In previous articles, we have explained the perspective of how the designed mechanical parts are manufactured. This time, we would like to change our perspective a little and introduce how the manufactured machine parts are quality guaranteed.
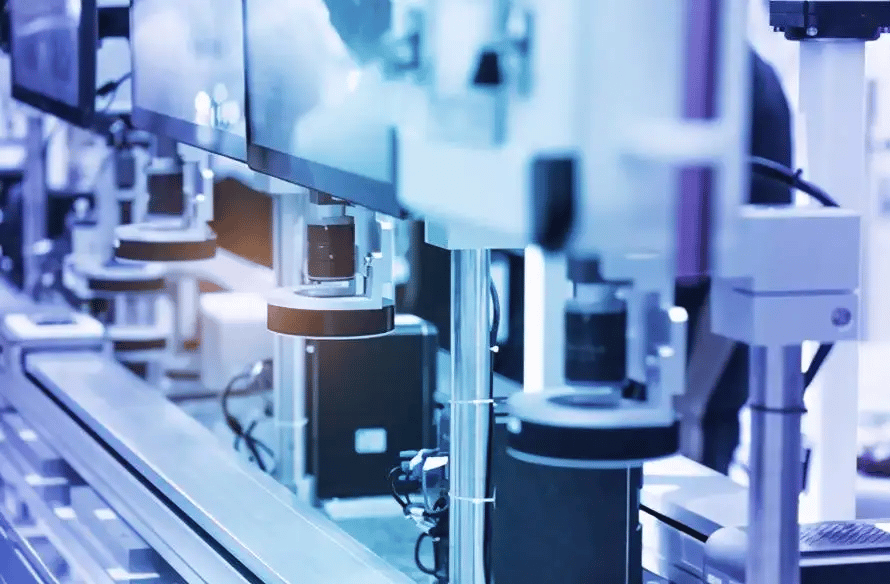
1. What is quality assurance of mechanical parts?
Quality assurance of mechanical parts is nothing more than ensuring that the manufactured parts are made according to the drawings. Here, we will introduce how quality is guaranteed at the manufacturing site from a practical perspective.
Quality assurance is “proving that what we have made meets the requirements of our customers.” Among them, in the practical aspects of the processing site, the main work content is to check the specifications (material, surface treatment, etc.) and dimensions of the manufactured parts by inspection and check whether they are completed according to the drawings.
First, let’s briefly introduce the quality control system required for quality assurance and the positioning of inspection work.
1.1 Quality Control System
At many manufacturing sites, we have established a quality control system that complies with the requirements of quality standards such as ISO 9001. To summarize the essence, I think that there are many manufacturing sites that have the following quality control system.
(1) Create, operate, and store quality manuals and other documents that stipulate quality control methods, procedures, standards, etc.
(2) Establish a quality control department and assign a person in charge of it.
(3) Create, operate, and store quality records and other record documents
(4) Assign inspectors from the quality control department, train them, and evaluate their competencies.
(5) Prepare the equipment necessary for quality control, and operate and store it in an appropriate environment.
(6) Appropriately confirm and manage quality in the process of product realization
The wording is quite formal, but the purpose is “Let’s establish and document quality control standards and methods and operate them accordingly.”
(1)~(4) is more important than the construction of internal systems, education, and management, and is a higher-level activity than practice.
Think of (5) and (6) as the work actually performed at the manufacturing site.
1.2 Quality Control and Inspection Operations
Depending on the manufacturing site, the quality control department is an organization called the “Quality Assurance Department” or “Inspection Department”. In addition, “inspectors” who exclusively perform inspection work belong to the department, and are mainly responsible for measurement work such as dimensional measurement. Basically, inspection work is the work of confirming whether machine parts are manufactured according to the drawings.
There are also inspection processes during the manufacturing process to ensure final quality. Inspection work generally consists of the following three processes.
(1) Acceptance Inspection
This is an inspection process that confirms the quality of materials and purchased products before they are used in our own process. We check the standards, dimensions, and appearance of materials and outsourced processed products for scratches and bruises. Later, when a problem is discovered during an in-process inspection or pre-shipment inspection, it may be very important whether it has been confirmed by the incoming inspection. In addition, in order to confirm that the outsourcing process such as materials and heat treatment is in accordance with the instructions in the drawings, we obtain material certificates (so-called mill sheets) provided by suppliers and various certificates and store them after verification.
In the process of the manufacturing process, the dimensions required for quality control are confirmed by inspection. In some cases, the inspection department performs precise inspections for each processing process, and in other cases, the operator inspects them on the machine. The contents of the inspection are generally recorded and stored in quality record documents such as “in-process inspection tables” and “process control tables”.
This is the final inspection process that is carried out by the quality control department again before shipment after the manufacturing process is completed. Various measuring instruments are used to check whether the product conforms to the instructions in the drawing.
The inspection results are generally recorded in the “inspection table” and kept as a quality record or submitted to the customer together with the product. If, as a result of the inspection, there is a deviation from the drawing instructions, corrections are made by additional work, etc., and inquiries are made to the customer to determine whether the product is good or bad.
In addition, measuring instruments are regularly “calibrated” by the measuring instrument manufacturer to ensure measurement accuracy. The “calibration certificate” of the measuring instrument is also kept as a quality record. It is important to have “traceability” for quality records so that when there is a problem on the user side, it can be retroactively confirmed whether there was any abnormality in the manufacturing process.
2. Inspection and inspection equipment effective for quality assurance
In general, in the quality assurance of mechanical parts, it is important to check whether the materials and surface treatment are in accordance with the drawings, and to measure whether the dimensions and geometric tolerances are satisfied according to the drawings by inspection. Here, we will explain the inspection items of actual dimensional measurement and the details of the measuring instruments used.
When designing, it is important to anticipate what kind of inspection equipment will be used in the end. In some cases, there are cases where “processing is possible, but inspection is not possible.”
2.1 Visual inspection
Visual inspection is an inspection that observes the exterior surface of a product visually or with a magnifying glass to confirm that there are no scratches or bruises. In quality assurance inspection, it is easy to focus only on measuring dimensions, but the first thing to do is to make sure that there are no problems with the appearance.
Of course, in addition to checking for scratches and bruises on the exterior, we also check the degree of burrs and surface roughness. Especially in the case of mechanical parts, burrs are inevitable, so it is necessary to confirm with the designer in advance to what extent they are allowed. Normally, when you touch it with a nail or mechanical pen lead, the guideline for burrs is whether there is a snag. If burrs are confirmed, they are returned to the finishing process to deburr. If the drawing instructs that “the corner part without instructions is the thread chamfer”, the burrs will be removed by thread chamfering. When designing, be sure to instruct the processing of such corners.
The surface roughness can be measured numerically with the surface roughness measuring instrument described later, but in many cases, the surface roughness standard pieces as shown in Fig. 2-1 are compared and confirmed.
If there is an instruction on surface roughness (for example, Ra3.2) in the drawing instructions, I think it is common to check it by visual inspection in this way, and if there is a problem, strictly measure it with a surface roughness measuring instrument.
2.2 Inspection with measuring instruments
In the inspection process in quality assurance, dimensional inspection is mainly performed using general-purpose measuring instruments such as calipers and micrometers. The reading dimensions of these measuring instruments change depending on how they are handled. Precise handling is required as shown below.
Calipers (dial calipers)
Calipers are measuring instruments that mainly measure length. It can be said to be a general-purpose measuring instrument that can measure outer dimensions, inner dimensions, depth, etc. using various parts. There are various sizes depending on the measurement range, but the measurement error increases as the measurement range increases. Depending on the measuring range, it is important to select as small a caliper as possible. Normally, a dial-type caliper as shown in the figure below is used, but there are also digital calipers that display the measured dimensions digitally.
Inner diameter micrometer (Hall test Holtest)
An inner diameter micrometer is a measuring instrument that measures hole diameter. Since each measurement range is different, it is important to select one with a measurement range according to the hole diameter.
Dial Thickness Gauge
The dial thickness gauge is a measuring instrument that measures thickness. It is effective when measuring the wall thickness of a shape in a recessed place that cannot be measured with a caliper or a shape with a undulating shape.
Depth gauge
A depth gauge is a measuring instrument that measures depth.
Height gauge
A height gauge is a measuring instrument that measures the height and level difference of a product. By placing the product on the surface plate, the relative height can be measured accurately and quickly.
Pin gauges and cork gauges
Pin gauges and plug gauges are measuring instruments that measure hole diameters. With a precision-made cylindrical gauge, it is actually put into the hole shape and the accuracy of the inner diameter is checked by whether it enters smoothly.
Screw gauge
A screw gauge is a measuring instrument to ensure that a threaded hole meets the standard. The thread gauge has the same gauge grade as the thread to be measured. Make sure that the street side and the stop side are attached, that the screw enters on the street side, and that it does not enter more than specified on the stop side.
R gauge, C gauge
The R gauge is a measuring instrument for checking whether the R-plane part and the C gauge is within the intersection.
2.3 Coordinate measuring machine
In the quality assurance inspection process, there are cases where the general-purpose measuring instrument described in 2.2 alone cannot be sufficiently measured. For example, when measuring the dimensions of complex shapes, geometric tolerances, etc. In such cases, coordinate measuring machines are used.
A coordinate measuring machine is a measuring instrument equipped with a mechanism that drives the X-axis, Y-axis, and Z-axis, similar to milling machine tools such as machining centers. It differs from machine tools in that instead of a rotary tool for sharpening workpieces, it is equipped with a probe for measuring. By bringing the tip of this probe into contact with the product, the three-dimensional coordinates of the point of contact are recognized and recorded.
By measuring the coordinate information of various points, it is possible to determine the plane and diameter, and to calculate the positional relationship between shapes. For this reason, it is possible to measure geometric tolerances that cannot be measured with general-purpose measuring instruments.
However, the coordinate measuring machine itself is very expensive and requires specialized skills for measurement. In addition, in order to maintain measurement accuracy, it is necessary to use it in a space with constant air conditioning (approximately 20±1°C, etc.), and it must be installed on a rigid ground with low vibration.
2.4 Summary of inspection items and inspection equipment
The inspection process is the work of measuring the requirements instructed in the drawings in a rational manner and confirming that they meet the required values.
Although the above-mentioned coordinate measuring machine is a versatile measuring instrument, general-purpose measuring instruments such as micrometers often have higher measurement accuracy when measuring specific dimensions. It is important to use different measuring instruments depending on the measurement items.
In this article, we explained the quality assurance of machine parts. If you know in advance how the mechanical parts you design are actually manufactured and their quality is guaranteed, it will be easier to imagine how to deal with and check when something goes wrong.