Mistakes and failures are possible to happen in quality inspection. Let’s figure out the common inspection failures, as well as the causes and methods to solve them.
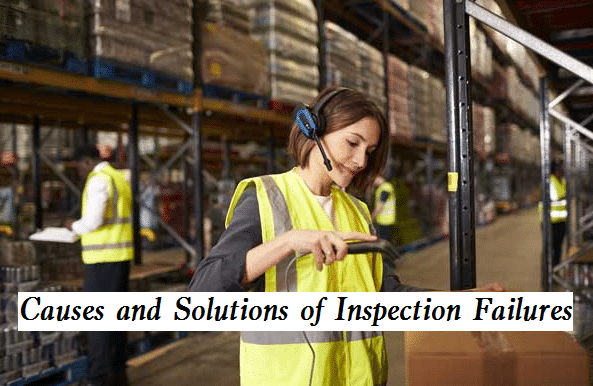
What are Common Inspection Failures
- Non-conformance to specifications or standards.
- Poor workmanship or manufacturing defects.
- Incorrect or incomplete documentation.
- Lack of control over raw materials or suppliers.
- Failure to follow established processes or procedures.
- Poorly maintained equipment or tools.
- Insufficient training of personnel.
- Failure to conduct inspections at appropriate stages of production.
- Inaccurate or inconsistent inspection results.
- Lack of clear criteria or accepted standards.
What are the Factors that Cause Inspection Mistakes
- Human error or bias
- Poorly defined inspection criteria or standards
- Insufficient training or experience of the inspector
- Time constraints or pressure to complete inspections quickly
- Poorly maintained or outdated equipment or tools
- Interruptions or distractions during the inspection process
- Lack of proper documentation or records
- Inadequate resources or funding for inspection activities
- Unclear communication or information transfer between inspector and stakeholders
- Fatigue or stress among inspectors.
What Steps to Take If Inspection Failures Happen
- Isolate the failed material to prevent its use in production.
- Conduct a root cause analysis to determine the reason for failure.
- Notify suppliers and request corrective action.
- Evaluate the impact on current and future production.
- Decide whether to reject, rework, or accept the material with concessions.
- Document the inspection results and actions taken.
- Implement preventative measures to avoid similar failures in the future.
- Communicate the results and actions taken to relevant departments and stakeholders.
- Update supplier performance records and reassess their suitability for future orders.
- Continuously monitor and improve the incoming inspection process to minimize the risk of future failures.
Should I Re-inspect If a Lot Fails in the QC Inspection?
It depends on the reason for the failure and the extent of the non-conformance. If the failure was due to a minor issue that can be easily corrected, then a re-inspection may be appropriate. However, if the failure was due to a major issue such as incorrect specification or poor workmanship, it may be necessary to reject the lot and conduct a root cause analysis to prevent similar failures in the future. It’s recommended to follow established quality control procedures and guidelines when deciding whether to re-inspect or take other corrective actions. It’s also important to document the inspection results, actions taken, and the rationale behind those actions.