CMM measurement is more ideal than manual measurement instruments, such as micrometer, caliper, and altimeter, because using CMM to automate part measurement can reduce the demand for skilled personnel like CNC machine tools. Generally, experienced employees are responsible for CMM programming and setting, and the rest are operated by other employees.
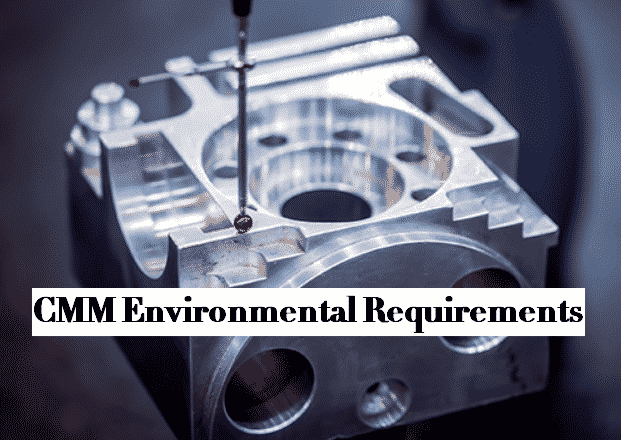
CMM Operation Environmental Requirements – Conditions for Using Coordinate Measuring Machine
The coordinate measuring machine is a kind of high-precision detection equipment, the environmental conditions of its machine room are very important to the results of the measuring. This includes detecting workpiece status and environment, temperature conditions, vibration, humidity, power supply, compressed air, and other factors. IPQC provides full CMM services including form tracing, part sorting, 3D laser scanning, color mapping, and more measurement and inspection options.
The physical shape of the detected workpiece has a certain influence on the measurement results. The most common are workpiece surface roughness and chips left by machining. Coolant and oil also affect the measurement error. Generally, dust and dirt can be concentrated on the measuring ball, affecting the performance and accuracy of the measuring machine. There are many similar situations that affect the measurement accuracy, most of which can be avoided. It is recommended to carry out necessary cleaning before and after the work of the measuring machine.
- Temperature conditions
The main environmental factor affecting the measurement is temperature. Since the ambient temperature of all geometric quantities and errors is defined as 20 ℃, this temperature must also be followed during the operation of the measuring machine, but this is not the case. The change of the ambient temperature of the measuring machine mainly includes the change of ambient temperature, the change of short-time temperature, the change of long-time temperature, and the change of temperature gradient. In order to ensure measurement accuracy, each measuring machine manufacturer has strict restrictions on this. In modern mass production, many measuring machines are directly used in the production workshop. In view of the conditions on the production site often can not meet the requirements for temperature, most measuring mechanism manufacturers have developed automatic temperature correction systems. The automatic temperature correction and compensation system monitors the grating of the measuring machine and the temperature of the detected workpiece parts and corrects the measurement results based on the standard temperature of 20 ℃ according to the temperature expansion coefficient of different metals. For rapid temperature or temperature gradient changes, compensation correction cannot be carried out.
- Vibration
As more measuring machines are used in the production site, vibration has become a frequent problem. For example, stamping machines, air compressors, or other heavy equipment around the measuring machine will have a serious impact on the measuring machine. It is difficult to detect small amplitude vibration. If it is confused with the vibration frequency of the measuring machine, it will also have a great impact on the measurement accuracy. Therefore, the manufacturer of the measuring machine has certain requirements for the vibration frequency and amplitude of the measuring environment. - Humidity
Relative to other environmental factors, humidity is not a big problem. In order to prevent oxidation and rust of block gauge or other metering equipment, it is required to keep the ambient humidity below 40%. - Power supply
In order to ensure the good operation of the control system, computer system, and external networking, there are certain requirements for power supply, including power supply voltage change, frequency requirements, grounding device, shielding device, etc. - Compressed air
Some coordinate measuring machines require compressed air due to the use of precision air bearings. The purchaser of the coordinate measuring machine shall meet the requirements of the measuring machine for compressed air to prevent the impact of water and oil intrusion into the compressed air on the measuring machine, and prevent sudden air cut-off to avoid damage to the air bearing and guide rail of the measuring machine.