Generally speaking, in the process of product development, the product quality problems are often from the design, and the solution generally starts from analyzing problems, solving solutions to improving the design. After mass production, there are also design problems, but they may also be caused by production process deviation or part quality variation. Moreover, because the products have been sold and have inventory, the process of solving the problem is much more complicated. The source of the problem is found by the manufacturing department or the quality testing department, and some occur when the customer uses it. How do we control the quality of mass production?
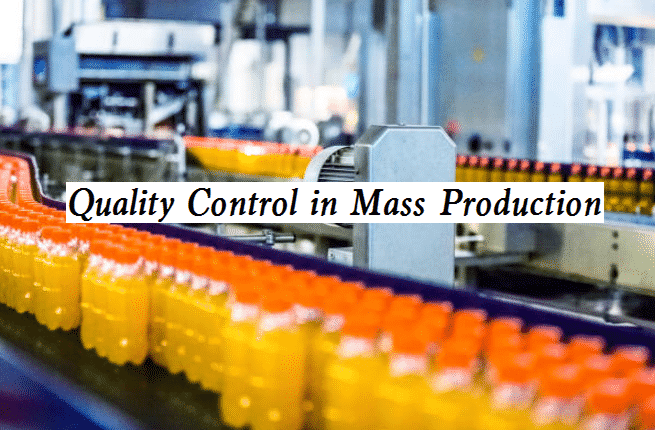
How to Control the Quality in Mass or Batch Production?
These are the basic steps to deal with quality problems after mass production. The quality control after mass production is extremely complex and cumbersome. It is full of judgment, decision-making, technology, company operation, quality, and many other problems, which affect the company from top to bottom and cost a lot.
1) The first step is to find a way to reproduce the problem. If a problem is difficult to reproduce, it is difficult to reproduce it in your own laboratory. Under what conditions does the problem occur? What is the defect rate? For example, when a customer complains that the product is powered off, we must find out under what circumstances the product is powered off?
2) Next, identify the nature of the problem and how serious is the problem? Is it a general quality problem or a safety problem? Some problems may not be problems. The product design specifications do not support such functions. For example, an ordinary mobile phone did not have a waterproof design. As a result, someone dropped the mobile phone into the water and damaged it, which was caused by serious improper use. Generally speaking, it is no longer solved. The first two steps are mainly to clarify the nature of the problem.
3) After the basic nature of the problem is clarified, such as the severity of the problem, the probability of the occurrence of the problem, the conditions for the recurrence of the problem, etc., at this time, it is necessary to consider the basic situation of the production line, whether to stop the line immediately, etc., because if the line is not stopped, it is possible to produce more defective products, etc.
4) Engineers should immediately enter the problem analysis program, which is the technical work we usually talk about. They should do all kinds of experiments, analyses, observations, and even look back at the test report in the product development stage. And preliminarily identify whether it is caused by design problems or other variations. If the design phase test is good, and the same test is wrong now, it can generally be judged that it is not a design problem.
5) The process of analyzing the causes of problems is also the process of exploring solutions to problems. These two are constantly repeated conjectures and verification. It should be noted that the closed-loop verification mentioned earlier is also used to determine the effectiveness of the solution. To find a solution, make new samples to test and verify.
6) When the cause of the problem is locked, the solution to the problem generally appears. If it is a part quality problem, we have to talk to the part supplier. Sometimes we can only identify the problem of the part, but we don’t know the cause of the problem. In this regard, the supplier is actually more professional than us. The supplier should find out the deeper problems, how to improve them and what the solution is, and report them to us, The improved samples should be provided to us for testing to see if they are good in the end.
7) Process control, such as how to control the process of the parts supplier, whether special control methods are needed, how to inspect, how to inspect the incoming inspection of our own company, whether special attention is needed, etc. What should we pay attention to in the assembly test of our finished products? Do you want to modify the production test and so on? These factors, such as effectiveness, simplicity, and economy, should be taken into account to find the most appropriate method.
8) After these are confirmed, send an engineering change notice (ECN) through the file system, import new versions of materials, and control run to see the production status after the introduction of improvement measures.
9) We also need to discuss how to deal with the things that have been shipped, for example, whether there is a need for a recall, and how to deal with the inventory? Do you want to rework it?