The dimensional inspection of components plays a critical role in ensuring the quality and performance of mechanical assemblies. In the case of a rocker arm assembly, a key component that requires precise measurement is the bearing. Accurate dimensional inspection of the bearing in a rocker arm is crucial to verify its compliance with specifications, assess its performance characteristics, and ensure optimal functionality. In this comprehensive article, we will explore various techniques and best practices for accomplishing the dimensional inspection of a bearing in a rocker arm assembly, incorporating the most popular views on the subject.
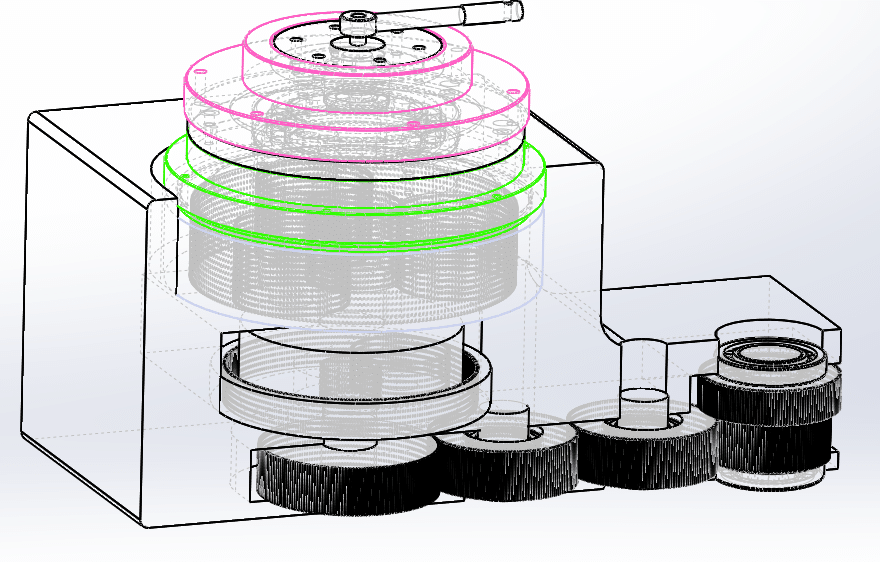
Importance of Dimensional Inspection in Rocker Arm Assemblies:
The dimensional inspection of bearings in rocker arm assemblies serves multiple purposes, including:
Quality Assurance: By conducting dimensional inspections, manufacturers can verify that bearings meet the required specifications, tolerances, and fitment standards. This ensures the overall quality and reliability of the rocker arm assembly.
Performance Assessment: Dimensional inspections enable the evaluation of critical parameters such as inner and outer diameters, thickness, and clearance. This assessment aids in determining the bearing’s load-carrying capacity, friction characteristics, and overall performance within the rocker arm assembly.
Durability and Service Life: Accurate dimensional inspection helps ensure that the bearing’s design and material characteristics are suitable for the expected service conditions. It helps identify any dimensional deviations or anomalies that may affect the bearing’s durability and service life.
Dimensional Inspection Methods & Tools
Several popular views exist regarding the most effective techniques for accomplishing dimensional inspections of bearings in rocker arm assemblies:
Traditional Measurement Tools: Traditional measurement tools, such as calipers, micrometers, and dial indicators, are widely employed for dimensional inspections. These tools provide accurate measurements of critical dimensions such as inner and outer diameters, width, and thickness. They are cost-effective and offer high precision for small-scale dimensional inspections.
Coordinate Measuring Machines (CMM): CMMs are sophisticated measurement systems that utilize probes and computer-controlled movements to capture precise 3D measurements. CMMs are capable of inspecting complex geometries and can generate detailed reports with graphical representations. They offer superior accuracy and repeatability, making them suitable for comprehensive dimensional inspections of rocker arm bearings.
Optical Measurement Systems: Optical measurement systems, including vision-based systems and non-contact laser scanners, are gaining popularity for dimensional inspections. These systems capture high-resolution images or 3D point cloud data, enabling accurate measurement of bearing dimensions. Optical measurement systems are non-destructive, fast, and can handle both large-scale and small-scale inspections.
X-ray and CT Scanning: X-ray and CT scanning techniques provide valuable insights into the internal structure and dimensional integrity of bearings. These techniques are particularly useful for non-destructive inspection of complex bearing designs and detecting internal defects, such as cracks or voids. X-ray and CT scanning enable precise measurement of internal dimensions and can aid in quality control and failure analysis.
How Can The Dimensional Inspection Of A Bearing In A Rocker Arm Be Accomplished?
To ensure accurate and reliable dimensional inspections of bearings in rocker arm assemblies, consider the following best practices:
1. Establish Measurement Plan: Develop a comprehensive measurement plan that outlines the critical dimensions to be inspected, the appropriate measurement techniques, and the acceptance criteria. This plan should consider industry standards, customer requirements, and the specific design and function of the rocker arm bearing.
2. Select Suitable Measurement Tools: Choose the appropriate measurement tools based on the required accuracy, complexity of the bearing design, and available resources. Consider factors such as precision, ease of use, and compatibility with the bearing’s material and geometry.
3. Calibration and Verification: Regularly calibrate and verify the measurement tools to ensure their accuracy and reliability. Adhere to established calibration standards and protocols to maintain traceability and consistency in the measurement process.
4. Sampling and Statistical Analysis: Determine the appropriate sampling strategy for dimensional inspections. Conduct statistical analysis, such as process capability studies, to evaluate the measurement data, identify any trends or variations, and ensure compliance with specifications.
5. Documentation and Reporting: Thoroughly document the dimensional inspection process, including measurement results, procedures, and any deviations or non-conformities identified. Generate detailed reports that provide a clear overview of the dimensional characteristics of the rocker arm bearing and any findings during the inspection.
6. Compliance with Industry Standards:
7. Ensure that the dimensional inspection of rocker arm bearings aligns with relevant industry standards and guidelines. Industry-specific standards, such as those from the International Organization for Standardization (ISO) or the American Society of Mechanical Engineers (ASME), provide valuable guidance on measurement techniques, tolerances, and acceptance criteria.
Accurate dimensional inspection of bearings in rocker arm assemblies is vital for ensuring product quality, performance, and durability. By employing appropriate measurement techniques, adhering to best practices, and considering popular views on dimensional inspection, manufacturers can effectively assess the critical dimensions of rocker arm bearings. This enables the identification of deviations, assurance of compliance with specifications, and optimization of the rocker arm assembly’s functionality.