In the production of injection molding parts, plastic part design plays a significant role, inappropriate design often causes defects in plastic molded parts. In this article, we are going to explore how plastic part design affects the product appearance quality, and how to improve the appearance quality by optimizing the design.
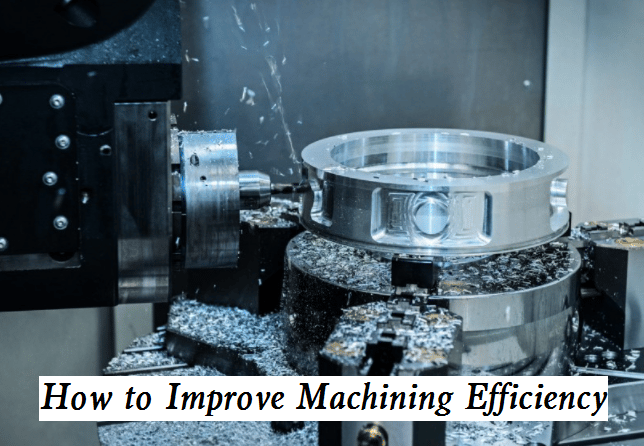
How to Improve Appearance Quality of Plastic Injection Molded Parts by Optimizing Design
Improve sink marks in plastic part design
Sink marks usually occur at the positions corresponding to the ribs and supports of the plastic parts. The reason for such sink marks is that the wall thickness of these parts increases and the plastic shrinkage becomes larger. In order to reduce this shrinkage, the thickness of the ribs should be controlled between 0.5 and 0.7 times the wall thickness of the plastic parts. Too thin or too thick is not appropriate. Too thin has a limited reinforcement effect; Too thick, the bottom of the rib is easy to produce sink marks during the forming process.
Sink marks are also affected by mold gate design, material type, and process. The farther away from the gate, the greater the possibility of surface shrinkage. The textured design of the mold cavity can cover up some defects of the plastic parts, but it is difficult to ensure the surface quality at the locations of the plastic part ribs, supports, and sudden changes in wall thickness. Some flexible plastic part design schemes can reduce the surface sink marks, such as opening grooves or designing ripples at the corresponding parts of the plastic part ribs. Gas-assisted molding can significantly reduce the surface shrinkage of plastic parts, but the problem of color difference is inevitable. When the thin wall plastic part is far away from the gate, if the gate size is too small, it will cause obvious sink defects of the plastic part.
Improve weld lines in plastic part design
During injection molding, the front edges of the material flow converge to form a weld line, which is another surface defect of the plastic part. The gate needs to be designed at the non-key part of the plastic part, so as to reduce the impact of the weld line on the quality of the plastic part. Mold flow analysis is useful for predicting gate settings. Reasonable exhaust design outside the fusion line area can help reduce the fusion line, but in most cases, the fusion line cannot be completely eliminated.
Improve air traps in plastic part design
During the injection process, if the external exhaust of the plastic part is not smooth, or the material flow around the plastic part is filled before the material flow near the gate, gas will be generated. When trapped gas is generated, the plastic will be burnt due to the Diesel effect. This can be avoided by moderately increasing the wall thickness of the plastic part between the gate and the trap point. The blind rib parts processed by EDM will also generate trapped air, which will make it difficult to fill the reinforcing rib, and the material will also overheat. In this case, exhaust must be used, such as adding an ejector pin, breathable insert, or other exhaust structures.
When the wall thickness of the plastic part changes suddenly, the surface of the plastic part is prone to air trapping. The molten plastic flow loses contact with the mold cavity locally. With the increase of injection pressure, a certain amount of air accumulates between the plastic and the mold cavity wall. This air will be rapidly compressed, causing the temperature to rise, thereby reducing the surface quality of the plastic part. This situation will lead to poor adhesion or impact resistance of the plastic part surface.
Improve bubbles in plastic part design
Bubble problem generally exists in transparent material injection, such as PC parts. It is often caused by excessive shrinkage of the thick wall of the plastic part. To solve the bubble problem, it is necessary to avoid designing structural features with relatively large wall thicknesses on plastic parts. If it is really unavoidable due to the functional needs of the product, the mold design needs to deliberately use a large gate and set sufficient pressure holding time in the injection process. Inadequate drying of materials and insufficient back pressure and holding pressure are also easy to cause bubbles.
Improve streaks in plastic part design
The possible causes of surface streaks of plastic parts include moisture in plastic raw materials, aging of injection molding machine barrel, aging of mold hot runner, or excessive shearing during material flow. From the perspective of plastic part design, the too small gate will lead to excessive shearing of materials. Mold flow sharing is helpful to determine the reasonable material shear rate.
Improve delamination in plastic part design
When the adhesive force between the solidified surface layer and the molten inner layer of the plastic part is insufficient, material delamination will occur, which is caused by high material temperature or too fast an injection speed. If the delamination cannot be improved by reducing the injection speed and adjusting the melting conditions, the material shear rate can be reduced by improving the gating system and using large-size gates and runners.
Improve jetting in plastic part design
When molten plastic directly enters the open mold cavity through a small gate, it is easy to produce a jet. The plastic expands after passing through the gate and cools rapidly, forming a wavy strip of cold material in the mold cavity. Then, the cavity pressure rises, and the rest of the cavity is normally filled. The initially formed cold material leaves visible wavy lines on the plastic part, which will affect the mechanical properties of the plastic part. In order to avoid jetting defects, the gate position shall be designed to ensure that the molten plastic can quickly fit with the mold cavity after passing through the gate.