As the name implies, industrial measuring equipment is instrument that measures products correctly. It can be said to be an important tool for maintaining the quality of products.
“I was assigned to the quality inspection department, but I don’t know what kind of industrial measuring equipment it is”; “I want to know in advance what to pay attention to when measuring.” If you are asking these questions, we will introduce the features of industrial measuring equipment, their types, and common troubles. Please use it as a reference to hold down the basics of industrial measuring devices.
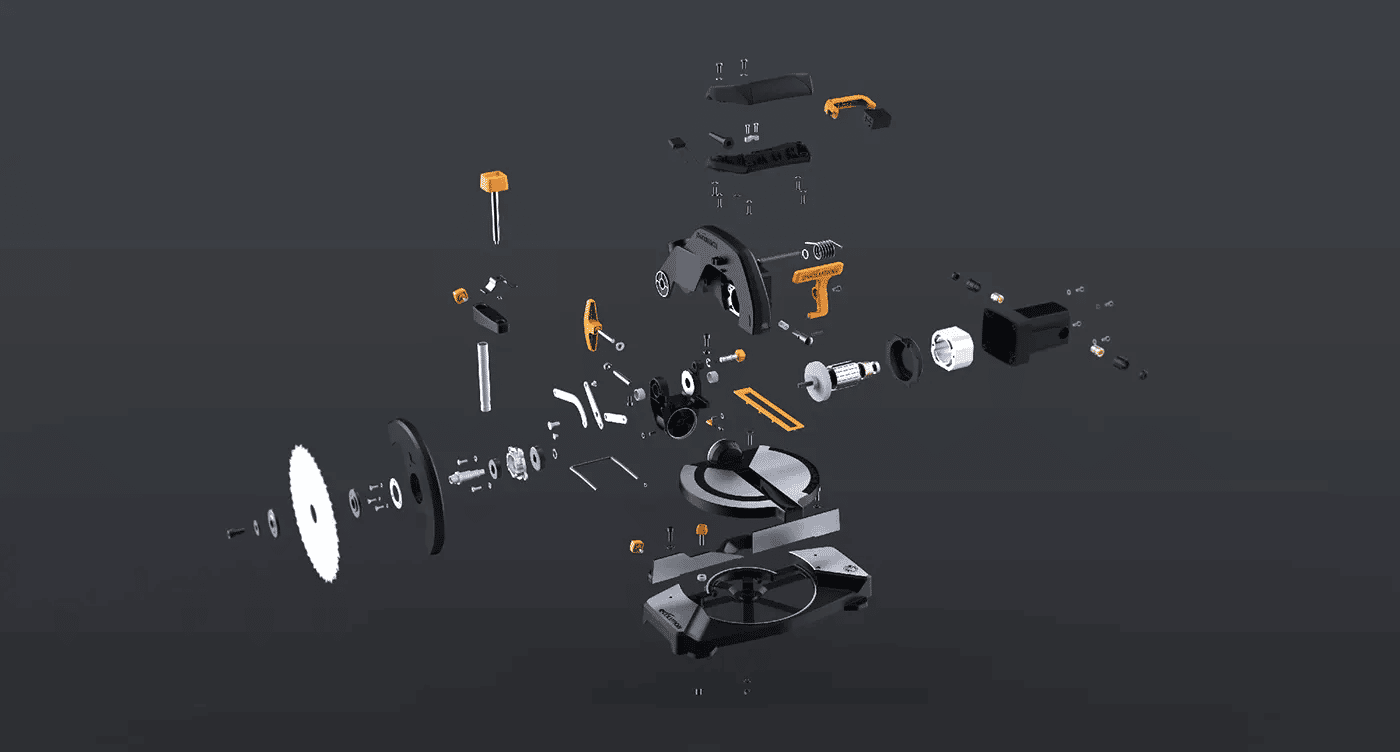
1. What is Industrial Measuring Instrument?
An industrial measuring instrument is a measuring instrument used to ensure that a product is as designed. Scales that measure length and mass meters that measure weight are commonly used, but industrial uses differ in that they can measure to more detailed values and in terms of accuracy.
For example, on a general scale (such as a ruler), the smallest unit is 1 mm, but on industrial scales (calipers and micrometers), the unit display is up to the minimum unit of 0.001 mm, and it is possible to measure as much as 1/1000 in detail.
2. Features Of Industrial Measuring Equipment
We would like to list four representative features of industrial measuring equipment:
(1) High measurement accuracy
One of the characteristics of industrial measuring instruments is their high measurement accuracy. In industrial applications, it is designed to match the range and accuracy required, and even the same measuring instrument must be selected according to the application. For example, in order to improve measurement accuracy, a spindle is used to finely tune the feed volume in the axial direction, so that the minimum unit is several microns
(2) Periodic calibration is required
Industrial measuring instruments need to not only measure, but also guarantee the measurement results. Therefore, by performing regular calibration, maintenance is performed in a state where correct measurement can be performed. In addition, since the measurement value of the measuring instrument shifts little by little with daily use, it is necessary to calibrate periodically from this viewpoint as well.
(3) There are various measuring devices that are not generally used
Rulers and measures are common for measuring length, but for industrial use, there are various types of calipers, micrometers, dial gauges, height gauges, etc. just for measuring length. Since there are various measurement sites, there are equipment that is suitable for the application. There are various devices that are not used by the general public, and the difference between industrial use and general use is that there are devices that can reach the itchy place at the time of measurement.
(4) It is necessary to use it in the correct measurement environment
The last characteristic of industrial measuring equipment is the need for an appropriate measurement environment. Appropriate temperature and humidity control is required, especially in measurement environments. The reason for making the temperature appropriate is that since the measuring instrument is made of metal, the length of the measuring instrument itself may change due to the temperature, and the measurement result may change. Therefore, it is necessary to keep the temperature constant when handling the measuring instrument.
The reason for proper humidity is to prevent rust and corrosion of the measuring instrument. Rust on the edges of the measuring instrument may cause the measurement results to shift, or it may be damaged due to internal rust or corrosion.
3. Types of Industrial Measuring Equipment
Next, we will introduce specific examples of industrial measuring equipment according to the parameters to be measured.
(1) Dimensional measurement
Even if the dimensional measurement is performed, there are various measuring instruments because the part and state differ depending on the measurement target. Representative items are introduced in the table below.
Measurement scene | Typical measurement equipment |
Measuring the total length of a hard object | Nogisu, dial gauge |
Measuring the thickness of soft objects | Dial gauge |
Measure diameter | Cylinder gauge / ring gauge |
Measure height | Height gauge |
Measuring depth | Depth gauge |
Measure the gap | Thickness gauge |
① Nogisu
Measurement is performed by sandwiching the measurement target between the two plates at the tip. It is generally used to measure while holding it in your hand.
② Micrometer
Measurement is performed by sandwiching the measurement target between the two shafts at the tip. The micrometer is generally used by fixing it to a pedestal for measurement.
③ Dial gauge
Measurement is performed by sandwiching the measurement target with the stylus at the tip (dial thickness gauge). It is used for measuring soft products such as rubber because it can be measured under a certain measurement pressure. It is also frequently used, such as by rotating the workpiece with the stylus pressed against it on a lathe, etc., to check the circumferential touch.
④ Cylinder gauge / ring gauge
Adjust the 0 point of the cylinder gauge with a ring gauge with the same inner diameter as the measurement target, and measure the amount of deviation of the inner diameter of the measurement target with the cylinder gauge. It is used for measuring the inner diameter of cylinder blocks that require high-precision measurement.
⑤ Height gauge
Place both the measurement target and the height gauge on the platen and measure the height of the measurement target from the standard. You can also use the dial gauge as a stylus and slide the height gauge on the platen to measure.
⑥ Depth gauge
The depth is measured by touching the reference plane of the depth gauge to the measurement target and hitting the scale to the depth.
⑦ Feeler gauge
Measure by inserting it into the gap you want to measure. Gauges with multiple thicknesses are usually set as a set, and the measured value is determined by distinguishing between gauges that can be inserted and gauges that cannot be inserted.
(2) Hardness Measurement
Industrial measuring instruments include measuring instruments that measure the hardness of a product. The hardness of a product is often treated as a substitute for mechanical strength, and is often described in drawings as a design requirement.
Generally, measurements are made using a measuring device called a hardness tester. It can be used depending on the material and shape to be measured.
Type of hardness test | Usage example |
Rockwell hardness (Hr) | Used to measure the hardness of metal after heat treatment |
Vickers hardness (Hv) | Used when measuring the hardness distribution of thin and small parts. |
Brinel hardness (Hb) | Used to measure the hardness of coarse and non-uniform metal such as cast products. |
Shore hardness (Hs) | Used for measuring the hardness of large metal parts that are difficult to bring into the inspection room. |
Noup hardness | Used when measuring the hardness of brittle materials. |
(3) Pressure measurement
There are many industrial measuring instruments that not only measure the product itself, but also measure its characteristics, etc., and one of them is a pressure gauge. There are various types of pressure gauges, from pressure gauges for monitoring the pressure in factory piping to pressure sensors for measuring pressure in test cells.
(4) Torque Measurement
In addition to simple measurements, there are also devices that can perform measurements at the same time as assembly. One of them is a torque gauge. With a torque gauge, you can measure the fastening torque while fastening bolts and nuts.
It is used to guarantee the fastening torque described in the drawing in the assembly process, and to check whether or not the fastening force is reduced during the overhaul survey.
4. Common Troubles And Countermeasures For Industrial Measuring Equipment
We would like to explain three common problems and how to deal with them when using industrial measuring equipment.
(1) Misalignment of measured values due to inappropriate calibration frequency
A common problem is that the measurement value is misaligned due to the inappropriateness of the configuration frequency of the in-house measuring equipment. There are many cases where such a case is noticed later, and a backlog occurs to check retrospectively from which timing the measurement deviation occurred. In order to prevent this from happening, it is necessary to firmly determine the calibration frequency of the measuring instrument.
(2) Measurement value deviation due to inappropriate room temperature
In some cases, the product expands or contracts thermal depending on the temperature, and the measurement result is shifted. In particular, for products with tolerances of several microns such as sliding parts, the rate of change due to room temperature is large. For example, there are cases where the results of a measurement of parts issued from an overseas factory differ when measured by Japan. In such a case, although both factories had measuring rooms, there were factors such as the measurement results being misaligned due to the difference in the measuring room temperature between Japan and overseas. In order to prevent this from happening, it is necessary to keep the room temperature of the measurement environment constant and to unify the philosophy within the company.
(3) Damage due to contact with the work
When handling measuring instruments, it is common to have troubles that come into contact with the workpiece and cause damage such as deformation of the measuring unit.
For example, when measuring with a measurement device with a thin tip such as a point micrometer, there are troubles such as turning the dial while looking at the digital display, and the tip is deformed.
In order to prevent such troubles from occurring, it is necessary to standardize measurement work and create work procedures that are less likely to cause problems.