In this article, we’ll go over some details about factory audits, including the process, types, and checklist.
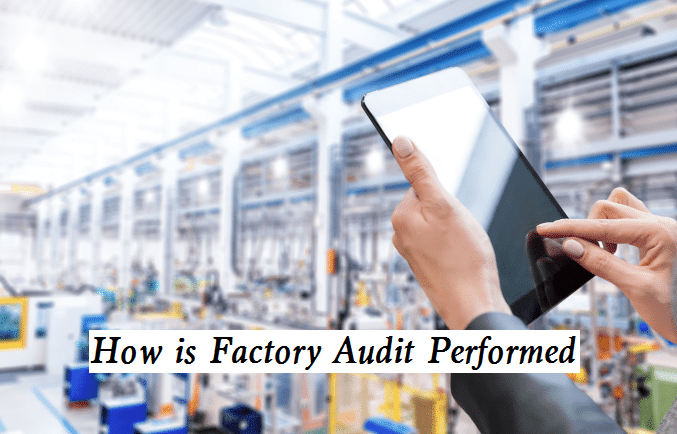
What is the Process of a Factory Audit?
A factory audit is an assessment of a manufacturing facility’s quality management system, processes, and procedures to ensure compliance with industry standards, regulations, and best practices. The process of a factory audit typically includes the following steps:
1) Planning: The auditor and factory management agree on the audit scope, timeline, and objectives. The auditor may request documents and information prior to the audit to prepare for the assessment.
2) Pre-audit: The auditor conducts a preliminary review of the factory’s quality management system and documentation to identify potential compliance issues and areas of concern.
3) On-site audit: The auditor visits the factory to conduct a comprehensive assessment of the facility’s processes, procedures, and systems. The audit typically includes a review of documents, interviews with personnel, and observation of manufacturing processes.
4) Findings and recommendations: The auditor provides a report that identifies compliance issues and non-conformities, as well as recommendations for improvement. The report may also include corrective actions that the factory must take to address identified issues.
5) Follow-up: The auditor may conduct follow-up audits to ensure that the factory has implemented corrective actions and is in compliance with industry standards and regulations.
6) Overall, the process of a factory audit aims to assess the factory’s ability to produce quality products, maintain safe and healthy working conditions, and comply with applicable laws and regulations.
Different Types of Factory Audit
There are several different types of factory audits, each with its specific focus and objectives. Some common types of factory audits include:
- Quality System Audit: This type of audit evaluates a factory’s quality management system (QMS) to ensure that it meets industry standards and regulatory requirements. The audit may assess the factory’s policies, procedures, and documentation related to quality control, product testing, and customer complaints management.
- Environmental Audit: An environmental audit evaluates a factory’s compliance with environmental regulations and assesses its environmental management system. The audit may evaluate the factory’s waste management practices, water and air quality, energy usage, and pollution prevention measures.
- Social Compliance Audit: A social compliance audit assesses a factory’s compliance with labor and human rights standards. The audit may evaluate the factory’s policies and practices related to fair wages, working hours, workplace safety, and workers’ rights.
- Security Audit: A security audit evaluates a factory’s security measures to protect its employees, facilities, and assets from theft, vandalism, or other security threats. The audit may assess the factory’s access control measures, CCTV systems, and emergency response procedures.
- Supply Chain Audit: A supply chain audit assesses a factory’s suppliers’ compliance with industry standards and regulatory requirements. The audit may evaluate the supplier’s environmental and social compliance, quality management systems, and product safety.
Factory Audit Checklist
A factory audit checklist can be quite extensive and may vary depending on the type of audit and the industry the factory operates. However, here is a general checklist that covers some common items that may be included:
1) General Information
Factory name and location
Date and time of the audit
Contact person and their contact details
Type of audit
2) Quality Management System (QMS)
Quality policy and objectives
Quality manual and procedures
Document control system
Record-keeping and documentation practices
Internal audit and corrective/preventive action process
Training and competency of employees
3) Manufacturing Processes
Production planning and scheduling
Raw material and finished product inventory management
Production line and process controls
Equipment maintenance and calibration
Non-conforming product handling and disposition
Product testing and inspection
4) Product Quality
Product specifications and standards
Product testing procedures and equipment
Traceability and identification practices
Packaging and labeling practices
Customer complaint handling process
5) Environmental Management
Environmental policy and objectives
Environmental management system
Air and water quality management
Waste management practices
Energy conservation measures
6) Occupational Health and Safety
Occupational health and safety policy and objectives
Risk assessment and hazard identification process
Safety equipment and PPE usage
Emergency preparedness and response plan
Injury and illness reporting and investigation process
7) Labor Practices
Compliance with local labor laws and regulations
Working hours and overtime practices
Employee compensation and benefits
Workplace safety and hygiene practices
Child labor and forced labor prevention measures
8) Supply Chain Management
Supplier selection and evaluation process
Supplier compliance with quality, environmental, and social standards
Product traceability and identification
Contract review and approval process
9) Compliance with Laws and Regulations
Compliance with relevant environmental, health and safety, and labor laws and regulations
Permits and licenses
Regulatory reporting and record keeping