In the fast-evolving world of precision manufacturing, the quality of individual components plays a decisive role in product reliability, safety, and performance. Whether it’s for aerospace, medical, or automotive industries, precision parts inspection is at the heart of ensuring that manufactured components meet the highest standards. This blog outlines critical best practices in parts inspection, essential tools, and expert insights to help manufacturers achieve excellence in quality assurance.
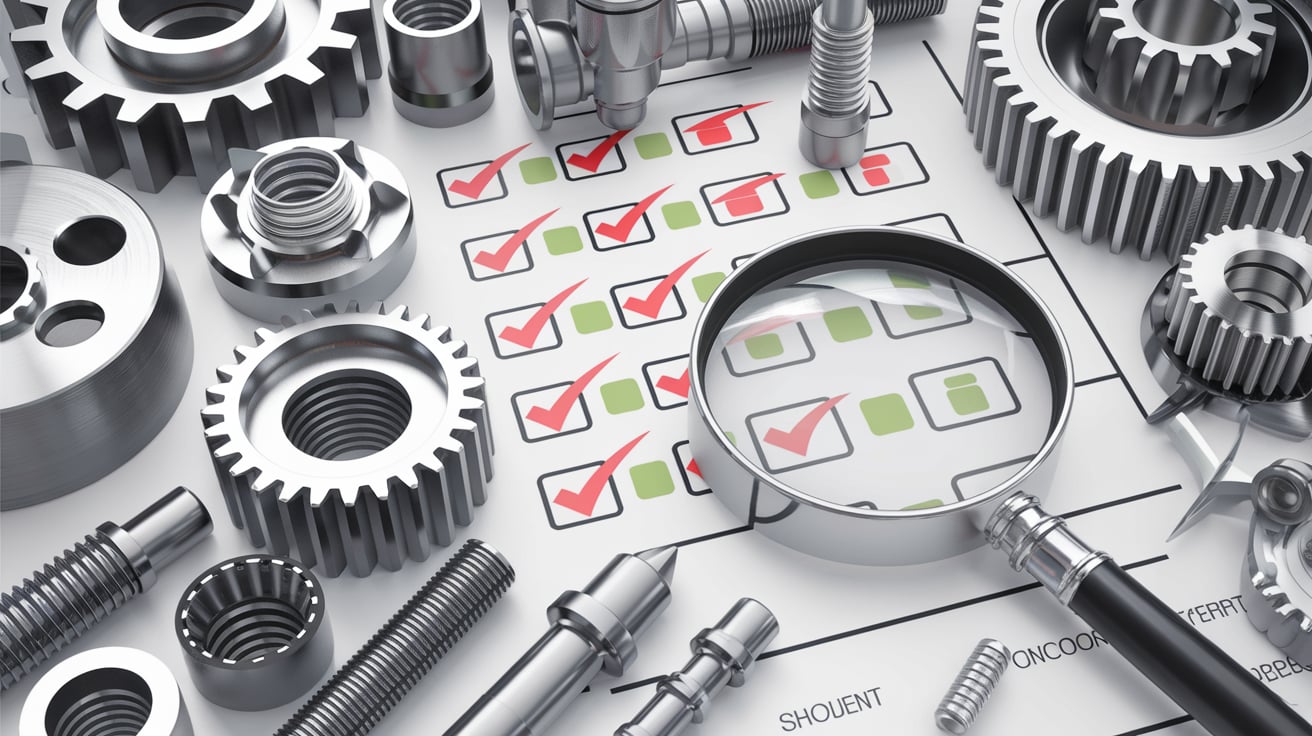
1. The Role of Precision Inspection in Manufacturing
Precision parts inspection is not just a step in the manufacturing process; it’s a cornerstone of quality management. It ensures that:
· Tolerances are Met: Critical dimensions conform to design specifications.
· Defects are Identified Early: Issues such as surface irregularities, material inconsistencies, or internal flaws are detected before assembly or delivery.
· Compliance is Guaranteed: Adherence to industry and customer-specific standards is maintained.
· Costs are Controlled: Early defect detection reduces rework, material waste, and potential warranty claims.
2. Critical Best Practices in Precision Inspection
A. Define Inspection Standards Early
Establish clear inspection criteria during the design phase. Collaborate with engineers to identify critical dimensions, tolerances, and acceptable defect thresholds. Early planning ensures smoother production and fewer surprises during inspection.
B. Tailor Inspection Methods to Material and Function
Different parts demand different inspection methods. For instance:
· Metal Components: Use techniques like Coordinate Measuring Machines (CMM) for dimensional accuracy and ultrasonic testing for subsurface flaws.
· Plastic Parts: Focus on surface inspection using optical systems to detect warping, shrinkage, or material inconsistencies.
· Composite Materials: Leverage advanced tools like X-ray or CT scanning for internal defect detection.
C. Leverage Statistical Process Control (SPC)
SPC uses data-driven insights to monitor and control production quality. By analyzing trends in measurement data, manufacturers can identify deviations and implement corrective actions before defects arise.
D. Implement 100% Inspection for High-Criticality Parts
For safety-critical components, such as those in medical or aerospace applications, 100% inspection ensures zero-defect delivery. Automation and machine vision systems make this feasible without compromising efficiency.
3. Essential Tools for Precision Parts Inspection
The right tools are vital for effective quality control. Here’s an overview of the most widely used inspection technologies:
1. Coordinate Measuring Machines (CMM)
CMMs use touch probes or laser scanners to measure the dimensions of a part against a 3D CAD model. Ideal for complex geometries, they provide micron-level accuracy.
· Advantages: High precision, excellent for intricate designs.
· Use Case: Verifying tolerances on turbine blades, gears, or other machined components.
2. Optical Inspection Systems
These systems employ high-resolution cameras or laser-based technology to inspect surface features.
· Advantages: Non-contact inspection, rapid data capture.
· Use Case: Evaluating surface finishes, identifying scratches, or assessing part geometry in high-volume production.
3. X-Ray and CT Scanning
X-ray and CT imaging are indispensable for non-destructive testing (NDT) of internal structures.
· Advantages: Detects internal voids, cracks, or material inconsistencies.
· Use Case: Inspection of cast or molded parts, composite materials, or additive-manufactured components.
4. Surface Roughness Testers
Surface finish is critical in parts like seals, bearings, and gears. Roughness testers quantify the surface profile to ensure functional and aesthetic requirements are met.
· Advantages: Accurate measurement of surface texture.
· Use Case: Ensuring smooth finishes on friction-sensitive components.
5. Laser Scanners
Laser scanning enables 3D surface mapping for both dimensional accuracy and visual inspection.
· Advantages: Fast and versatile, suitable for capturing complex freeform surfaces.
· Use Case: Reverse engineering, inspecting plastic molds, or verifying weld seams.
4. Trends Shaping Modern Parts Inspection
As manufacturing technology advances, so do the methods of ensuring quality. The following trends are transforming parts inspection:
A. Automation in Inspection
Automated inspection systems integrated with production lines are becoming standard. They enable real-time quality checks, reduce human error, and improve inspection throughput.
B. AI and Machine Learning
Artificial intelligence is revolutionizing defect detection. Machine learning algorithms can analyze inspection data, recognize patterns, and predict potential quality issues, offering manufacturers a proactive approach to quality control.
C. Digital Twins
Digital twins replicate physical parts in a virtual environment, allowing manufacturers to compare real-world inspection data with simulated expectations. This enhances precision and predictive maintenance capabilities.
D. Portable Inspection Devices
Handheld inspection tools bring quality control closer to the production floor. These tools are lightweight, easy to operate, and ideal for on-site checks in industries like construction or large-scale manufacturing.
E. Integration of IoT and QC Systems
The Internet of Things (IoT) connects inspection equipment with centralized systems, offering real-time data monitoring, reporting, and analytics. This integration boosts transparency and traceability in the QC process.
5. Overcoming Challenges in Parts Inspection
While advanced tools and methods have improved inspection capabilities, challenges remain:
· Balancing Speed and Accuracy: In high-volume production, achieving both can be difficult. Automated inspection and hybrid systems help bridge this gap.
· Interpreting Big Data: Modern inspection generates massive datasets. Manufacturers need robust software solutions to analyze and apply insights effectively.
· Ensuring Operator Expertise: Sophisticated tools require skilled technicians. Ongoing training and certification programs are essential.
Precision parts inspection is the foundation of high-quality manufacturing. By implementing best practices, leveraging advanced tools, and staying ahead of industry trends, manufacturers can ensure product excellence and customer satisfaction. Investing in a robust inspection process not only enhances reliability but also builds a reputation for precision and trustworthiness in a competitive market.
Ensuring Quality Excellence in Precision Parts Inspection: Best Practices and Key Insights
In the fast-evolving world of precision manufacturing, the quality of individual components plays a decisive role in product reliability, safety, and performance. Whether it’s for aerospace, medical, or automotive industries, precision parts inspection is at the heart of ensuring that manufactured components meet the highest standards. This blog outlines critical best practices in parts inspection, essential tools, and expert insights to help manufacturers achieve excellence in quality assurance.
1. The Role of Precision Inspection in Manufacturing
Precision parts inspection is not just a step in the manufacturing process; it’s a cornerstone of quality management. It ensures that:
· Tolerances are Met: Critical dimensions conform to design specifications.
· Defects are Identified Early: Issues such as surface irregularities, material inconsistencies, or internal flaws are detected before assembly or delivery.
· Compliance is Guaranteed: Adherence to industry and customer-specific standards is maintained.
· Costs are Controlled: Early defect detection reduces rework, material waste, and potential warranty claims.
2. Critical Best Practices in Precision Inspection
A. Define Inspection Standards Early
Establish clear inspection criteria during the design phase. Collaborate with engineers to identify critical dimensions, tolerances, and acceptable defect thresholds. Early planning ensures smoother production and fewer surprises during inspection.
B. Tailor Inspection Methods to Material and Function
Different parts demand different inspection methods. For instance:
· Metal Components: Use techniques like Coordinate Measuring Machines (CMM) for dimensional accuracy and ultrasonic testing for subsurface flaws.
· Plastic Parts: Focus on surface inspection using optical systems to detect warping, shrinkage, or material inconsistencies.
· Composite Materials: Leverage advanced tools like X-ray or CT scanning for internal defect detection.
C. Leverage Statistical Process Control (SPC)
SPC uses data-driven insights to monitor and control production quality. By analyzing trends in measurement data, manufacturers can identify deviations and implement corrective actions before defects arise.
D. Implement 100% Inspection for High-Criticality Parts
For safety-critical components, such as those in medical or aerospace applications, 100% inspection ensures zero-defect delivery. Automation and machine vision systems make this feasible without compromising efficiency.
3. Essential Tools for Precision Parts Inspection
The right tools are vital for effective quality control. Here’s an overview of the most widely used inspection technologies:
1. Coordinate Measuring Machines (CMM)
CMMs use touch probes or laser scanners to measure the dimensions of a part against a 3D CAD model. Ideal for complex geometries, they provide micron-level accuracy.
· Advantages: High precision, excellent for intricate designs.
· Use Case: Verifying tolerances on turbine blades, gears, or other machined components.
2. Optical Inspection Systems
These systems employ high-resolution cameras or laser-based technology to inspect surface features.
· Advantages: Non-contact inspection, rapid data capture.
· Use Case: Evaluating surface finishes, identifying scratches, or assessing part geometry in high-volume production.
3. X-Ray and CT Scanning
X-ray and CT imaging are indispensable for non-destructive testing (NDT) of internal structures.
· Advantages: Detects internal voids, cracks, or material inconsistencies.
· Use Case: Inspection of cast or molded parts, composite materials, or additive-manufactured components.
4. Surface Roughness Testers
Surface finish is critical in parts like seals, bearings, and gears. Roughness testers quantify the surface profile to ensure functional and aesthetic requirements are met.
· Advantages: Accurate measurement of surface texture.
· Use Case: Ensuring smooth finishes on friction-sensitive components.
5. Laser Scanners
Laser scanning enables 3D surface mapping for both dimensional accuracy and visual inspection.
· Advantages: Fast and versatile, suitable for capturing complex freeform surfaces.
· Use Case: Reverse engineering, inspecting plastic molds, or verifying weld seams.
4. Trends Shaping Modern Parts Inspection
As manufacturing technology advances, so do the methods of ensuring quality. The following trends are transforming parts inspection:
A. Automation in Inspection
Automated inspection systems integrated with production lines are becoming standard. They enable real-time quality checks, reduce human error, and improve inspection throughput.
B. AI and Machine Learning
Artificial intelligence is revolutionizing defect detection. Machine learning algorithms can analyze inspection data, recognize patterns, and predict potential quality issues, offering manufacturers a proactive approach to quality control.
C. Digital Twins
Digital twins replicate physical parts in a virtual environment, allowing manufacturers to compare real-world inspection data with simulated expectations. This enhances precision and predictive maintenance capabilities.
D. Portable Inspection Devices
Handheld inspection tools bring quality control closer to the production floor. These tools are lightweight, easy to operate, and ideal for on-site checks in industries like construction or large-scale manufacturing.
E. Integration of IoT and QC Systems
The Internet of Things (IoT) connects inspection equipment with centralized systems, offering real-time data monitoring, reporting, and analytics. This integration boosts transparency and traceability in the QC process.
5. Overcoming Challenges in Parts Inspection
While advanced tools and methods have improved inspection capabilities, challenges remain:
· Balancing Speed and Accuracy: In high-volume production, achieving both can be difficult. Automated inspection and hybrid systems help bridge this gap.
· Interpreting Big Data: Modern inspection generates massive datasets. Manufacturers need robust software solutions to analyze and apply insights effectively.
· Ensuring Operator Expertise: Sophisticated tools require skilled technicians. Ongoing training and certification programs are essential.
Precision parts inspection is the foundation of high-quality manufacturing. By implementing best practices, leveraging advanced tools, and staying ahead of industry trends, manufacturers can ensure product excellence and customer satisfaction. Investing in a robust inspection process not only enhances reliability but also builds a reputation for precision and trustworthiness in a competitive market.