How flat the surface of an object is is very important for manufacturing industrial products, especially ensuring quality of CNC machined parts. The tolerance range of irregularities is specified by the flatness and must be managed so that it is within the tolerance, but if it is not measured accurately and quantitatively, shape defects will be overlooked, it will be difficult to maintain quality, but it may also affect the next process or lead to a decrease in the yield rate.
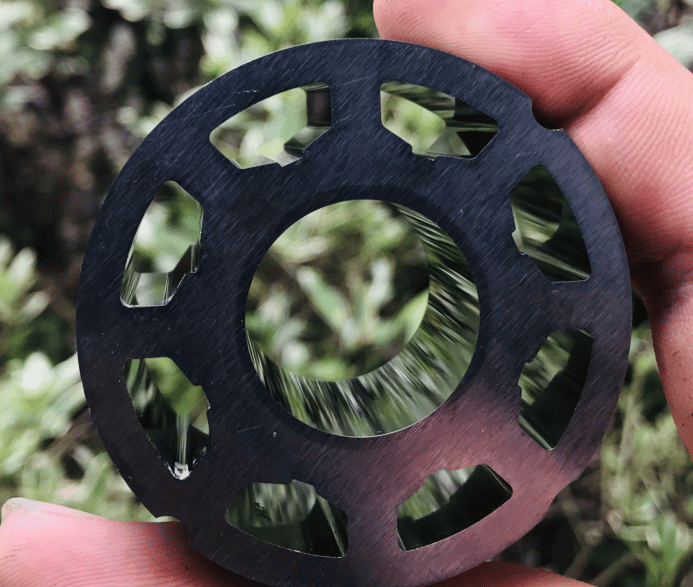
On this page, we will explain not only basic knowledge about flatness, common problems with conventional flatness, but also the latest measurement methods that can dramatically improve work efficiency and accuracy.
What is Flatness of CNC Machined Parts?
“Flatness” is a numerical value that indicates the smoothness (uniformity) of a plane. It requires that the flat part of the part fits between two parallel faces without sticking out. The definition in ISO is “the magnitude of deviation from a geometrically correct plane of a plane shape”.
CNC Parts Quality Inspection – Flatness Measurement Methods
・Maximum flatness
In the target plane, each plane passing through three points as far apart as possible is set, and the maximum value of their deviation is calculated as the flatness.
・Maximum inclined flatness
Calculate the value of the gap that can be formed when the target plane is sandwiched between parallel planes as the flatness.
When machining the surface of a part into a “tara”, flatness is used as an index to indicate how much precision is required for that surface.
・Are there any protruding protrusions? (Indicates uniformity of the machined surface itself)
・Is there warping? (Check whether the part after processing is deformed)
It is an index that is emphasized in the “cutting” and “polishing” processes, such as aluminum machined parts and stainless steel machined parts with flurry.
How To Measure Flatness of CNC Machined Parts?
There are two types of flatness measurement methods: contact type and non-contact type.
・ Contact type: Measurement by dial gauge, measurement by light wave interference pattern (Newton ring) using optical flat (flat gauge)
・ Non-contact type: Non-contact type measuring instruments are often used because the plane of the measurement target is not deformed by the combination of height information obtained by irradiating laser light.
Measurement With Dial Gauge (Contact Type)
Attach the dial gauge to the tip of the arm and contact the tip over the object to be measured. While tracing the surface to be measured so that the measurement point is uniform, the value of the dial gauge is read and the surface state (flatness) is measured.
Measurement Using Optical Flat (Contact Type)
An optical flat is a reference standard instrument made of transparent glass with a flat measuring surface. The flatness is measured based on the number of stripes (light wave interference frings: Newton rings) formed when this is brought into contact with the surface of the measurement target and irradiated with short-wavelength light.
Measurement Using Laser Light (Non-Contact Type)
A strip of laser light is irradiated on the measurement object, and the reflected light is imaged on a two-dimensional CMOS to measure the flatness. Also called a two-dimensional laser displacement sensor or a profile sensor, it can measure flatness without depending on the finishing state of the surface being measured. Since the measuring instrument and the measurement object do not come into direct contact, the measurement object will not be damaged.
Difference Between Flatness And Parallelism
The difference is that “one surface” is the measurement target for flatness and “two parts (parts)” are the measurement target for parallelism. Flatness and parallelism differ from the target location to be measured and the measurement method.
Flatness
A numerical value indicating the degree of flatness (uniformity) of a surface. This is a value to indicate how much gap is allowed when the surface of the measurement target is sandwiched between two parallel planes. For measuring flatness, dial gauges, optical flats, measuring instruments using laser light, etc. are used.
Parallelism
A number that indicates how parallel two or more planes or straight lines are. It is a value to indicate how close two parts (parts) that should be parallel can be brought to a parallel state. In measuring instruments such as outer micrometers and calipers, the degree of accuracy of the parallelism of the measuring surfaces has a significant impact on the measurement results.