After the plastic part is ejected from the injection mold, we need to use the correct method to test the plastic part to ensure that it can meet the design and application requirements. What methods are used to inspect the quality of injection molded parts in the plastic injection molding industry?
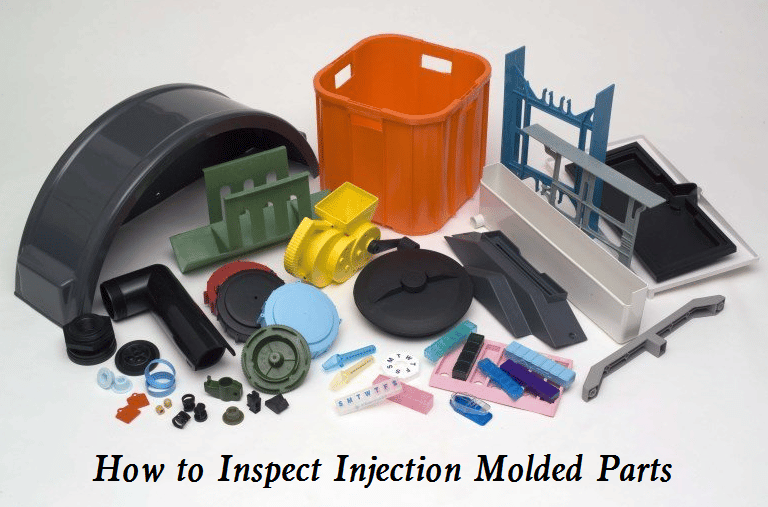
How to Inspect Injection Molded Parts – 5 Quality Check Methods in Plastic Injection Molding
Visual check
In addition to general visual inspection, sometimes enhanced visual inspection methods are also used, such as a microscope or industrial CT to detect suspected defective products. Visual inspection is mainly strengthened by means of adjustable light, high-power light, and amplification detection. Visual inspection also often uses different light sources to achieve different test results. The commonly used light sources include ultraviolet light, fluorescent light, incandescent light, halogen light, sodium gas light, LED light, and black light. In short, different light types can be used for different detection purposes. For example, the use of black light can improve the brightness of product pollutants in some cases, so as to detect defective products.
Dimensional measurement
After the injection molding product is ejected from the mold, due to the characteristics of the plastic product itself, the product often has problems such as shrinkage, warpage, and distortion. Therefore, the detection of such defects has become a key issue to ensure product quality.
Due to the characteristics of plastics and the limitations of the injection molding process, these three kinds of problems will always occur with the project. Therefore, appropriate methods are needed to ensure the dimensional stability of the final product. The commonly used detection methods include the image measurement method, in mold pressure detection method, and size measurement method. It should be noted that when we want to measure the key dimensions of a product, we generally need to follow the following three principles, which are: at least 30-60 minutes apart (some materials may have longer intervals) before measuring the dimensions, measure the dimension after annealing. In some cases, it is necessary to measure the dimension under the application condition of simulated products
Polarizer test
Polarizers are generally used to detect the internal stress of transparent components, such as PC plastics. Through the detection of internal stress, we can understand the risks of post deformation, cracking, and warpage of products. However, the internal stress problem can not be known through simple visual inspection or size measurement. At present, the polarizer detection method is the most effective detection method.
The polarizer testing method can help us determine the following three problems: the stress concentration in the product; The crystallinity of plastics; Molecular orientation of plastics. During the test, place the sample on the observation platform. The part with stress is bright white, and the part without stress is black, which is the same as that without the sample. Among them, the positions changed to blue, green, red, and other colors are the concentration areas with more stress. When the stress ratio is large, the stress distribution will not change even if the sample is rotated
Combustion test
When the injection molding part is burned, after the polymer material encounters the flame, the following series of problems will occur according to the difference in material characteristics, which are: fast or slow combustion; Scorched; burned and split; burned and melted; Being burned and dripping; Release odor or smoke; A colored flame is generated.
When the polymer material moves away from the flame, a series of problems will occur according to the difference in material characteristics, which are: fast or slow combustion; Scorched; burned and split; burned and melted; Being burned and dripping; Release odor or smoke; Continue to burn. According to these characteristics, we can understand a series of problems with injection molded parts through combustion tests.
Density test
Density is one of the characteristics of a substance. Every substance has a certain density. The density of different substances is generally different. So we can use density to identify substances. The method is to measure the density of the substance to be measured and compare the measured density with the density of various substances in the density table, so as to identify what substance the object is made of. Water, the most common substance in nature, is often used for density comparison because its density is 1g / cm3, which is very standard. Different plastic properties determine that plastics have different densities Generally speaking, the higher the crystallinity and feeding degree of the injection molded product, the higher the density of the product. Therefore, we can determine the crystallinity and feeding degree of the product during the injection molding process by detecting the density of the injection molded product.