As an important transportation mode to solve the problem of traffic congestion in densely populated cities, rail transit has been added and expanded more and more with the continuous expansion of urban scale. This kind of transportation mode with large traffic volume and in non ground space has higher requirements for its operation scheduling and safety performance. In this paper, we share a case about the engineering application of 3D laser scanning in rail transit stations.
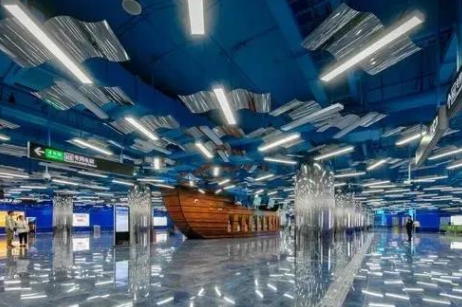
Project Case
In recent years, with the rapid development of 3D laser scanning technology, it provides a good technical way for measurement and data acquisition. The significance of three-dimensional scanning is that it can convert the three-dimensional information of the physical object into the digital information that can be processed directly by the computer, and provide a convenient and fast means for the digitization of the physical object.
In this case, the monitors conduct three-dimensional scanning and mapping of the whole station after the completion of metro civil construction, which is subsequently used to compare with the initial design data to analyze the construction quality of civil engineering, form the final results, and provide accurate data for comprehensive analysis and utilization for subsequent equipment installation, decoration and other projects.
The traditional subway engineering surveying and mapping usually uses the total station to collect the coordinates of discrete points on site, and makes maps with the help of operation sketches and on-site photos. The inconvenience is that it is easy to be affected by the parallel construction of other processes during work, and sometimes it is difficult to meet the intervisibility conditions. In addition, the surveying and mapping period is tight, the task is heavy, and the on-site surveying and mapping conditions are complex, Therefore, the disadvantages of large field workload, low degree of automation and measurement efficiency, limited information acquisition and partial and one-sided measurement results bring great difficulties to field work.
The use of 3D laser scanner in the surveying and mapping of subway stations has the characteristics of non-contact measurement, high resolution, high precision, high efficiency, digital acquisition and rich information. It can quickly and comprehensively obtain the point cloud data of subway stations and sections. After preprocessing such as point cloud data splicing, denoising and slicing, more comprehensive, rich and vivid measurement results can be generated, Recheck the construction quality of the station. In addition, the BIM model of the station can be inversely established according to the point cloud to restore the real size and clearance of various structures of the station, which provides basic data for subsequent large-scale equipment installation simulation, pipeline space review or adjustment of decoration scheme.
Application Of 3D Scanning In Rail Transit Stations
Compared with traditional measurement, the point cloud data obtained by 3D scanning measurement is more comprehensive, which can be measured and used multiple times at one time. It can obtain the structural deviation, hole deviation, clearance and other information of the station based on point cloud calculation at the same time, provide more comprehensive and intuitive measurement results, and establish a permanent 3D data file of the station. It can also improve the correctness of the original station BIM model according to the point cloud data, and provide a complete and accurate data basis for the later equipment installation, decoration, operation and maintenance and information management of the station. We generally make a simple and incomplete exposition on the applicable direction.
1. Improve the correctness of the original BIM model
Each participant of the project will establish a BIM model at each stage of project implementation, so as to realize the exchange of project information among all participants. However, due to errors in construction, the BIM model established in the design and construction stage is often inconsistent with the actual situation of the final completion site. This inconsistency may bring difficulties to the later stages of the project, such as decoration, operation and maintenance. Through the point cloud model obtained after three-dimensional scanning, we can effectively obtain the real and effective size information of the project site, so as to realize the connection between the model and the current situation of the project.
Verify the consistency between the BIM model and the on-site construction structure, and then modify the BIM model through model comparison, so as to improve the accuracy and reduce the errors caused by the model not in line with the engineering practice, so as to better ensure the quality of urban rail transit engineering construction.
2. Test and analyze the completed projects
2.1 dimensional analysis
For example, for the flatness analysis of the site, we analyze the flatness of the point cloud model through the software, which can intuitively display the flatness of each part in the way of color scale, view the flatness of the wall, and generate a test report. Through flatness analysis, the flatness of subway station wall, column, roof and ground is summarized, the quality is controlled, and the specific quality problems are repaired.
Another example is clearance analysis. We intercept the point cloud data of the plane by plane interception on each floor and compare it with the design data, or intercept the facade point cloud data at the characteristic position of the station and compare it with the design data to analyze the elevation of roof and floor markers.
2.2 deviation analysis
For example, in the structural deviation analysis of subway station, the three-dimensional scanning data can visually display the three-dimensional deviation between the actual structure of the station and the design model, calculate the change of point cloud from BIM model, and visually display the deviation results with color chromatogram.
In addition, it can also be applied to the hole deviation analysis of subway stations, such as the size and position deviation of reserved holes such as stair holes, escalator holes and water supply and drainage, so as to provide data guidance for later equipment and pipeline installation.
3. Provide basic data for subsequent decoration
In the construction of subway station, the error between the actual structure and the original design has a significant negative impact on the subsequent decoration stage and equipment installation stage.
We use the three-dimensional point cloud scanning technology to obtain the digital model of the construction structure, analyze and compare the point cloud model and the BIM model, so as to easily find and correct the parts in the BIM model that do not meet the actual site, ensure the correctness of the model, provide an accurate digital basic model for the subsequent decoration and equipment safety work, and improve the construction efficiency, Increase economic benefits.
4. Generate section view and section view
In the generated three-dimensional model, the section view and section view of any part can be obtained by cutting. The analysis of the section and section can facilitate the relevant staff to verify the structural dimensions and issue the corresponding as built drawings.