilities, and will be a key factor in the selection process.
- 7. Bridge
The shape is created by connecting the edge of the face to the edge of the face, similar to the lofting function of a surface in 3D CAD. This is done when the entire perimeter is not enclosed, such as a hole.
- 8. Invert the front and back of the surface
Since mesh face data has a front and back and a normal direction, problems may occur if the front and back are reversed when joining meshes or defining thickness. If the front and back of the mesh face data is reversed, it may be corrected.
- 9. Extracting elements and editing boundaries
3D scanned data does not recognize planes and holes. Therefore, we may calculate averages from the acquired data and extract elements such as holes and planes to facilitate their use for inspection and reverse engineering. We may also edit or modify the boundaries of the geometry.
- 10. Automatic cleaning (repair)
There is also software that will automatically perform the processes described so far. The performance of the automatic processing depends on the software. If it can be done automatically, it can save a lot of man-hours. If you are going to select a software, I recommend that you conduct a 3D scan of the shapes that you often handle in your company and benchmark the automatic repair to verify the results.
Also, not everything can be optimized automatically, so please select software after properly checking not only the functionality of the automatic repair but also the manual operations introduced here.