Fasteners play an important role in industries such as automotive, aerospace, construction, and machinery manufacturing. These components ensure that parts stay securely connected, and the quality of fasteners is directly linked to the safety and reliability of the equipment. As such, ensuring the quality of fasteners through stringent standards and inspection methods is essential.
In an industry where precision and reliability are paramount, quality assurance is the backbone of our operations at RFI, here we’ll talk about the key aspects of fastener quality assurance, including QC standards, certifications, inspections, and best practices for selecting high-quality fasteners.
1. Fastener Quality Assurance
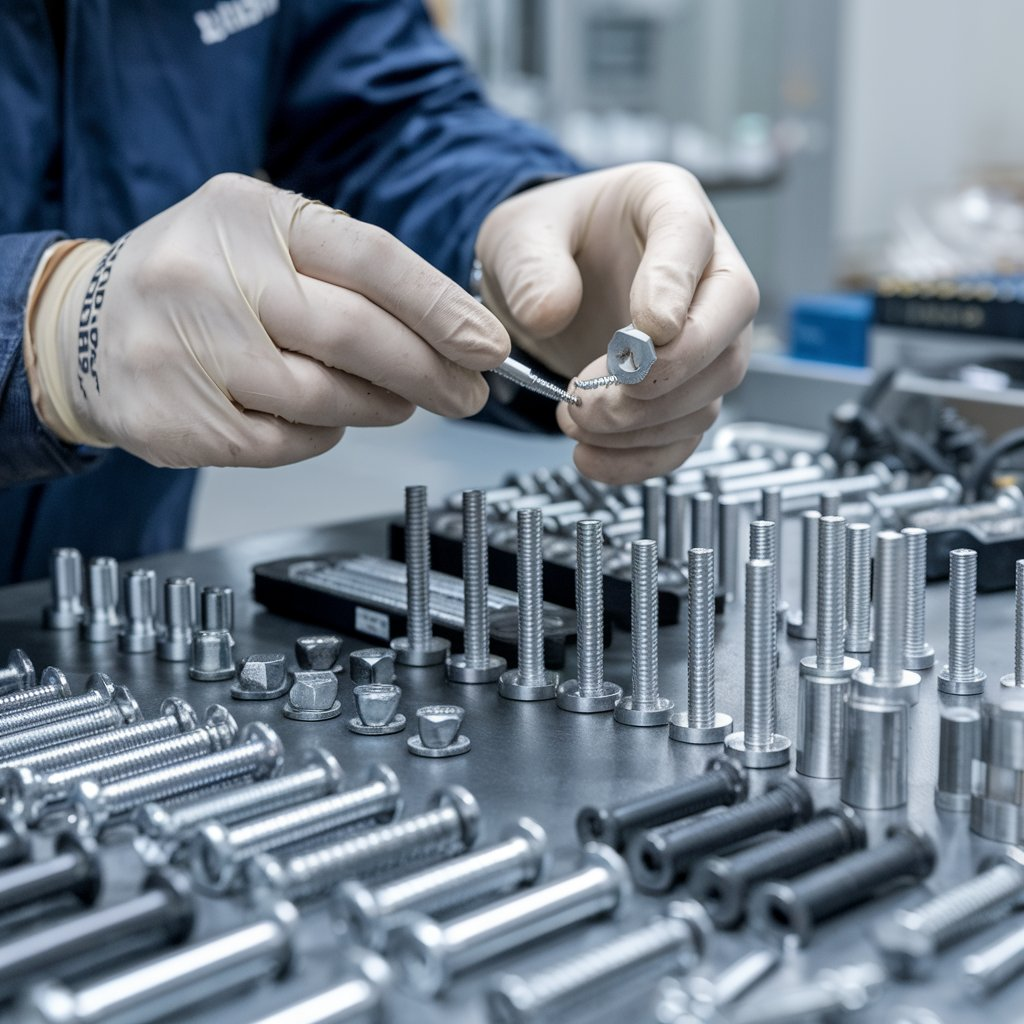
Quality Assurance (QA) refers to the activities undertaken to ensure that products and services maintain a predetermined level of quality. For fasteners, QA involves a comprehensive approach that spans from the selection of raw materials to customer service after delivery. QA focuses on the end product from the purchaser’s perspective and seeks to guarantee customer satisfaction and safety.
In contrast, Quality Control (QC) is more focused on ensuring that the manufacturing processes meet the required specifications from the manufacturer’s perspective. QC is an integral component of QA, as it ensures that production processes stay within the defined quality parameters.
1.1. View of Quality Assurance in Fastener Selection
The performance and cost of fasteners can vary significantly depending on factors such as size, material, shape, processing method, and surface treatment. At RFI, we ensure that fasteners are selected or designed to meet individual customer needs. This involves either sourcing from a wide variety of standard fasteners or manufacturing special parts tailored to specific applications.
1.2. Basic Rules of Fastener Quality
When selecting fasteners, it’s important to adhere to the following principles:
- Fasteners must be equal to or stronger than the assembled parts in terms of strength and durability.
- Bolt joints should never be a weak point in an assembly.
- Assembled fasteners should be replaceable and serviceable.
By following these rules, we ensure that the fasteners we recommend are robust and reliable.
1.3. Requirements for Fastener Selection
Average Product Life
The fasteners used should last as long as the product itself. Fasteners offer the advantage of being replaceable without damaging the product, but they should not be the weak point in the assembly.
Finish Requirements
Factors such as corrosion resistance, strength, load capacity, and cost must be considered. The environmental conditions and material selection are also critical.
Risk Assessment
We evaluate the risks associated with fastener failure, as defects can lead to catastrophic accidents. Our fastener recommendations are designed to minimize risk and ensure safety.
Thorough Quality Control
We define strict quality standards for fastener manufacturers, ensuring that raw materials are certified, manufacturing processes are documented, and inspections are thorough.
Communication with Customers
Understanding customer needs is the cornerstone of our fastener selection process. We work closely with our customers to recommend the best fasteners for their specific applications.
2. Fastener Quality Control Standards
To ensure that fasteners meet the required performance and safety criteria, the following quality standards must be adhered to:
Size Standards
Fasteners must comply with size standards to ensure proper fitting and fastening. These standards are typically outlined by international and industry organizations such as ISO, DIN, and ASME. Enterprises may also develop internal size standards based on specific application needs.
Material Standards
The material of the fastener is crucial for its mechanical properties and corrosion resistance. Common materials include carbon steel, alloy steel, and stainless steel, all of which must meet international material standards.
Surface Treatment Standards
Fasteners often undergo surface treatments like galvanizing, phosphating, or oxidizing to enhance corrosion resistance and improve appearance. Such treatments must meet established national and industry standards.
Strength Standards
Fasteners are subjected to various forces, making strength a key factor. Standards for tensile strength, yield strength, and impact strength ensure that fasteners can bear loads and resist fatigue according to international guidelines.
Tensile Standards
Tensile strength is crucial for ensuring reliable connections. Standards for static and dynamic load tensile testing are in place to ensure that fasteners can perform effectively under different conditions.
3. Fastener Quality Certification – ISO 9001:2015
In industries where precision and reliability are non-negotiable, quality assurance is the foundation of operations. While fasteners may be small, their impact is significant. A single defective fastener can cause catastrophic failures, making the commitment to quality paramount.
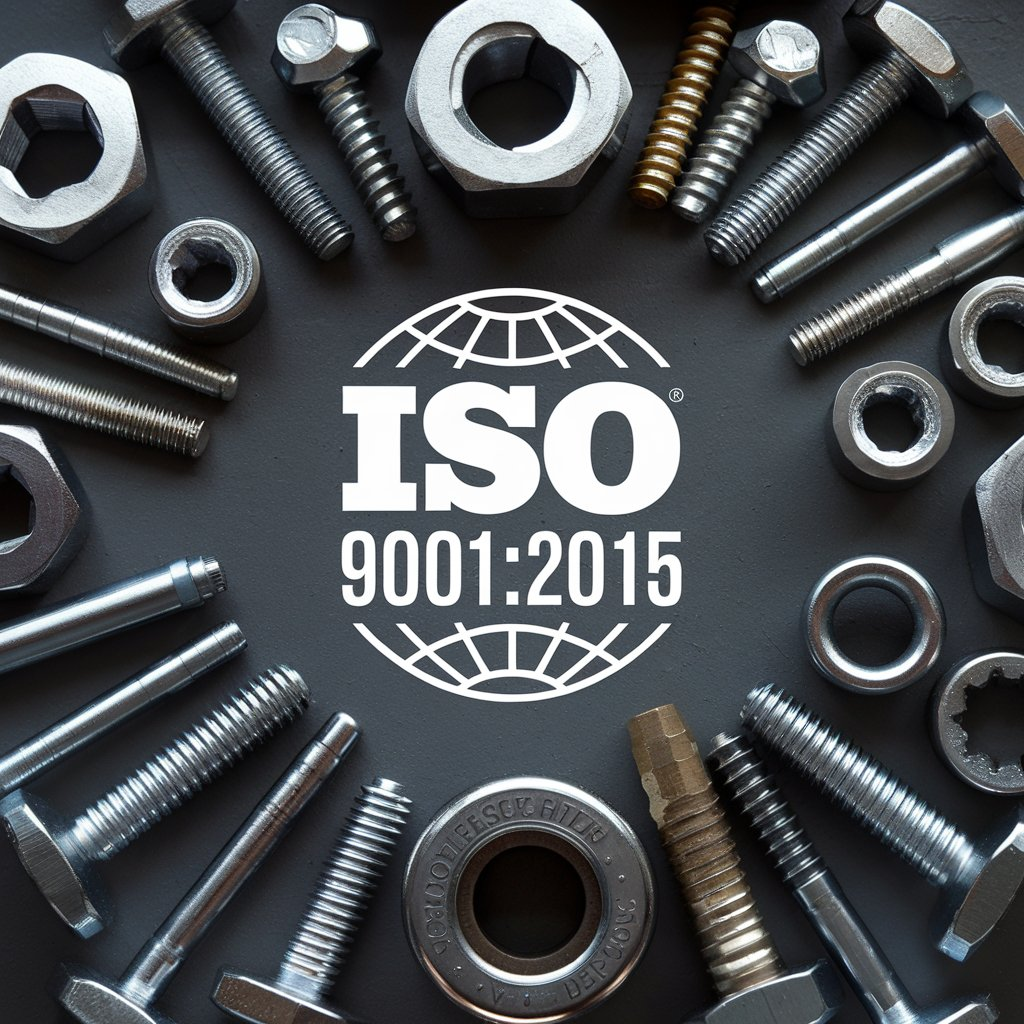
3.1. ISO 9001:2015 – The Gold Quality Standard of Fastener
ISO 9001:2015 is a globally recognized standard for quality management systems (QMS). For RFI, achieving this certification means:
- Process Optimization: Continual evaluation and improvement of manufacturing processes.
- Customer Satisfaction: Meeting and exceeding customer requirements is at the heart of our operations.
- Risk Management: Identifying and mitigating risks to ensure consistent production of high-quality fasteners.
3.2. What ISO 9001:2015 Means for Our Customers:
- Consistency: Every fastener meets stringent quality standards.
- Traceability: Complete documentation and traceability ensure accountability.
- Customer Focus: The certification ensures that our products and services consistently exceed customer expectations
3.3. Beyond ISO 9001:2015 – Our Commitment to Excellence
At RFI, our commitment to quality extends beyond certifications. We invest in in-house testing facilities and continuous improvement initiatives to ensure that our fasteners meet the highest standards.
In-House Testing
We conduct tensile strength, corrosion resistance, and dimensional accuracy tests to ensure our fasteners meet the requirements.
Continuous Improvement
Investing in the latest technologies and gathering customer feedback allows us to consistently improve our products and processes.
4. Fastener Inspection Methods (Case in Automotive Industry)
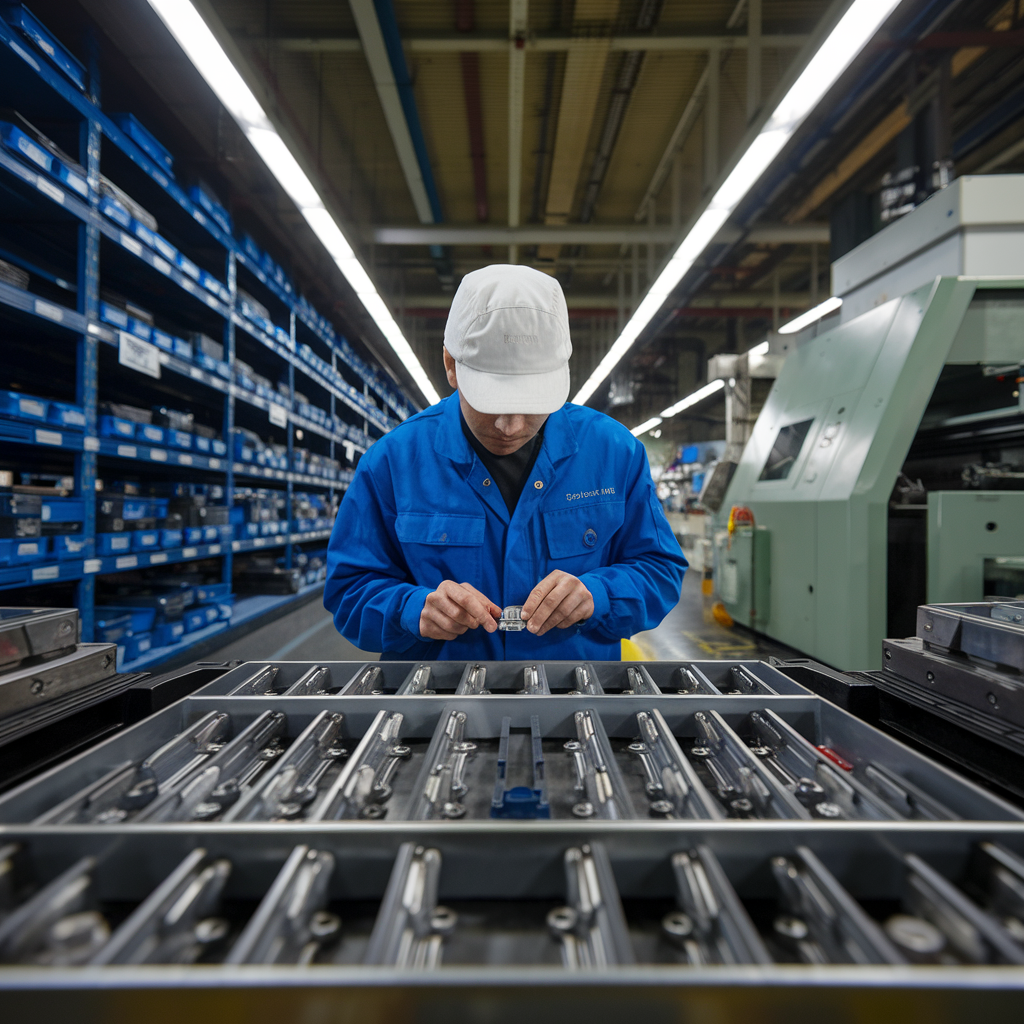
In 2024, a major automotive manufacturer faced a significant challenge when they experienced bolt failures in their engine assemblies. These failures led to engine malfunctions, resulting in costly recalls and reputational damage. The bolts in question were responsible for securing critical engine components, and their failure posed a serious risk to vehicle safety.
To address this issue, the manufacturer partnered with RFI to conduct a thorough quality inspection of their fasteners and implement more stringent quality assurance measures.
To ensure the fasteners meet the required quality standards, especially ISO 9001:2015, here are the common inspections can be carried out:
1. Initial Appearance Inspection
The first step in the process was to perform a visual inspection of the bolts. Using both the naked eye and microscopes, inspectors found surface defects such as small cracks and deformations that could compromise the integrity of the fasteners. These defects had previously gone unnoticed due to inadequate inspection protocols.
2. Dimension Inspection
Inspectors measured the bolts using precision tools like micrometers and calipers. It was discovered that a significant percentage of the bolts did not meet the specified dimensional tolerances, particularly in the thread pitch and shank diameter. These variances could result in improper torque application during assembly.
3. Chemical Composition Analysis
A chemical analysis was conducted to verify the material composition of the bolts. The analysis identified that some of the bolts did not meet the required material specifications. Specifically, the carbon content in the steel was lower than specified, reducing the tensile strength of the fasteners.
4. Tensile Strength Testing
Using a tensile testing machine, the bolts were subjected to load tests to determine their tensile and yield strength. Many of the bolts failed to meet the expected tensile strength, rendering them unable to withstand the forces typically exerted during engine operation.
5. Corrosion Resistance Testing
Given that the bolts were used in high-temperature environments, a corrosion resistance test was conducted using a salt spray chamber. The test revealed that the surface treatment of the bolts failed to meet corrosion resistance standards, particularly in areas where the surface coating was uneven or incomplete.
Results and Solution
After the comprehensive inspection, it was clear that the bolts in use were substandard due to failures in material quality, dimensional accuracy, and surface treatment. RFI worked closely with the automotive manufacturer to:
- Source new materials that met the required chemical and mechanical properties.
- Redesign the bolts to ensure that dimensional tolerances were within the required specifications.
- Apply advanced surface treatments to improve corrosion resistance.
- Implement in-line quality inspection methods to catch defects earlier in the production process.
As a result, the failure rate of the fasteners dropped to nearly zero, and the manufacturer was able to resume production with confidence. Furthermore, the improved quality assurance processes prevented future recalls and restored the manufacturer’s reputation.
Lessons Learned
This case study highlights the importance of comprehensive fastener quality inspection and ongoing quality assurance. By implementing robust inspection methods and adhering to stringent quality standards, manufacturers can avoid costly failures and ensure the safety and reliability of their products.
5. Partnering with RFI – A Commitment to Quality
When you choose Randack Fasteners India (RFI), you’re choosing a partner committed to delivering high-quality, reliable fasteners. Our rigorous quality assurance processes ensure that every fastener we provide meets the highest standards of performance and safety.
Let’s Talk Quality
We’re passionate about quality, and we’re here to help you with all your fastener needs. Contact us today to learn more about our quality assurance processes or to discuss your next project. Together, we can build something strong.