The notion of AQL (Acceptance Quality Limit) is one of the most important in terms of quality inspections. It is a statistical method that allows determining the quality of production. Identifying the maximum percentage of defects that can be considered satisfactory for the chosen sample.
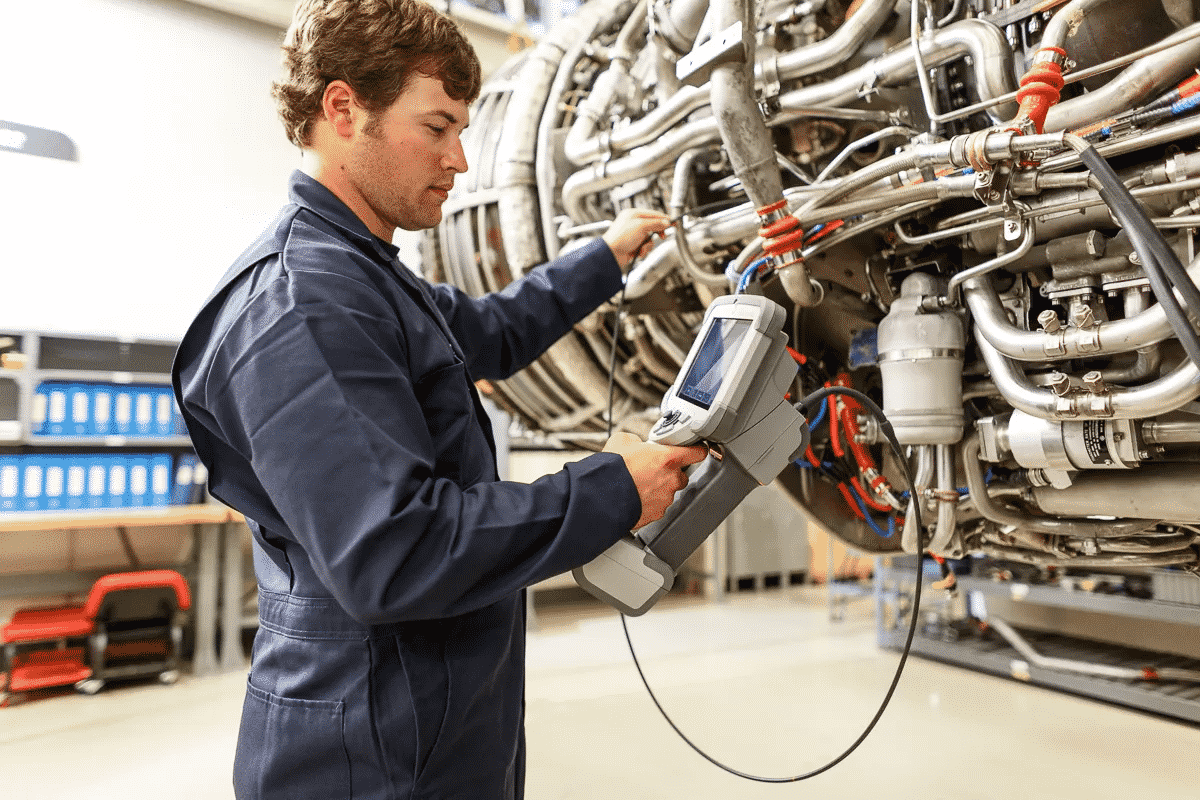
Acceptable Quality Level System (Acceptance Quality Limit)
Technical and technological progress today guarantee very high and, above all, constant quality levels. However, each manufacturing process has its percentage of defects, even if it is minimal. No manufacturer can guarantee 100% defect-free production. It is not possible to completely control the performance of each product, as many test methods destroy the product. This type of quality control is called destructive testing. Therefore, these test procedures can only be applied to a small but representative part of the production. To determine the AQL – the “Acceptable Quality Level” a partial quantity is taken according to a well-defined procedure, from the total production lot by sampling. These samples are controlled according to certain standards and specifications.
What is AQL (Acceptance Quality Limit)?
AQL (Acceptable Quality Level) is the most widely used standard for product inspections. This standard uses the concept of AQL or Acceptable Quality Limit. According to which the maximum percentage of defects that can be considered satisfactory for the selected sampling according to pre-established tables is established.
What is AQL Table?
The sampling method establishes on the one hand the number of parts to be inspected according to the volume of production and on the other the Acceptance Level chosen. Depending on the number of defects detected for each category and the number of defects allowed (figures given by the AQL tables) the inspection will be approved or rejected.
By applying the tables, the number of pieces to be selected randomly is calculated according to the level of acceptance chosen. Level I being the strictest and Level III the least. Level II being the most commonly accepted. In addition to these three levels the table considers four other Special Levels. The latter are used in the event that you want to make a smaller sampling or when the level of defects that is expected to be found can be accepted. They are used for example to make the sample to check the composition of the tissue.
How To Use the AQL System: Two Tables For AQL Calculation
The AQL system is presented in the form of tables. They help determine the size of the sample to review according to the total amount of the order and its level of severity.
- AQL Table A – Depending on the Level chosen, the table assigns a letter code so that with the following table it can be determined the number of non-conforming pieces that will be accepted.
- AQL Table B – The second table establishes the number of non-conformities accepted according to the chosen Acceptance Level.
How Are Product Sampling Defects Classified?
The acceptance levels are chosen according to the type of defect: Minor, Major or Critical. The AQL acceptance level establishes the percentage of Minor, Major and Critical nonconformities that are accepted to approve or reject a production.
Generally the percentages of defects that are used are:
- Critical (represents a hazard) – 0%
- Major (may alter the proper functioning of the product) – 2.5%
- Minors (corresponds to a difference with respect to what is established, does not affect the usability of the product) – 4%
AQL Table I – Sampling Plan (Sample Size Code Letters)
In order to determine the sample size, we will need to look at the first table. The column on the left side corresponds to the range of units in total of the order. The other columns (3) correspond to the different levels of quality that are I (the most flexible), II and III (the most rigorous). It is worth mentioning that most AQL users choose level II.
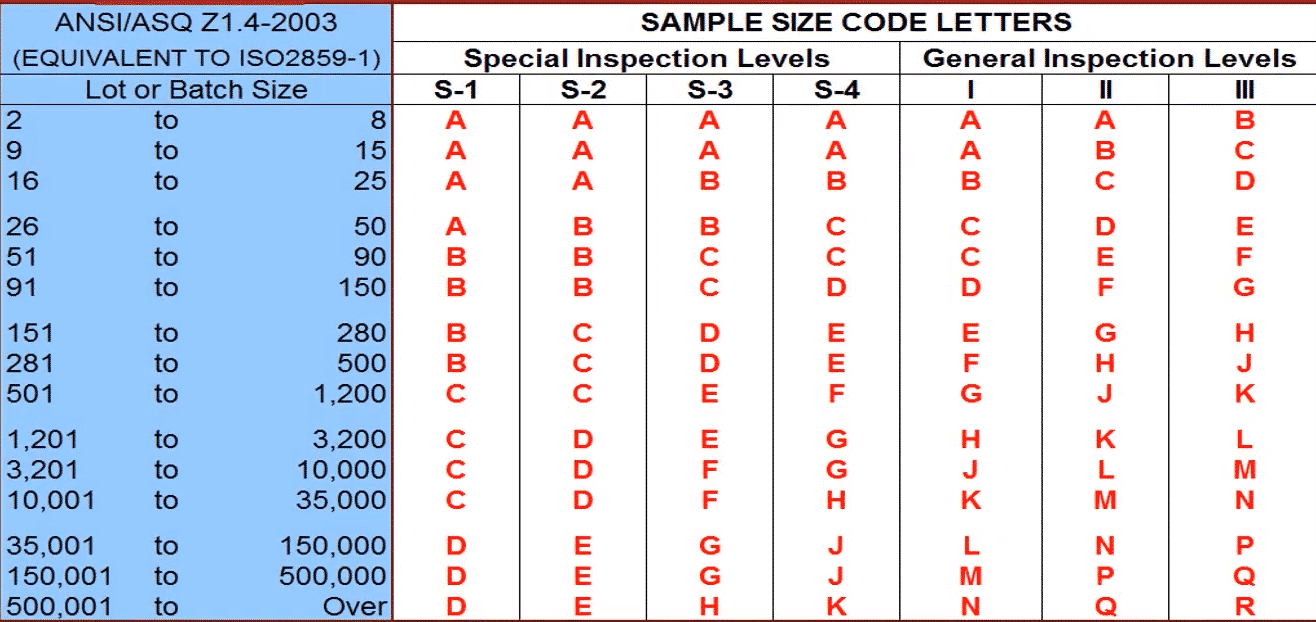
Example: if the order is 5,000 units, and we apply level II, the AQL system indicates the letter “L”, which we can find in table 2. The letter “L” indicates that the sample to be reviewed is 200 units.
AQL Table II – Sampling & Acceptance Level (Single Sampling Plans for Normal Inspection)
The second table calculates the number of pieces accepted based on the sampling acronym and the acceptance level.
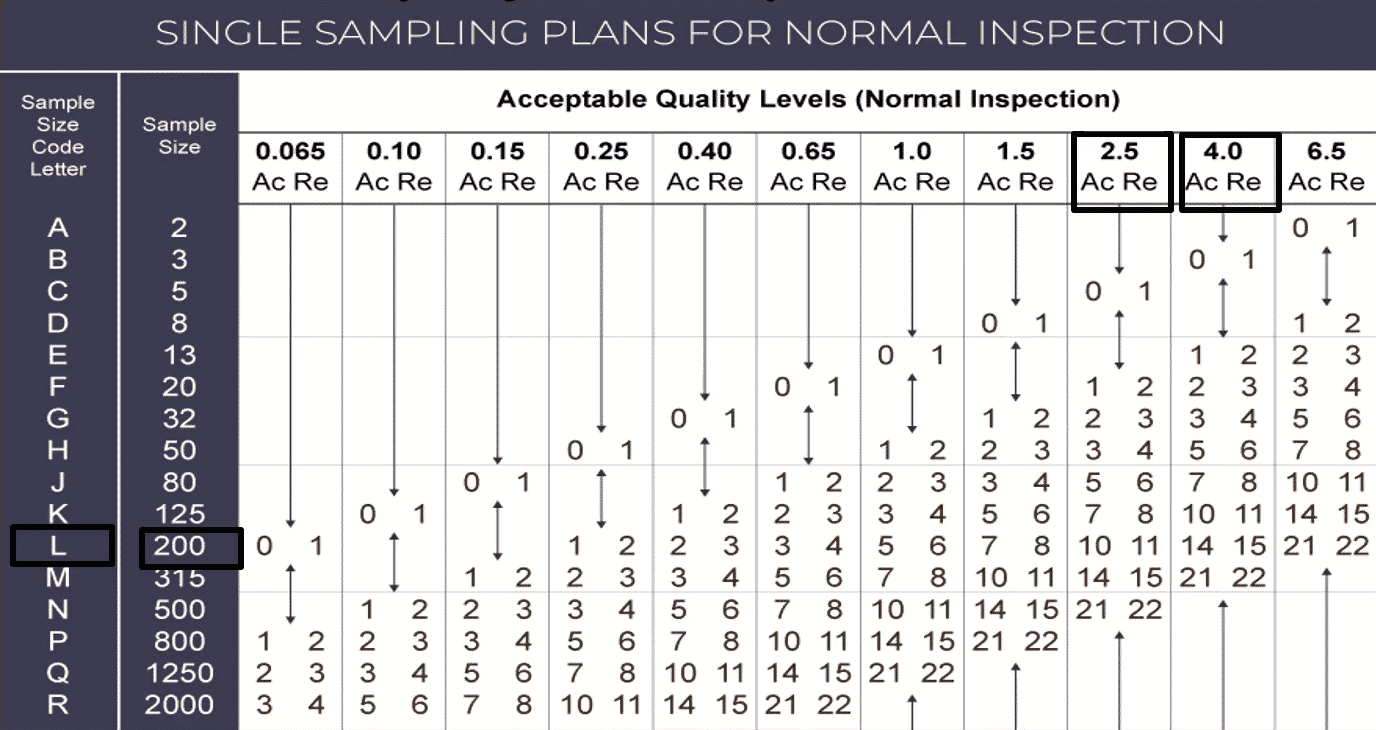
At the top of Table 2 we can see the levels of defects (from 0 to 6.5). Most users choose the default levels 0/2.5/4.0. If we use this defect level for 200 units, and we see that there are more than 0 critical defects, 10 major defects and 14 minor defects, we must refuse production or shipping and solve the problem with the supplier.
How To Use The AQL Table: Certain Conditions
We already know its definition and its role, so we only need to understand how to use the AQL table. Actually, the AQL table result is reliable only if some conditions are rigorously respected during the inspection of the products.
To ensure the reliability of the AQL table result it is mandatory:
- Avoid grouping several references in the same AQL table
- Each type of product comes from a different production process, therefore they must be controlled separately.
- Select the sample randomly based on the total amount
- The inspection must be done on a sample of finished products randomly selected from the entire manufactured lot.
- Follow the “square root” rule
- The number of boxes in which the samples are selected is based on a mathematical method: the square root of the total number of boxes.
- Define what is acceptable and unacceptable according to the buyer
- The buyer must classify the defects so that the result is as reliable as possible. If the opinion is based on the inspector’s interpretation, the result may be different: “fail” even with defects acceptable to the buyer, or “pass” when these defects are unacceptable to the buyer.
- Perform an AQL control for every 50K units maximum
- Choose an AQL level II or III
AQL Table Is Just A Statistical Tool
To fully understand how to use the AQL table, we must bear in mind that it is a tool whose result is exclusively statistical. Consequently, when the AQL result is “pass”, the buyer must always keep in mind that the number of defective products could be higher, or lower, if the inspector has controlled all the merchandise.
Due to the numerous conditions to be respected and the fact that the AQL table is only a statistical tool with its limitations, the buyer has to carefully study the received inspection report. All the details are important, in particular the list of AQL defects and the photos illustrating them. On the other hand, for each inspection, the buyer must ask himself the following: Taking into account that the percentage of defects could be higher over the entire order, do I consider these defects acceptable?