When it comes to CNC machining, precision isn’t just a goal—it’s a necessity. Whether you’re crafting components for aerospace, automotive, or consumer goods, the quality of each part can make or break the success of your project. But how do you ensure that every piece meets exact specifications? Enter quality assurance—a process that turns CNC machining into an art of consistency and reliability.
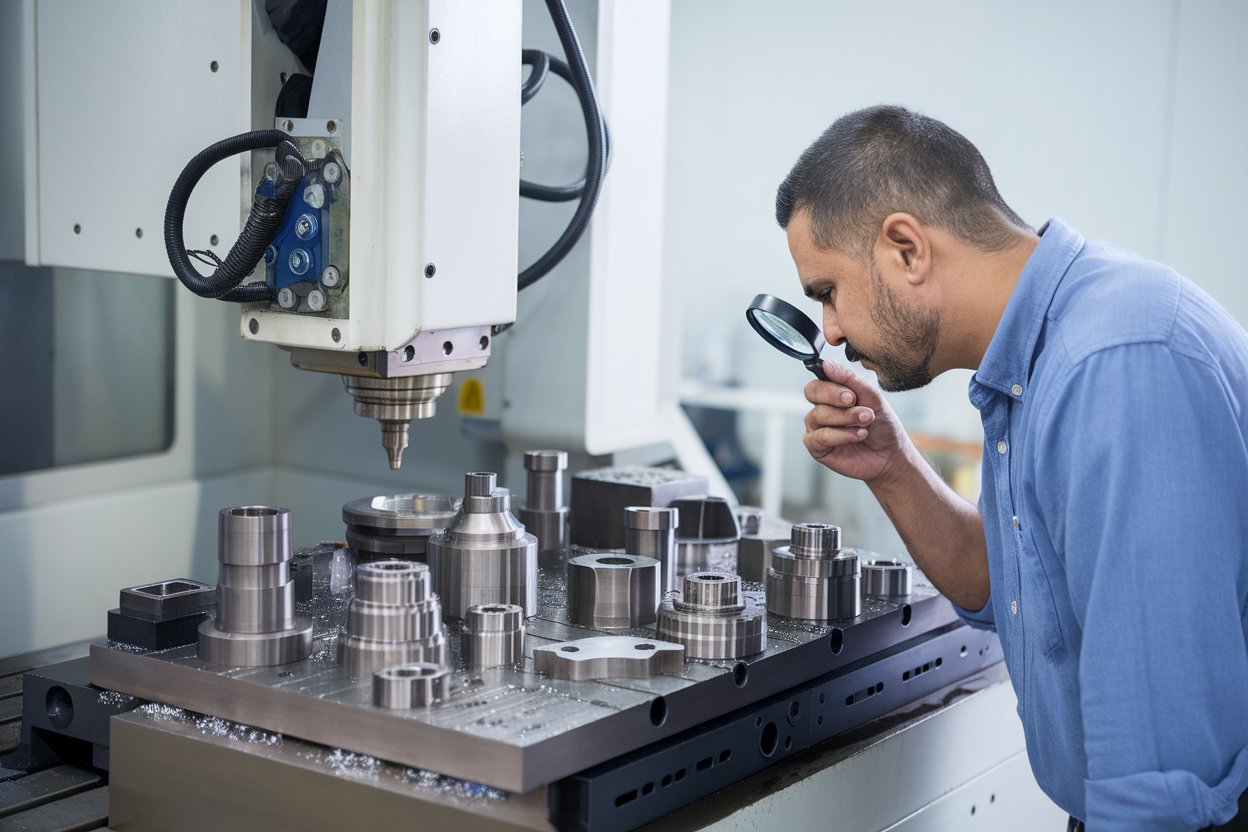
This article dives into why quality assurance is essential, the techniques that keep standards high, and how it transforms CNC machining into a trusted solution for any project.
Why Quality Assurance Matters
CNC machining is celebrated for its precision, but even the most advanced machines can’t guarantee perfection without rigorous quality checks. Why? Because the stakes are high:
1. Functionality
A slight deviation in a component’s dimensions can render it unusable. For industries like aerospace or healthcare, even a minor flaw can have catastrophic consequences.
2. Durability
Quality assurance ensures materials meet the required strength and resistance standards, preventing premature wear or failure in critical applications.
3. Cost Efficiency
Catching defects early saves time and money. It’s far cheaper to address issues during production than to recall defective parts later.
4. Customer Satisfaction
Consistent quality builds trust. Delivering flawless parts every time is a surefire way to retain clients and grow your reputation.
The Tools of the Trade: Quality Assurance Techniques
Quality assurance in CNC machining isn’t a one-size-fits-all process. It’s a blend of advanced tools, skilled technicians, and meticulous protocols.
1. Dimensional Inspection
– Tools like coordinate measuring machines (CMMs), laser scanners, and optical comparators ensure that parts match the 3D design down to microns.
– For simpler measurements, calipers and micrometers are used, but their precision shouldn’t be underestimated.
2. Surface Finish Testing
– A smooth surface isn’t just about aesthetics—it impacts performance, especially in moving parts. Surface roughness testers evaluate the texture to ensure it meets specifications.
3. Material Testing
– Techniques like hardness testing and tensile strength analysis verify that raw materials can withstand operational stresses.
– Non-destructive testing (NDT), such as ultrasonic or X-ray inspection, ensures internal integrity without damaging the part.
4. Functional Testing
– For complex components, quality assurance often includes functional tests to ensure they perform as intended under real-world conditions.
5. Statistical Process Control (SPC)
– By analyzing data from production runs, SPC identifies patterns and predicts potential issues, allowing for proactive adjustments.
Beyond the Numbers: Human Expertise in Quality Control
While machines and software play a big role, quality assurance also relies heavily on skilled professionals. Experienced inspectors and engineers bring:
– Attention to Detail: Machines are excellent, but a trained eye can catch subtle flaws that automated systems might miss.
– Problem-Solving Skills: When defects arise, it’s the human team that identifies root causes and implements solutions.
– Custom Solutions: Every project has unique requirements, and professionals tailor inspection protocols to meet specific challenges.
When Quality Meets Efficiency
A common misconception is that rigorous quality assurance slows down production. The truth? It does the opposite.
1. Streamlined Processes
By integrating quality checks at key stages of production, issues are identified and resolved early, preventing bottlenecks.
2. Reduced Waste
Accurate inspections minimize rejected parts, saving both materials and resources.
3. Faster Turnarounds
With fewer errors to fix post-production, projects are completed on time—or even ahead of schedule.
Industries That Demand Perfection
While quality assurance is essential for all CNC machining projects, certain industries set the bar even higher:
– Aerospace: Components must withstand extreme temperatures, pressures, and forces without failure.
– Medical Devices: Precision and sterility are critical for implants, surgical tools, and diagnostic equipment.
– Automotive: High-performance engines and safety systems demand flawless parts.
– Electronics: Miniature components require exact dimensions and reliable conductivity.
For these industries, quality assurance isn’t optional—it’s a regulatory requirement and a competitive edge.
Partnering for Success
When choosing a CNC machining partner, their approach to quality assurance should be a top consideration. Look for manufacturers that:
● Use advanced inspection equipment and techniques.
● Have certifications like ISO 9001 or AS9100, proving their commitment to quality standards.
● Offer transparency, sharing inspection reports and data.
● Emphasize continuous improvement, always looking for ways to refine processes.
The Key to Every Project’s Success
CNC machining is a marvel of modern manufacturing, but without quality assurance, its potential can’t be fully realized. By ensuring every part meets exacting standards, quality assurance transforms raw ideas into tangible success stories.
Whether you’re building the next breakthrough product or improving an existing design, investing in quality assurance isn’t just a step in the process—it’s the foundation for excellence.