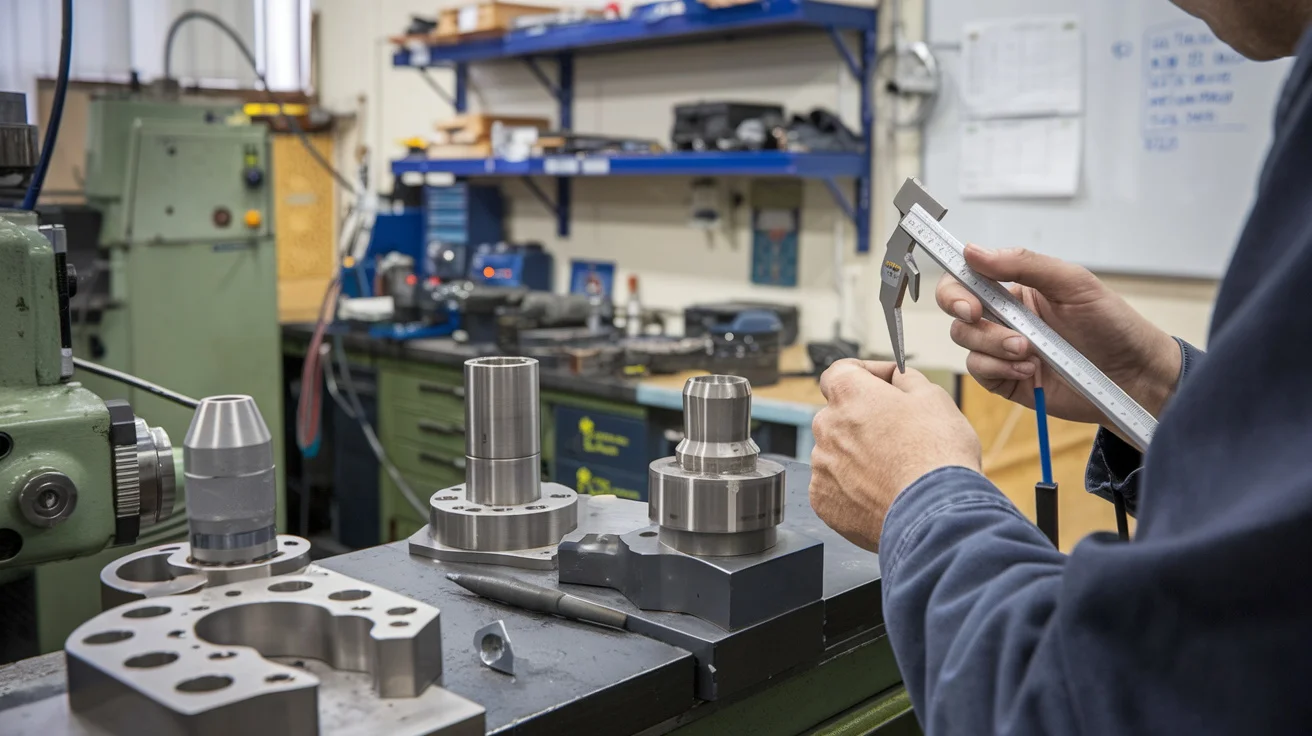
Maintaining tight dimensional tolerances in the precision manufacturing industry is critical to ensuring product functionality, safety, and overall quality. Whether you’re producing components for aerospace, automotive, medical devices, or consumer electronics, understanding the nuances of dimensional tolerances is key to delivering reliable results. In this blog, we explore what dimensional tolerances are, why they matter, and how inspection processes play a vital role in achieving and maintaining them.
What Are Dimensional Tolerances?
Dimensional tolerances refer to the permissible limit of variation in a physical dimension of a manufactured part. They define how much a part’s actual size can deviate from its nominal (intended) size while still meeting functional requirements. Tolerances are typically expressed in ± terms, such as ±0.01 mm.
Types of Tolerances
- Linear Tolerances: Control features like length, width, and height.
- Geometric Tolerances: Address form, orientation, and position, including flatness, roundness, and parallelism.
- Angular Tolerances: Govern angles between surfaces or features.
Why Do Dimensional Tolerances Matter?
A. Functional Fit
In assemblies, even slight deviations can result in parts that fail to fit or function as intended. Maintaining tolerances ensures seamless compatibility between components.
B. Performance and Safety
Critical applications, such as medical implants or aerospace components, demand precision to avoid failures that could lead to catastrophic consequences.
C. Cost Efficiency
While tighter tolerances increase production complexity and cost, they can reduce the likelihood of downstream failures or product recalls, saving money in the long term.
D. Regulatory Compliance
Industries like automotive and electronics adhere to strict standards for tolerances to ensure products meet safety and performance benchmarks.
Challenges in Maintaining Tight Tolerances
1. Material Variability
Different materials react differently to machining, molding, or forming processes. For instance:
· Metals can expand due to thermal changes during machining.
· Plastics may shrink unevenly during cooling in injection molding.
2. Tool Wear
Over time, cutting tools, molds, and dies wear out, leading to less precise dimensions. Regular tool maintenance is essential to minimize deviation.
3. Environmental Factors
Temperature, humidity, and other environmental conditions can cause dimensional changes in both materials and machinery.
4. Complex Geometries
Parts with intricate designs or thin walls can be challenging to manufacture within tight tolerances.
Role of Inspection in Maintaining Tolerances
A. Dimensional Inspection
Inspection ensures manufactured parts fall within specified tolerances. Common inspection techniques include:
· CMM (Coordinate Measuring Machines): Measure complex geometries with high accuracy.
· Optical Scanners: Provide 3D measurements of parts, ideal for intricate designs.
· Calipers and Micrometers: Offer quick and reliable measurements for simple features.
B. Statistical Process Control (SPC)
SPC monitors production processes to detect trends or deviations early, allowing corrections before defects occur.
C. First Article Inspection (FAI)
FAI verifies that the first parts produced meet all design specifications, preventing costly errors in mass production.
D. GD&T (Geometric Dimensioning and Tolerancing)
Using GD&T standards allows manufacturers to define tolerances more comprehensively, reducing ambiguity and improving quality.
Best Practices for Managing Dimensional Tolerances
1. Collaborate Early in Design: Involve engineers, manufacturers, and inspectors during the design phase to set realistic and achievable tolerances.
2. Use High-Quality Equipment: Invest in precision tools and maintain them regularly to ensure consistent output.
3. Automate Where Possible: Automated systems reduce human error and improve inspection efficiency.
4. Leverage Advanced Analytics: Use data analytics to identify process variations and optimize production.
5. Train Personnel: Ensure that operators and inspectors understand the importance of tolerances and are skilled in using measurement tools.
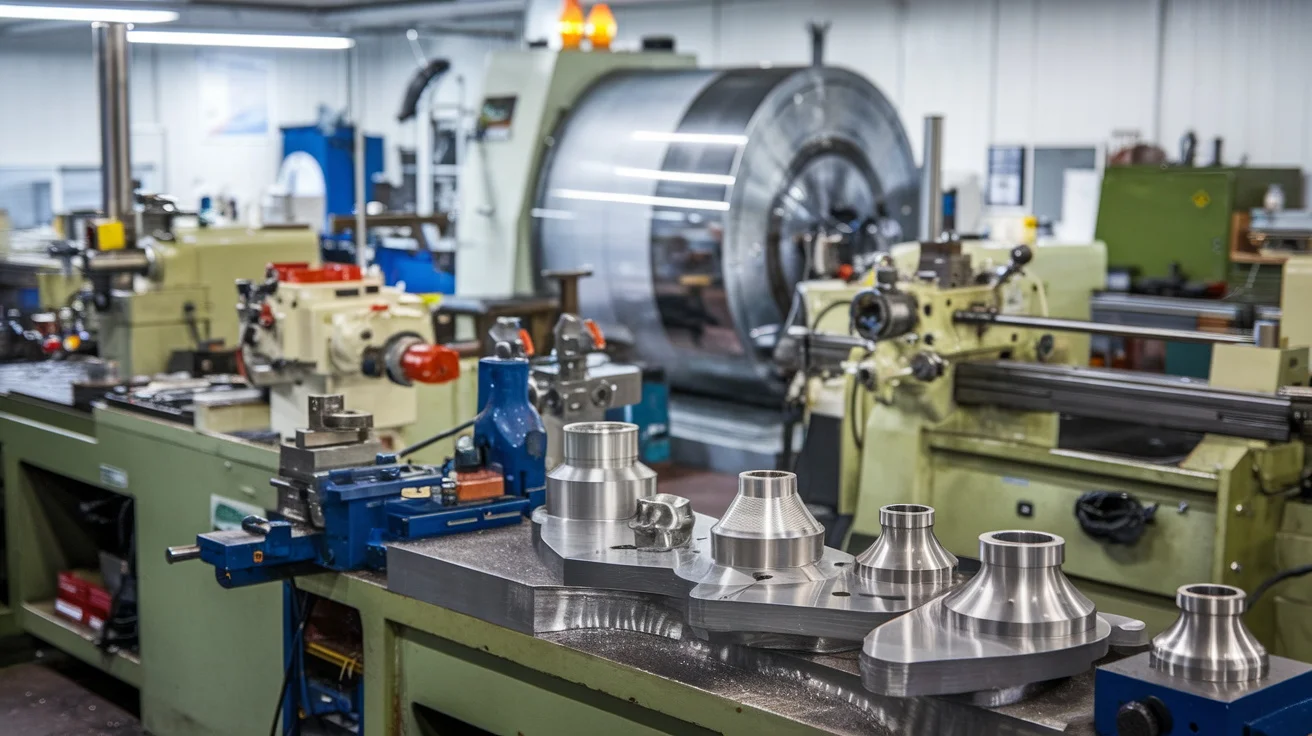
Future Trends in Dimensional Control
1. AI-Driven Inspection
Artificial intelligence is enabling smarter inspection processes, analyzing data in real time to detect patterns and predict failures.
2. Digital Twins
Digital twin technology allows manufacturers to simulate processes virtually, identifying potential tolerance issues before physical production begins.
3. Additive Manufacturing
Advances in 3D printing are improving precision capabilities, reducing the challenges of maintaining tight tolerances in complex geometries.
4. Sustainable Manufacturing
New materials and processes are being developed to achieve precision while reducing environmental impact.
Dimensional tolerances are the cornerstone of precision manufacturing, impacting everything from product functionality to overall cost efficiency. By adopting robust inspection practices, leveraging technology, and fostering collaboration, manufacturers can consistently meet tolerance requirements and deliver exceptional quality. As innovation continues to reshape the manufacturing landscape, staying ahead of trends will be critical to maintaining competitiveness in a demanding market.