There are several important factors to consider when choosing the best stylus for Coordinate Measuring Machines.
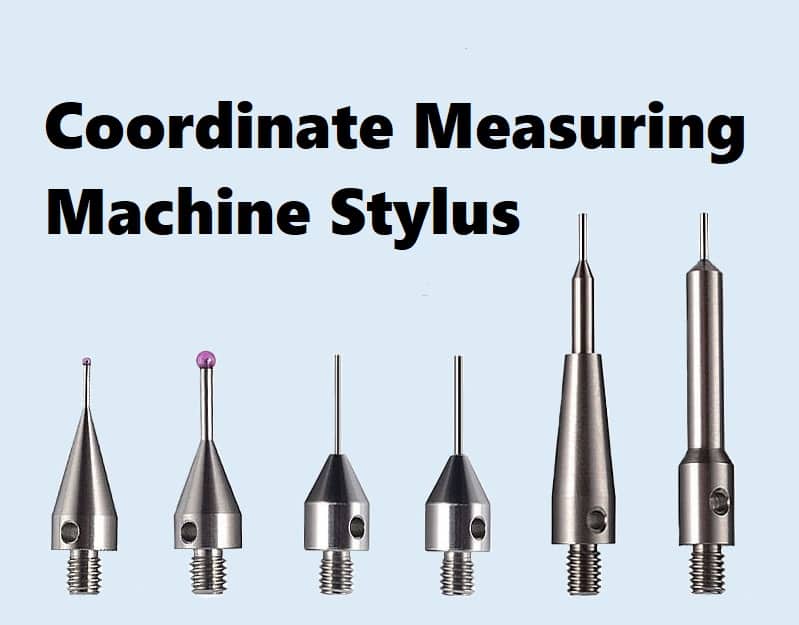
Precautions of Selecting Stylus for Coordinate Measuring Machine
When considering the accuracy required for CMM measurements, it is common to use a ratio of at least 1 to 5 CMM uncertainty to shape tolerance (1 to 10 is ideal, but many). In the case of, there is no compromise in terms of cost). This ratio provides a safety margin with relatively low uncertainty in the measurement results compared to the expected variability range of the measurement. If you can maintain this 1: 5 ratio with the tightest tolerances, then there is no problem with accuracy.
Unfortunately, as common as replacing the stylus attached to the probe, it can have a huge impact on the actual accuracy that can be achieved and can cause a great deal of variability in the measurement results. Just calibrating the CMM once a year to check accuracy only guarantees the measurement results with the stylus used for the calibration test (generally very short). Not enough. Also, the accuracy during this test is likely to be the highest. To get a more accurate picture of the accuracy of more measurements, you need to understand the impact of the stylus on measurement uncertainty.
In this post, we describe four main points to consider when selecting a stylus for Coordinate Measuring Machine, which affect the accuracy of the entire CMM.
- 1. Stylus sphere sphericity (roundness)
- 2. Stylus deflection
- 3. Thermal stability
- 4. Selection of stylus ball material (during scanning)
1. CMM Stylus Sphere Sphericity (Roundness)
The tip of the stylus used for measurement is often spherical and is typically made of artificial ruby. Deviations in the sphericity (roundness) of this tip contribute to the measurement uncertainty of the CMM, which can easily reduce the accuracy of the CMM by 10%.
Ruby spheres are manufactured to the accuracy level defined by the “grade” associated with the maximum deviation of the sphere from the true sphere. Commonly used sphere specifications include grade 5 and grade 10 (the smaller the grade number, the higher the accuracy). Downgrading from Grade 5 to Grade 10 will reduce the cost of the stylus alone, but at the risk of a 1: 5 ratio.
The grade of the sphere cannot be visually determined and does not appear clearly in the measurement results. Therefore, it is difficult to determine whether the grade of the ball is important. Using a grade 5 sphere as standard is one solution, but at a slightly higher cost. However, the costs that go up here are not as serious as the cost of scrapping good products and, worse, the cost of passing non-conforming products. In addition, as the accuracy of the CMM increases, the effect of changes in the grade of the sphere will increase. On top-of-the-line CMMs, these reduce accuracy by nearly 10%.
An example is given below:
Typical probe measurement error according to ISO 10360-2 (MPEP) (calculated using a stylus with a grade 5 sphere)
MPEP = 1.70µm
It is a value calculated by measuring 25 discrete points, each evaluated as 25 separated radii. The range of radius variation is the MPEP value. The roundness of the stylus sphere is directly related to this value. Therefore, switching from a grade 5 sphere to a grade 10 sphere increases this value by 0.12 µm, which in this example increases the probe measurement error by 7%.
MPEP = 1.82µm
The roundness of the stylus sphere also affects MPETHP. MPETHP uses four scanning paths on the sphere to evaluate the performance of the scanning probe.
Gravity 5 sphere sphericity = 0.13µm
Gravity 10 sphere sphericity = 0.25µm
For the most demanding requirements, we offer a variety of Grade 3 spheres with a sphericity of 0.08 µm.
2. CMM Stylus Deflection
When using a touch-trigger probe such as the industry standard TP20, you typically replace the stylus module to apply the best stylus for each measurement task. We do not use one long stylus for all shapes, as the longer the stylus, the less accurate it is. The stylus should be as short and stiff as possible. Why is that?
This loss of accuracy is not directly caused by the stylus, but is exacerbated by the length of the stylus. This error is due to the different forces that trigger the probe in each direction. The probe usually does not trigger at the moment of contact between the stylus and the object to be measured. A force that exceeds the spring load in the sensor mechanism must be applied. The stylus undergoes elastic deformation due to this force. This deformation causes the probe to move slightly relative to the object to be measured between physical contact and the output of the trigger. This slight movement is known as pre-travel.
With the triangular three-point support arrangement used in many probes, the force required to trigger is not constant. In the stiff direction, the probe will not trigger until the stylus flexes more. It also means that the CMM moves more significantly, so the pre-travel amount also changes depending on the approach angle (see the figure on the right). Pretravel variability becomes even more complex when it comes to complex approach angles (X, Y and Z axes).
To minimize this effect, calibrate all styli on a well-dimensional reference sphere before use. Ideally, this calibration should map the error in all combinations of stylus and approach angle. However, in reality, a typical angle is often selected and averaged to save time, so a slight error remains.
To what extent this remaining error affects measurement uncertainty is difficult to determine without empirical testing. It should be noted that the error due to the remaining pretravel variability is increased by the stiffness of the selected stylus. In other words, the material selection is very important when designing the stylus, and it is necessary to weigh the bending rigidity of the shaft with other characteristics such as weight and cost. Steel with Young’s modulus E = 210kN / mm2 is suitable for many short styli, while the most widely used rigid material is carbide (E = 620kN / mm2). However, due to the high density of carbide, it is rarely used in long styli. For long styluses, carbon fiber excels in both rigidity (E ≥ 450kN / mm2) and light weight. On the other hand, ceramics (E = 300-400kN / mm2) are also often used in machine tool applications where light weight and heat stability are required.
The stiffness of the stylus is also affected by the stylus assembly joints. As a general rule, no coupling is provided because hysteresis occurs, but this principle may not be adhered to when measuring with a fixed sensor for complicated parts. In such cases, a configuration consisting of various styli, extensions, connectors, and knuckles is required. Again, it is important to consider each material when selecting each component, as it affects rigidity, weight, and robustness.
3. Thermal Stability of CMM Stylus
Temperature fluctuations can cause serious measurement errors. Choosing the right material extension for your stylus will give you better stability in changing environments, leading to more consistent measurement results. Since thermal expansion depends on length, a material with a low coefficient of thermal expansion is required, especially when using a long stylus.
As already mentioned above, carbon fiber is most widely used for long styluses and extensions because of its rigidity, light weight, and its length does not change over temperature. When metal is required for joints and knuckles, titanium is the best choice for strength, stability and density. At Renishaw, both probe and stylus extensions are lined up in these materials.
4. Selection of CMM Stylus Ball Material
Often, the ruby ball is chosen as the tip of the stylus. However, other materials may be more suitable.
In touch measurements, the tip of the stylus is in contact with the surface for only a short time, so there is no relative motion. Scanning measurements differ because the sphere slides on the surface of the object, resulting in frictional wear. In extreme cases, this extended contact time can affect the sphericity by removing the material of the stylus sphere or depositing other materials on the sphere. This effect is noticeable when a specific part of the sphere is in constant contact with the object to be measured. We have conducted extensive research on this effect and focused on two types of wear mechanisms.
Abrasion
Abrasive wear wear occurs when scanning surfaces such as cast iron. The remaining fine particles cause fine scratches on the stylus and work, creating a small flat surface at the tip of the stylus. In such cases, a sturdy zirconia ball is the best choice.
Adhesive wear
Adhesive wear test 2 Adhesive wear occurs when the stylus sphere and the material of the object have a chemical affinity for each other. It can be seen when scanning aluminum objects with ruby (aluminum oxide) spheres. The material is transferred from the relatively soft object to the stylus sphere, forming an aluminum film on the sphere. This also affects the roundness. In such cases, silicon nitride is the best choice. Silicon nitride has high wear resistance and does not attract aluminum.
5. Other Elements of CMM Stylus
Other considerations when selecting a stylus include:
- Stylus screw diameter that matches the sensor used
- Stylus type such as straight, star, swivel, custom etc.
- A type of stylus tip such as a sphere, cylinder, disc, or hemisphere.
- The size of the tip of the stylus. To minimize the effect of surface roughness on measurement accuracy.
Summarize
The CMM stylus is an integral part of any measurement and plays a vital role between the sensor and the object to be measured. For example, you will have access to the shape around the part. The stylus must also accurately convey the surface position to the probe. To facilitate high-precision measurements, the stylus must be constructed from precision parts made of materials that meet the measurement requirements. With the right stylus carefully selected, uncertainty is not significantly increased and consistent and reliable results are obtained. If part tolerances are tight or long styluses are required, the impact of these choices on accuracy should be carefully considered.