The expression “burrs” that is commonly used in metal processing sites such as pressing and cutting may not be understood by people who are not involved. Therefore, on this page, we will explain what burr is and why it occurs. We will also introduce the challenges of measuring burr as a quality inspection and how to solve them.
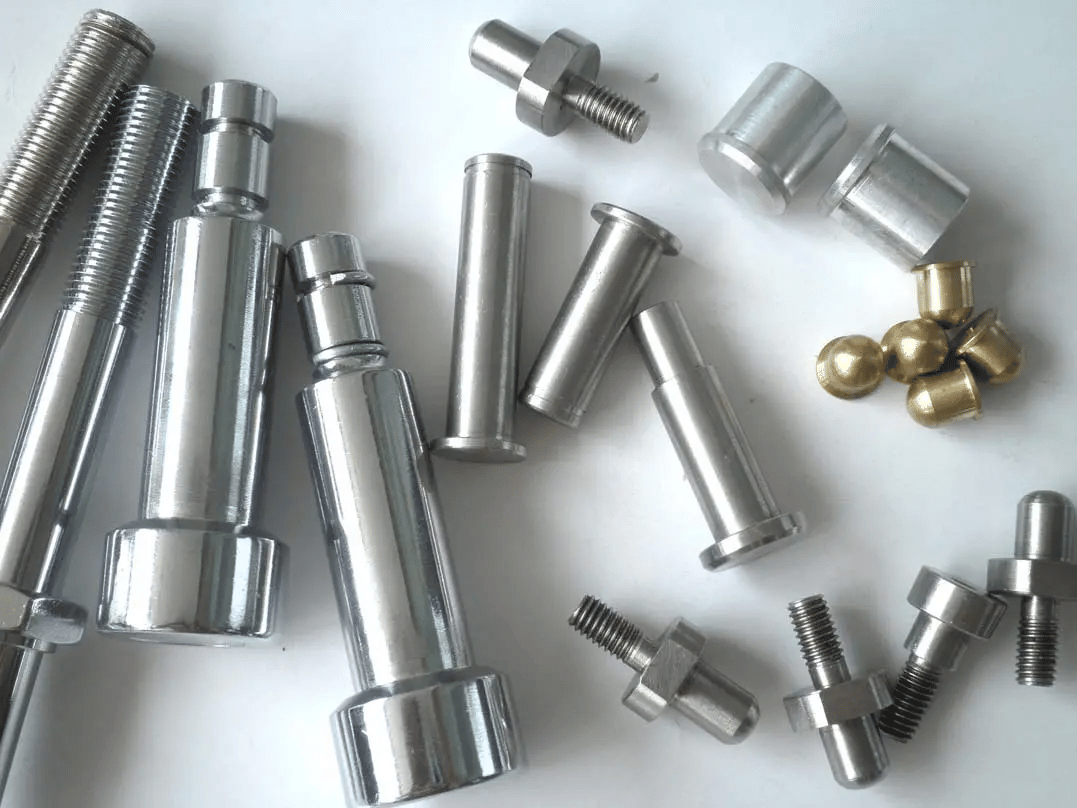
What Is Burr?
Burr is a metal ledge that occurs on the cut surface in shearing and drilling by pressing. It is also commonly defined as “the outer residue of a geometric shape at the edge of the shape and the residue on the part during the machining or molding process”.
If the buur remains, touching it with your hands will cause injury. They may not be able to be combined or joined accurately. In order to avoid such troubles, it is ideal to remove them by polishing. However, if it cannot be removed, it is necessary to indicate to the drawing the good side on which maple may occur.
The size of the burr is expressed by the “height of the burr” and the “thickness of the base of the burr”.
What is No Burr?
It is often seen in drawing instructions, but there is no clear standard for its height and size. burrs are always better off without, but chamfering all edges increases man-hours and costs.
Types and Classification Of Burrs in CNC Machined Products
In addition to machining such as drilling and cutting, Burr occurs in various processing methods such as casting, forging, and resin molding. The types of burrs can be classified according to the processing method, and each has its own causes.
Cutting and Grinding Burrs
- Processing method – Machining (turning, milling, drilling, grinding)
- Cause – When chips were formed, part of the material flowed plastically.
Shear Burrs
- Processing method – Plastic forming (shearing, pressing)
- Cause – In the clearance between the die and punch, part of the material flowed plastically.
Cast Burr / Resin molding Burr
- Processing method – Casting and resin molding
- Cause – A part of the material plastically flowed on the mating surface of the mold or mold.
Plastic deformation burrs
- Processing method – Forging and rolling
- Cause – Flashlands and gattas of molds made some of the material plastically flowing.
Conventional Burr Measurement of CNC Parts and Products
If a stamped part has a flounder outside the tolerance range, there is a possibility that a mating failure or welding failure during joining may occur when the part is attached, or a failure due to a connection failure may occur due to a slight load during use. Measuring and inspecting the cut surface of a stamped part can lead to the quality of the part itself, the quality during assembly, and even its reliability in the market after shipment.
Conventionally, measurements of pressure burr were performed with contour shape measuring machines. However, there were the following challenges.
Issues of Burr Measurement with Contour Shape Measuring Machine
A contour measuring machine is a device that measures and records the contour shape of an object by tracing the surface of an object using a stylus. In recent years, there have been models that use lasers instead of stylus to trace contours without contact to measure complex shapes. In addition, some models can measure both the upper and lower sides. In a contour profilometer, it is necessary to take an accurate measuring line for the shape of the Burr you want to measure.
Therefore, there were the following issues:
- It takes time to fix the sample to the jig and level it. In addition, knowledge and skills related to contour measuring machines are essential for accurate leveling.
- The stylus of the contour profilometer moves arcs up and down around the fulcrum on the stylus arm, and the position of the stylus tip also moves in the X direction, so errors also occur in the X-axis data.
- It is very difficult to pass the needle as intended, and subtle needle misalignment can cause variations in measured values.
- Since it is necessary to aim and measure at a specific part, it is difficult to increase N.
- Since only a part of the measurement value can be taken, it is not possible to evaluate it in terms of aspects.
3D Scanning Can Detect Burrs In Parts & Products Quickly And Accurately
Dramatically improving and improving the efficiency of shape measurement of Burr, which is difficult to measure.
High-speed 3D scanning enables instantaneous measurement of the exact 3D shape of an object without contact. Difficult measurements such as the height and position of Kaeli can be completed in as little as 1 second. All the problems of conventional measuring machines can be cleared.
- Since it measures by surface, it is easy to measure a large area. Don’t miss even the slightest burr, and you can make a detailed evaluation. Since the measurement time is also short, it is easy to increase N to N.
- It eliminates variations in measured values by humans and realizes quantitative measurements.
- Without positioning, simple operation is realized by simply placing an object on the stage and pressing a button. Eliminate individualization of measurement work.
- Since 3D shapes can be measured easily, at high speed, and with high accuracy, it is possible to measure many objects in a short time, which can be useful for quality improvement.
In addition, since it is possible to easily analyze comparisons with past 3D shape data and CAD data, distribution within tolerance ranges, etc., it can be used for various applications such as product development and manufacturing trend analysis and sampling inspection.