An auditor will generally audit factories or suppliers according to the audit form or checklist, which involves a new supplier system and process audit, annual supplier process audit, new project process audit, etc. Then what you may ignore during the process? What could you do to make the supplier audit more effective?
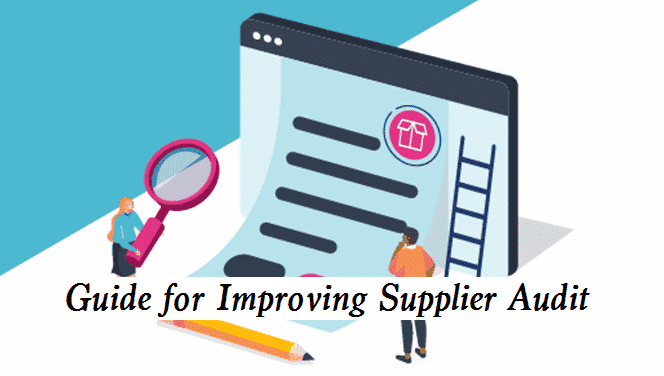
How Do You Audit Suppliers Effectively?
Generally speaking, auditors who have just started, will audit according to the audit table, which is mainly made according to ISO9000 and other systems or standards. However, can such a table accurately measure the quality assurance ability of a supplier? Not all effective. If you only audit your supplier’s quality management level according to this table, you can only be regarded as a junior auditor at most. How to select suppliers that can meet our quality requirements from a large number of candidate suppliers can be carried out from the following aspects in addition to scoring according to this table.
Tips for Improving Supplier Audit
Result analysis
The following three points are to evaluate the quality management level of suppliers from the resulting level.
- Generally speaking, the quality management level of large-scale suppliers is high, and the quality assurance ability of small factories is not as good as that of large factories (of course, it is not absolute, and there are exceptions sometimes). So before entering the door, first look at the factory scale and decoration level of the company, and then go to the production line to see its production scale. Finally, look at his financial statements, check his sales growth in recent years, and judge the overall scale and development speed of the company through these. Generally speaking, companies with large scale and fast development speed also have high-quality management levels.
- It’s not enough to just understand these. Another important point is which manufacturers are the main customers of this supplier. Whether the quality requirements of his main customers are at the same level or higher than those of our company. To find out the evidence in this regard, we can check the billing system of the supplier to see which customers his invoices are issued to and whether they are consistent with the main customers claimed. In order to find the objective facts, it is difficult to fake all the invoices issued by the supplier to a major customer within a period of time.
- In order to further find out the quality management status of the supplier, another trick is to check the quality evaluation given to him by his main customers. The data of the quality evaluation conducted by a supplier’s customers can often objectively reflect his quality management level.
Process management level
- Check whether the supplier has a clear identification and definition of his product realization process. In other words, is there a process diagram that runs through all businesses of the company, which is the basis of process management? The business processes of suppliers in different industries are completely different. Among these processes, some are key processes, which play a very key role in the final product quality of suppliers. At this time, we can view the company’s production process flow chart, FMEA, and control plan. Understanding the management details of these key processes is the embodiment of the auditor’s professional ability. As a new auditor, your knowledge is limited, but it doesn’t matter if you don’t understand it. You can first find a supplier with a high management level in the industry and conduct a process audit to understand how each process of his product realization is managed, especially the management requirements of his key processes must be very clear. We call this benchmarking. Based on this supplier’s process management method, you can audit other suppliers producing the same type of products. You will gain a lot by doing so.
- Check whether the quality indicators of each process of the supplier are clearly defined. Whether the quality data is collected and whether the chart is made to show the quality trend after data collection. Whether his quality indicators can be seen by the boss quickly and how they can be seen in real-time. If visual management is achieved, the manufacturer will be given extra points. When checking that some of his KPIs (key performance indicators) are not up to standard, what improvement measures have been taken, what is the status of the improvement measures, whether they are closed or in progress, or have not been implemented or even have no improvement plan? There are only KPI results but no improvement measures. No matter how good the KPI statistics are. Here we can refer to PDCA theory in quality management. This paper does not elaborate on this theory. Interested friends can learn and understand it by themselves.
- The most important point is whether the supplier manages its key processes in place. For example, this process is the key process of detecting surface cracks. If it is not detected, it will produce many potential quality problems, among which the biggest hidden danger is the fracture of parts, resulting in vehicle safety accidents.
- Whether the supplier’s quality organization has the right to speak. The quality department is a department responsible for quality improvement. If its quality director has a certain power, he or she occupies a place in the company’s decision-making system and can report to the boss independently. Such suppliers often have a high level of quality management. Another point is to see the attitude of employees in other departments towards the quality department and whether they respect the employees of the quality department. In addition, the personnel composition of the quality department is also very important. If a quality department has only inspectors and no or few quality engineers, the general quality management level of such suppliers will not be high.