When sourcing or manufacturing products, ensuring quality is paramount. One way to safeguard your investment and brand reputation is by conducting product inspections. However, many businesses, especially smaller ones or startups, often ask, “How much does product inspection cost?” The answer varies based on several factors, including inspection type, location, and the complexity of your product. In this blog, we’ll break down the costs associated with product inspections and explore how to maximize your quality control budget.
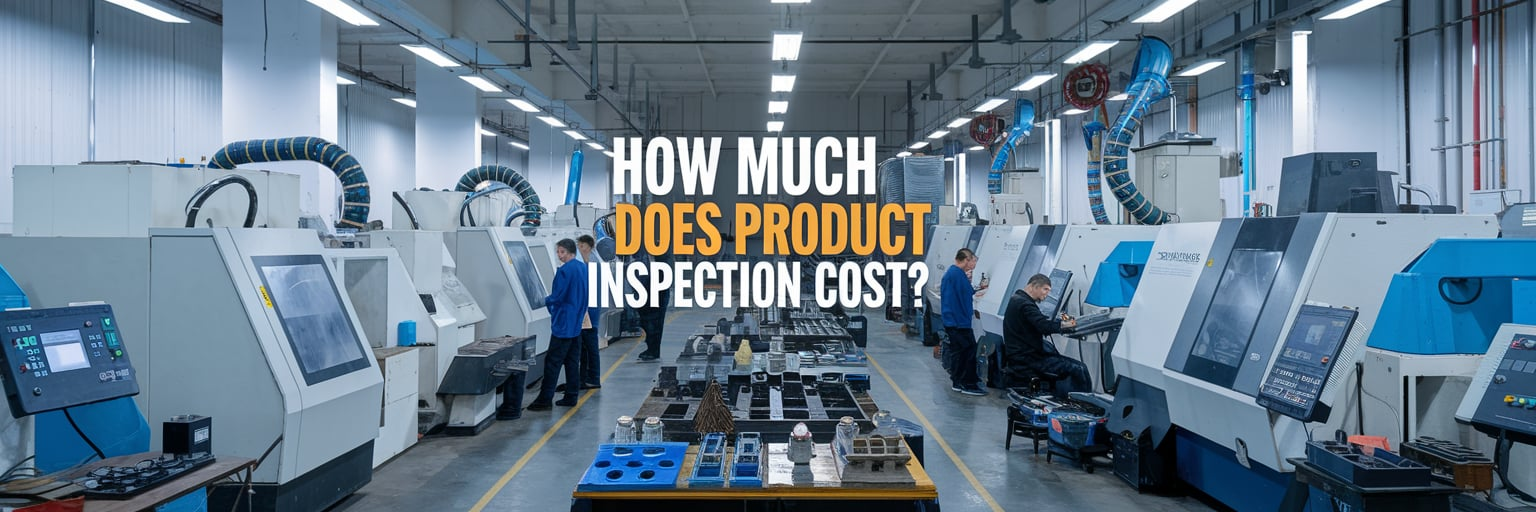
1. Factors Affecting Product Inspection Costs
The cost of a product inspection depends on several variables:
a. Type of Inspection
Different inspection types come with varying levels of complexity and associated costs:
· Pre-Production Inspection: Verifies raw materials and initial setup to prevent defects early.
· During Production Inspection (DUPRO): Conducted when 20-50% of the production is complete. It identifies issues before mass production is finished.
· Pre-Shipment Inspection (PSI): Ensures that finished goods meet specifications before shipment.
· Container Loading Check (CLC): Ensures the correct products and quantities are loaded securely for transport.
Each of these inspections involves distinct procedures and time commitments, which influence costs.
b. Location of the Supplier or Factory
Geographical location significantly impacts inspection costs.
· Developed regions such as North America and Europe often have higher inspection fees due to higher labor costs.
· Emerging markets like China, Vietnam, or India tend to offer more affordable inspection rates but may also require more frequent checks due to varying manufacturing standards.
c. Product Complexity
Products with intricate designs, multiple components, or strict regulatory requirements (e.g., electronics, medical devices) require more time and expertise to inspect, thus raising costs.
d. Inspection Service Provider
Whether you choose a third-party inspection service, an in-house team, or a dedicated quality assurance partner will impact the cost.
2. Typical Pricing Models for Product Inspection
Inspection providers generally charge based on one of the following models:
a. Per Man-Day Rate
This is the most common pricing structure. A man-day refers to one inspector working a full day (typically 8 hours).
· Rates: $200–$400 per man-day in Asia, $400–$800 per man-day in Western countries.
This model is ideal for larger production volumes, where multiple man-days may be required.
b. Flat Fee Per Inspection
Some companies offer a flat rate for specific types of inspections, particularly for smaller orders.
· Rates: $150–$300 for standard inspections in Asia.
c. Customized Packages
For businesses with ongoing inspection needs, many providers offer discounted packages. These may include regular audits, multiple inspections, or additional services like laboratory testing.
3. Additional Costs to Consider
While inspection fees are straightforward, other associated costs may impact your budget:
a. Travel and Accommodation Costs
If inspectors need to travel to remote factory locations, you may be responsible for their transportation and lodging expenses.
b. Product Sampling Costs
For certain inspections, especially destructive testing, a sample of products may be taken for testing, leading to additional costs.
c. Follow-Up Inspections
If defects are found, a second or third inspection may be required after corrective actions, adding to your overall cost.
4. Is Product Inspection Worth the Cost?
Although product inspections come at a price, their value far outweighs the cost. Here’s why:
a. Prevent Costly Returns and Rework
A single defective batch can result in expensive returns, lost sales, or even reputational damage. Inspections help catch defects early, preventing these issues.
b. Ensure Compliance
Many industries, such as automotive, aerospace, or electronics, have strict regulations. Failing to comply can lead to legal fines and product recalls.
c. Build Customer Trust
Customers are more likely to remain loyal to brands that consistently deliver high-quality products. Inspections help ensure that your products meet their expectations.
5. How to Reduce Inspection Costs Without Compromising Quality
While inspections are necessary, there are ways to optimize your budget:
a. Partner with Local Inspectors
Hiring inspectors located near your supplier reduces travel expenses and ensures quicker responses.
b. Focus on Critical Points
If your budget is limited, prioritize inspections on the most critical aspects of your product, such as safety features or compliance standards.
c. Combine Inspections
Scheduling inspections that cover multiple checkpoints in one visit can save time and money. For example, combining a DUPRO and Pre-Shipment Inspection may reduce costs.
d. Work with Reliable Suppliers
Choosing manufacturers with proven track records for quality can reduce the frequency and depth of inspections required over time.
6. Choosing the Right Inspection Service Provider
When selecting an inspection provider, consider:
· Reputation and Experience: Look for companies with a strong track record in your industry.
· Coverage and Availability: Ensure they operate in your supplier’s region and offer flexible scheduling.
· Reporting Standards: Detailed reports with photos and actionable insights are essential for making informed decisions.
Conclusion
The cost of product inspections varies widely, but their role in ensuring quality and protecting your business is invaluable. By understanding the factors that influence inspection costs and implementing cost-saving strategies, you can optimize your quality control processes while staying within budget.
Investing in inspections is not just about quality—it’s about building a brand that customers trust and ensuring long-term success.