Injection molding is a widely used manufacturing process that enables the production of intricate plastic parts with precision and efficiency. However, like any manufacturing process, it is not without its challenges. One common issue encountered in injection molding is short shot, which refers to an incomplete filling of the mold cavity. In this comprehensive article, we will delve into the complexities of short shot in injection molding, explore the most popular opinions on its causes, and provide effective solutions and best practices for fixing this issue.
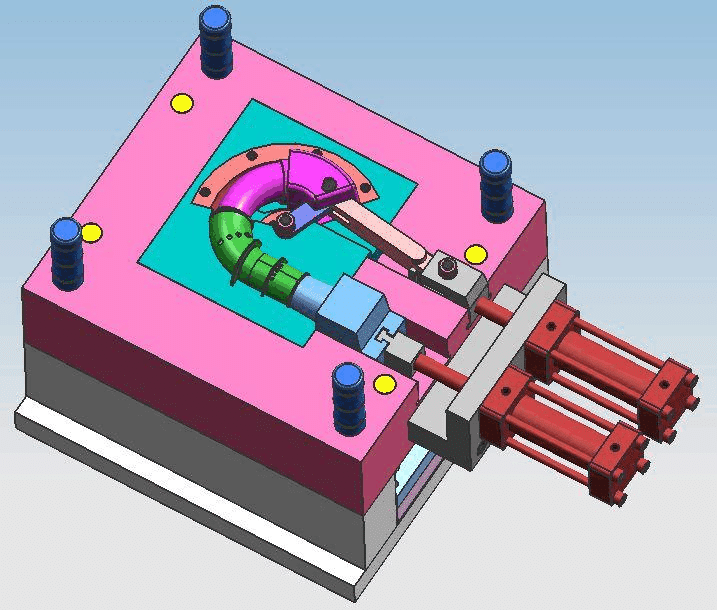
1. What is Short Shot in Injection Molding?
Short shot occurs when the molten plastic material does not completely fill the mold cavity during the injection molding process, resulting in a partially formed or undersized part. This defect can be attributed to a variety of factors, including design flaws, process parameters, material properties, and machine-related issues. It is important to address short shot promptly to ensure the production of high-quality parts and minimize scrap rates.
2. Causes of Short Shot in Injection Molding:
Several factors contribute to short shot occurrences in injection molding. Here are the most popular opinions regarding its causes:
- Insufficient Injection Pressure: Inadequate injection pressure can impede the complete filling of the mold cavity. Insufficient pressure may arise due to low hydraulic pressure, an undersized injection unit, or restrictions in the flow path. This can result in the molten plastic material not reaching all areas of the mold, leading to a short shot.
- Inadequate Material Flow: Poor material flow due to inadequate melt temperature, high viscosity, or improper gate design can restrict the flow of plastic into the mold cavity. Insufficient material flow may cause premature solidification, preventing the complete filling of the cavity and resulting in a short shot.
- Improper Venting: Inadequate venting in the mold can trap air or gases, preventing proper material flow and resulting in incomplete filling. Insufficient venting may lead to air pockets or trapped gas that displaces the molten plastic, causing a short shot defect.
- Insufficient Injection Time: Inadequate injection time may occur when the injection speed or duration is not optimized for the specific part and mold design. If the injection time is too short, the material may not have enough time to completely fill the mold cavity, leading to a short shot.
- Material Properties: The properties of the plastic material used in injection molding can also contribute to short shot defects. Factors such as material viscosity, melt temperature, and thermal stability can affect the flow characteristics and ability to completely fill the mold cavity.
3. Fixing Short Shot in Injection Molding:
Addressing short shot in injection molding requires a systematic approach and careful analysis. Here are effective solutions and best practices to fix short shot issues:
- Optimization of Injection Parameters: Review and optimize injection parameters, including injection pressure, melt temperature, injection speed, and hold time. Conducting mold flow analysis and adjusting the parameters accordingly can help ensure complete cavity filling.
- Gate Design and Placement: Evaluate the gate design and placement in the mold. Optimal gate size, shape, and location can improve material flow and prevent premature solidification, reducing the likelihood of short shot defects.
- Mold Venting: Ensure proper mold venting to allow trapped air or gases to escape during the injection process. Adequate venting prevents air pockets and allows for proper material flow, minimizing the risk of short shot defects.
- Material Selection and Processing: Choose plastic materials with suitable viscosity and flow characteristics for the specific part and mold design. Conduct material testing and analysis to determine the optimal processing conditions that promote complete cavity filling and reduce the occurrence of short shot defects.
- Mold Design and Maintenance: Review the mold design to ensure it facilitates proper material flow and complete cavity filling. Regular maintenance and cleaning of molds are crucial to prevent any obstructions or contamination that can lead to short shot defects.
- Process Monitoring and Control: Implement robust process monitoring and control systems to detect and address short shot issues in real-time. Utilize sensors, monitoring software, and quality control measures to ensure consistent and reliable production.
4. Best Practices to Minimize Short Shot:
Prevention is key to minimizing short shot defects. Implement the following best practices to reduce the occurrence of short shot in injection molding:
- Thorough Design Analysis: Perform a comprehensive design analysis to identify any potential issues related to material flow, gate design, or mold venting. Address these concerns during the design stage to minimize the risk of short shot defects.
- Mold Flow Simulation: Utilize advanced mold flow simulation software to simulate and optimize the filling process. This enables the identification of potential short shot areas and assists in making informed design and process decisions.
- Process Validation and Testing: Conduct thorough process validation and testing, including mold trials and sampling, to ensure that the chosen process parameters and material properties are suitable for achieving complete cavity filling and minimizing short shot defects.
- Continuous Process Improvement: Adopt a culture of continuous improvement by analyzing production data, conducting root cause analysis, and implementing corrective actions to prevent short shot defects from recurring.
Short shot defects can pose significant challenges in the injection molding process, leading to substandard parts, increased scrap rates, and compromised product quality. Understanding the causes of short shot and implementing effective solutions and best practices are crucial for fixing and preventing this issue. By optimizing injection parameters, addressing design flaws, ensuring proper mold venting, and practicing continuous improvement, manufacturers can minimize short shot defects, enhance production efficiency, and deliver high-quality plastic parts.