In the realm of engineering and manufacturing, precision is paramount. Whether we’re crafting intricate components for aerospace technology or designing advanced medical devices, the pursuit of perfection begins with accurate measurements. One crucial aspect that demands our attention is the elusive quality known as cylindricity. Defined as the degree to which an object’s surface deviates from a perfect cylinder, cylindricity is a critical characteristic that can make or break the functionality and reliability of mechanical parts. So, if you’re ready to embark on a journey that unveils the mysteries of cylindricity measurement, fasten your seatbelt and prepare to delve into the realm of precision engineering. In this article, we’ll explore the principles, techniques, and tools required to unlock the secrets of measuring cylindricity, empowering you to elevate your manufacturing prowess to new heights.
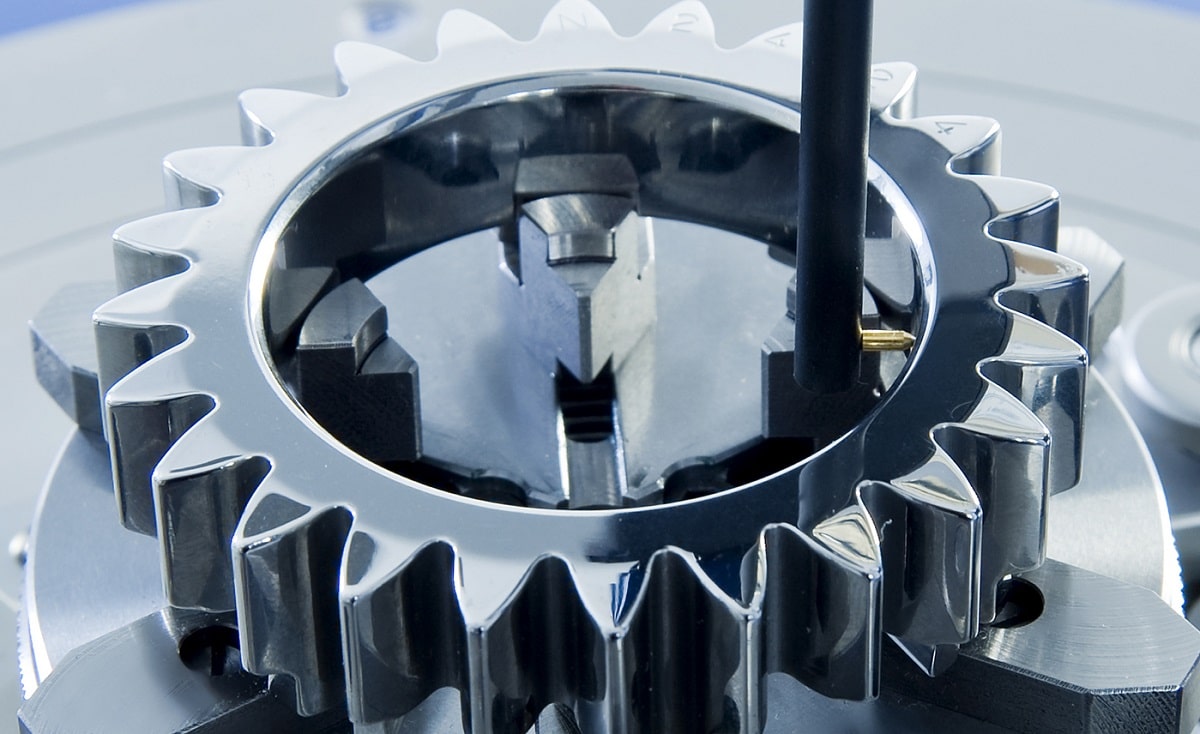
What is Cylindricity?
Before we delve into measurement techniques, it is important to have a clear understanding of what cylindricity entails. Cylindricity defines the three-dimensional tolerance zone around the axis of a cylindrical part, within which the surface must lie. Deviations from perfect cylindricity can occur in the form of out-of-roundness, taper, lobing, and other imperfections. Proper measurement and assessment of cylindricity ensure that a cylindrical part functions optimally within its intended application.
Methods To Measure Cylindricity
Cylindricity is a geometric characteristic used to describe how well a cylinder or cylindrical feature approximates a true cylinder. It is important in various industries, including manufacturing and engineering. Several methods can be used to measure cylindricity, depending on the level of accuracy required and the available equipment. Here are some commonly used methods:
Contact-Based Measurement Techniques
1. Micrometer Measurements:
Micrometers are widely used for measuring cylindricity. These handheld devices utilize a spindle and anvil to measure the diameter at various points along the length of the cylinder. By comparing these measurements, the operator can assess the cylindricity by evaluating deviations from a perfect cylinder.
2. Dial Indicator Method:
Dial indicators are another common tool for measuring cylindricity. This method involves mounting the cylinder on a rotating device and using a dial indicator to measure radial displacements at multiple points. By plotting the measured values, the operator can assess the cylindricity profile of the cylinder.
3. Three-Axis Coordinate Measuring Machine (CMM):
CMMs equipped with a probe attachment can be employed to measure cylindricity accurately. The probe traces the surface of the cylinder, capturing data points at regular intervals. The acquired data is then analyzed to determine cylindricity deviations.
Non-Contact-Based Measurement Techniques
1. Laser Scanning:
Laser scanning techniques have revolutionized the field of cylindricity measurement. A laser scanner projects a laser beam onto the cylinder’s surface, while a camera system captures the reflected light. The acquired data is processed using specialized software to generate a three-dimensional point cloud, allowing for a detailed analysis of cylindricity deviations.
2. Optical Profilometry:
Optical profilometers use light interference patterns to measure surface topography, making them suitable for cylindricity measurement. By scanning the cylinder’s surface with a focused light source, the instrument can calculate deviations from the ideal cylinder shape based on interference patterns generated by reflected light.
How to Measure Cylindricity with CMM?
Cylindricity is a geometric tolerance that describes how closely the surface of a cylindrical object approximates a perfect cylinder. It is typically measured using specialized metrology equipment. Here’s a general overview of the process for measuring cylindricity:
- 1. Obtain the necessary equipment: You will need a coordinate measuring machine (CMM) or a roundness measuring machine capable of measuring cylindricity. These machines are designed to precisely measure the form of cylindrical objects.
- 2. Prepare the cylindrical object: Ensure that the surface of the object is clean and free from any contaminants that could affect the measurement. If necessary, secure the object properly to prevent any movement during measurement.
- 3. Set up the measurement equipment: Calibrate and set up the measuring machine according to the manufacturer’s instructions. This may involve setting the appropriate measurement parameters and aligning the object correctly.
- 4. Define the measurement path: Specify the measurement path or scan path that the machine will follow while measuring the cylindricity. This path should cover the entire length or surface of the cylinder.
- 5. Start the measurement: Activate the measurement process on the machine. The machine will move along the defined path, collecting data points at regular intervals. It will measure the deviations of the actual surface from a perfect cylinder.
- 6. Analyze the data: Once the measurement is complete, the machine will generate a data set representing the deviations from the perfect cylinder. Analyze the data using specialized software provided with the measuring machine.
- 7. Determine cylindricity tolerance: Compare the measured data against the specified cylindricity tolerance. Cylindricity tolerance is typically specified as a maximum allowed deviation from a perfect cylinder, usually expressed in micrometers (μm) or inches (in).
- 8. Interpret the results: The analysis software will provide a graphical representation of the measured data, showing the deviations from the ideal cylinder shape. Review the results to determine if the cylindricity falls within the specified tolerance range.
It’s important to note that the specific steps and procedures may vary depending on the type of measuring machine used and the software provided by the manufacturer. It is always recommended to consult the equipment’s user manual or seek expert advice for accurate measurements.
How To Calculate Cylindricity?
Calculating cylindricity involves measuring the deviation of a surface from a perfect cylinder. The following steps outline a basic method for calculating cylindricity:
- 1. Obtain a cylindrical part: Start with the object you want to measure, such as a manufactured component or a precision-machined part. Ensure that it has a cylindrical shape.
- 2. Choose a measuring instrument: Select an appropriate measuring instrument capable of capturing the necessary data. Common tools used for cylindricity measurement include coordinate measuring machines (CMMs), roundness testers, profilometers, or optical comparators.
- 3. Establish a measurement reference: Determine a reference axis for the cylindrical part. This axis represents the ideal or nominal cylindrical shape against which deviations will be measured. It should be aligned with the axis of the part, ensuring that it remains consistent throughout the measurement process.
- 4. Capture data points: Using the selected measuring instrument, capture a series of data points along the surface of the cylindrical part. These points should be evenly distributed around the circumference and span the entire length of the part. The number of data points will depend on the level of precision required.
- 5. Analyze the data: Once the data points are collected, analyze them to calculate the cylindricity. There are different methods and algorithms available for this purpose, depending on the measuring instrument used. Common techniques include fitting a best-fit circle to the data points or performing Fourier analysis to evaluate the harmonic components.
- 6. Calculate the deviation: Compare each data point to the reference axis or nominal cylinder to determine its deviation. The deviation is the distance between the data point and the reference axis at a specific location.
- 7. Determine the cylindricity tolerance: Establish the allowable tolerance for cylindricity based on the requirements of the part or component. This tolerance represents the acceptable deviation from a perfect cylinder and is usually specified in engineering drawings or standards.
- 8. Evaluate the cylindricity: Compare the calculated deviations against the specified tolerance. If the deviations fall within the allowed limits, the part meets the required cylindricity. Otherwise, adjustments or further refinements may be necessary.
Remember that the specific measurement techniques, instruments, and algorithms used can vary depending on the equipment available and the level of precision required. It’s always advisable to consult relevant standards, guidelines, or industry best practices for accurate and consistent cylindricity measurement.
Measuring cylindricity is a crucial aspect of quality control and precision engineering. Accurate assessment of cylindricity deviations helps ensure optimal performance and functionality of cylindrical parts in various industries. Whether using contact-based methods like micrometers and dial indicators or non-contact-based techniques such as laser scanning and optical profilometry, choosing the appropriate measurement method depends on factors such as accuracy requirements, complexity of the part, and available resources. By adhering to standards, understanding measurement uncertainty, and leveraging technological advancements, engineers and manufacturers can achieve higher levels of precision in cylindricity measurement and enhance the overall quality of their cylindrical components.