Traceability is an important term used in quality control, it combines the world trace and ability. What is traceability and how do you implement product traceability? Follow us to understand the importance, types, and implementation of traceability.
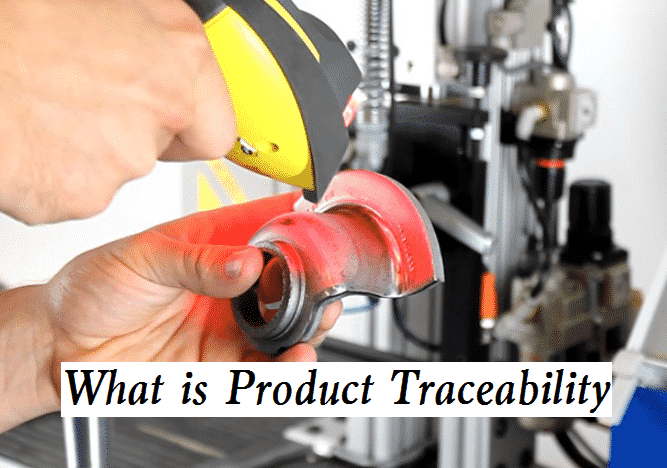
What is Product Traceability?
Product traceability refers to the ability to track the process of a product from the selection of raw materials to delivery and trace the history, application, or location of an item through record identification.
The definitions are also different in different industries such as automobile, electronic parts, food, and medical treatment. In the manufacturing industry, the meaning is: traceability records the information of manufacturers, suppliers, and sellers in various processes from the procurement of raw materials and parts to processing, assembly, circulation, and sales, so as to make them in the state of traceable historical records.
Importance of Product Traceability
In case of quality problems, manufacturers must take effective measures quickly. If the measures are inappropriate or taken too late, it may increase the mistrust of consumers or customers, and even make it difficult for enterprises to survive. In addition, with the formulation of consumer protection laws, the cases of rapid recall of problematic products as an enterprise obligation are also increasing year by year, and product traceability is also an issue that manufacturers must pay attention to.
Traceability is an effective tool to ensure food safety. At present, government agencies and consumers in many countries require the establishment of a traceability mechanism of the food supply chain, and many countries have begun to formulate relevant laws to bring traceability into the food logistics system in the form of regulations. In many countries in Europe and America, food without traceability has been banned from entering the market.
Classification of Traceability
There are many definitions of traceability, which can be roughly divided into supply chain traceability and internal traceability.
1)Supply chain traceability
The general concept of traceability is equivalent to supply chain traceability. Supply chain traceability refers to the status of historical records from the purchase of raw materials and parts to processing, circulation, and sales. Manufacturers can know where their products are going, and downstream operators or consumers can know where their products are coming from. Therefore, for manufacturers, in case of unexpected problems in products, traceability is conducive to the investigation of causes and recycling. In addition, for consumers, traceability can be used as a selection indicator of high-reliability products and eliminate concerns about false labeling.
2)Internal traceability
Internal traceability refers to the traceability of mastering the trend of parts and products within a limited specific range in an enterprise or factory in the overall supply chain. For example, in an engine assembly factory, engine parts such as camshafts and pistons are purchased from suppliers and assembled. The information of managing and using the manufacturing history and inspection results of these products can also be called internal traceability.
How to Implement Product Traceability?
In traceability, the manufacturer will use the accumulated information to track the product trend, which is called forward tracing (tracking), and the backward search for records in chronological order is called backward tracing (tracing). Traceability identifies products in individual or batch units and accumulates information in each process. It is precisely because this information can be accessed, tracked, or traced at any time that traceability can be realized.
- Forward tracing (tracking): when a part is judged to be defective, the instrument and place of shipment using the part will be locked, and the product can be accurately recycled. Forward tracing is conducive to recalling or taking measures for defective products.
- Backward tracing (tracing): when there is a problem with the ex-factory instrument, you can quickly investigate the cause by tracing the manufacturing record, locking the affected batch or process. Backward tracing is helpful to quickly grasp and improve the problems in the manufacturing process.
An important way to implement traceability management is to paste traceability labels on products. The traceability label records the readable identification of food. Through the code in the label, it is convenient to find detailed information about food in the food database. The traceability label can also help enterprises determine the flow direction of products and facilitate the tracking and management of products.