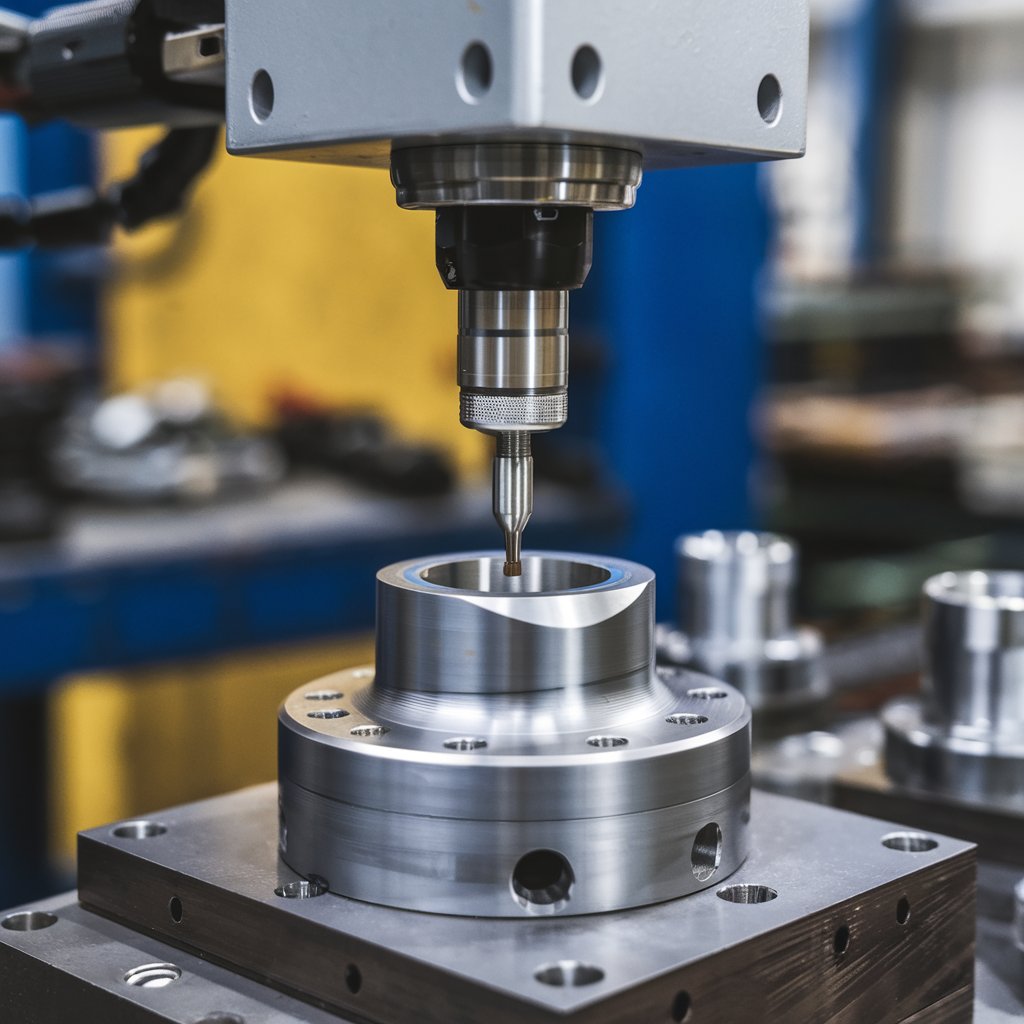
When it comes to precision manufacturing, there’s no room for error. Every component, no matter how small, needs to meet exact specifications. That’s where Coordinate Measuring Machines (CMM) come in—a game-changing technology that ensures every part leaving the production line is flawless.
CMM inspection has become a cornerstone of modern quality control. It uses a probing system to measure the physical geometry of a part against its design specifications. This process isn’t just about identifying flaws; it’s about guaranteeing that the final product functions exactly as intended, whether it’s a small automotive component or a complex aerospace part.
Why is this level of accuracy so important?
Imagine a gear that doesn’t fit perfectly in an engine or a medical device component that’s even slightly off. These aren’t just inconveniences; they can cause safety issues, downtime, or costly recalls. With CMM inspection, manufacturers can catch deviations early in the process, ensuring that every part meets the strictest standards before it’s shipped out.
What makes CMM so versatile is its ability to handle a variety of materials and shapes. Whether it’s measuring flat surfaces, intricate curves, or deep recesses, CMM provides accurate data in a fraction of the time it would take with manual tools. Plus, it works with an impressive range of materials, from metals and plastics to ceramics and composites.
The technology behind CMM has advanced significantly over the years. Modern machines now integrate with CAD software, making it easier than ever to compare real-world measurements with digital designs. Automated systems can even handle multiple parts in a single run, reducing downtime and boosting productivity.
But the real value of CMM inspection isn’t just in the data—it’s in what you do with it. Detailed inspection reports can guide production adjustments, highlight process inefficiencies, and even help with predictive maintenance by identifying wear and tear in tools. For manufacturers, this means fewer defects, less waste, and more confidence in the final product.
CMM inspection is more than just a quality check—it’s an investment in excellence. By ensuring that every part meets exact specifications, manufacturers can build trust with their customers, improve operational efficiency, and stay ahead in an increasingly competitive market. If precision matters in your business, it’s clear: CMM inspection isn’t just an option; it’s a necessity.
In the world of precision manufacturing, meeting exact specifications is non-negotiable. Every component, no matter how complex or simple, must align perfectly with its design to ensure safety, reliability, and performance. Enter Coordinate Measuring Machines (CMM)—a revolutionary technology that’s now the backbone of modern quality control, delivering unparalleled accuracy and consistency in measurement.
CMM inspection works by using a probing system to capture detailed measurements of a part’s physical geometry. These measurements are then compared to the original CAD (Computer-Aided Design) model, ensuring every curve, edge, and feature is within tolerance. Whether you’re producing aerospace components that must perform in extreme conditions or medical devices where a fraction of a millimeter can save lives, CMM inspection guarantees the precision required for high-stakes applications.
One of the standout advantages of CMM technology is its flexibility. A single machine can measure parts of all shapes and sizes, from flat surfaces to intricate 3D geometries. Its probes can navigate tight spaces, complex curves, and even hard-to-reach internal features, making it indispensable for industries like automotive, aerospace, electronics, and medical manufacturing.
The materials it can handle are equally diverse. CMM inspection is suitable for metals like aluminum, steel, and titanium; composites used in lightweight, high-performance applications; and even delicate materials like ceramics and plastics. This adaptability ensures that no matter the project, CMM can deliver precise and reliable results.
But what truly sets modern CMM systems apart is their integration with advanced technologies. Today’s machines are equipped with sophisticated sensors and software that allow real-time analysis and seamless communication with CAD systems. Automated CMM systems can measure multiple parts without manual intervention, dramatically reducing inspection times and allowing manufacturers to scale up production without sacrificing quality.
For many companies, the benefits of CMM inspection go far beyond simple quality assurance. By identifying defects or deviations early in the manufacturing process, CMM systems can prevent costly rework or material waste. In high-volume production, even a small improvement in efficiency or accuracy can lead to significant cost savings. Moreover, detailed inspection data can uncover patterns, such as tool wear or process inefficiencies, that can guide future improvements and reduce downtime.
CMM inspection also plays a critical role in compliance with industry standards and regulations. For industries like aerospace, automotive, and medical devices, demonstrating strict adherence to quality requirements isn’t just good practice—it’s a legal necessity. The detailed reports generated by CMM systems provide clear, auditable records that give manufacturers and their clients peace of mind.
CMM’s Role in the Shift Toward Smart Manufacturing
As manufacturing continues to evolve, CMM systems are becoming a cornerstone of Industry 4.0. The integration of CMM with IoT (Internet of Things) and AI technologies allows manufacturers to achieve even higher levels of precision and efficiency.
Imagine a factory where CMM inspection data is instantly shared with production machines, allowing them to adjust in real-time to stay within tolerance. Predictive analytics can use this data to forecast when a machine tool might need maintenance, reducing unplanned downtime and maximizing productivity. These smart manufacturing systems are no longer futuristic concepts—they’re becoming the standard for forward-thinking manufacturers.
How CMM Benefits Every Step of Production?
From prototyping to final assembly, CMM inspection adds value at every stage of the manufacturing process.
- Prototyping: During product development, CMM ensures that prototypes match their design perfectly. Early-stage measurements help engineers refine designs, reducing costly revisions later.
- Production: CMM ensures that each part produced on the line meets the required specifications, maintaining consistency even during high-volume runs.
- Assembly: By ensuring that all components are dimensionally accurate, CMM prevents misalignments or assembly issues that could lead to performance problems.
- Final Inspection: Before parts are shipped to customers, CMM provides a final layer of quality assurance, ensuring that every product is ready to perform as expected.
Making the Case for CMM Inspection
Investing in CMM inspection isn’t just about meeting standards—it’s about building trust and delivering excellence. Customers today demand more than just functional parts; they expect reliability, durability, and performance. With CMM inspection, manufacturers can confidently deliver on these promises, knowing that every part they produce has been measured and verified to perfection.
For businesses aiming to stay competitive, the precision, efficiency, and insights provided by CMM inspection are invaluable. Whether you’re a small manufacturer focused on niche products or a large-scale operation serving global markets, CMM technology can elevate your production processes and ensure that your products always meet the mark.
As manufacturing challenges continue to grow, the role of CMM inspection will only become more critical. It’s not just a tool for measurement—it’s a partner in ensuring the success of every project. So, the next time you see a perfectly engineered product, remember: precision like that doesn’t happen by chance. It happens because of technologies like CMM.
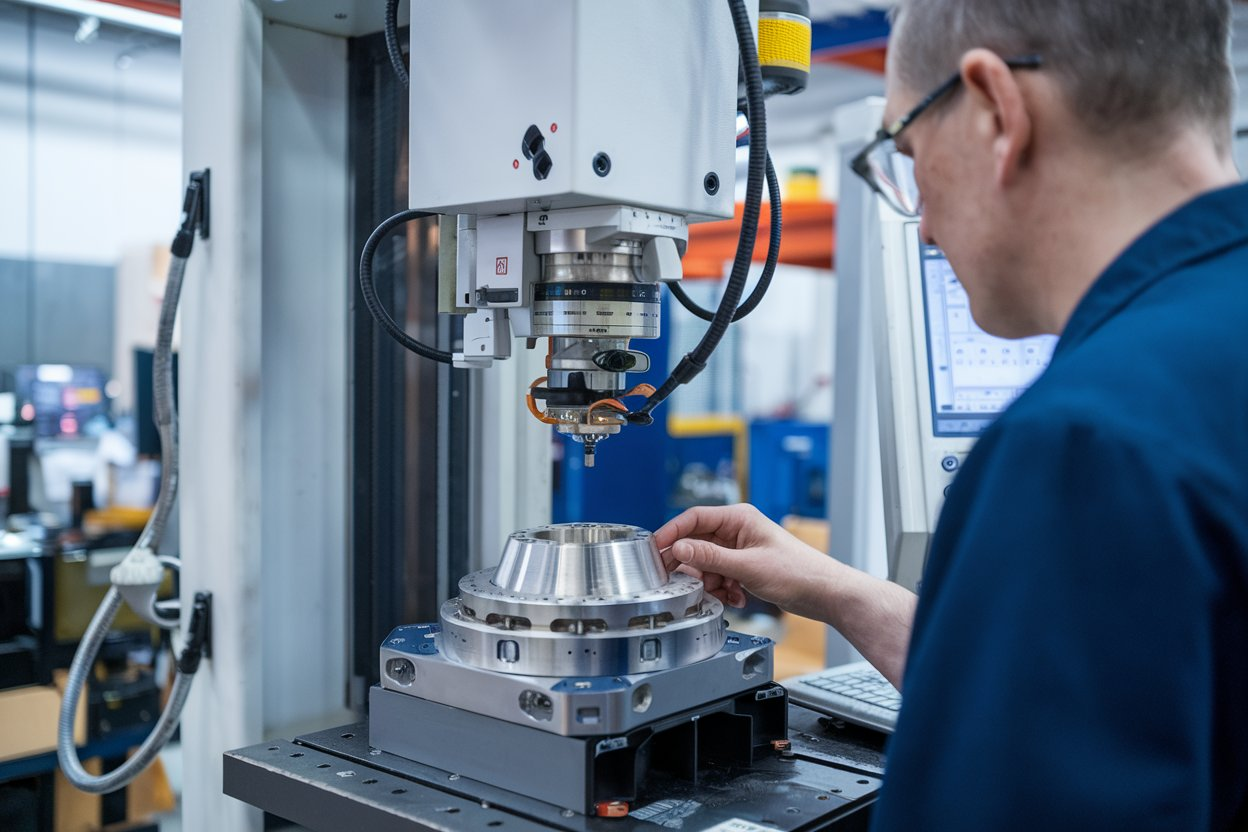