Injection molding is a common manufacturing process used to produce parts and products from plastic and other materials. It involves injecting molten material into a mold cavity where it cools and hardens into the final part shape.
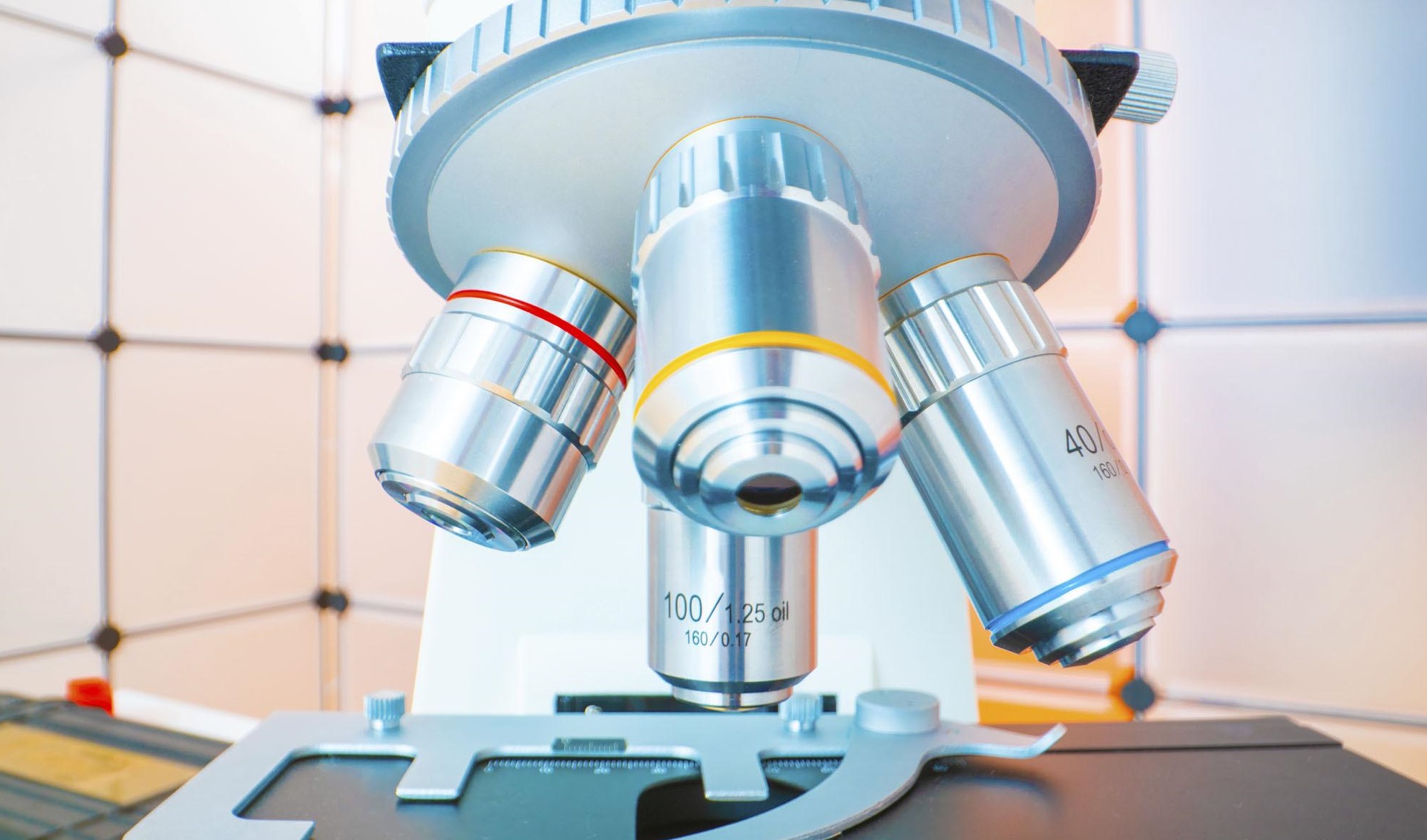
First article inspection (FAI) is an important quality control process conducted on the first piece produced during an injection molding production run. It verifies that the part meets all engineering, design and specification requirements before full production begins. Performing a thorough FAI helps ensure the injection molding process is capable of producing good parts consistently.
What is a First Article Inspection?
A first article inspection is a complete, documented physical and functional inspection performed on the first production sample of a new part or product. It follows an approved procedure and uses the actual engineering drawings and specifications as guidance.
The purpose is to verify that the component conforms fully to all engineering, specification, drawing, process, and contract requirements. This ensures the production process and tooling are capable of manufacturing parts that meet the design expectations.
First article inspections are commonly required:
- – When production starts on a new part number
- – When changes are made to the design, specifications, material, tooling, or production process
- – At specified intervals during the production life, such as annually
- – When production resumes after a long lapse
- – When production moves to a different facility
Performing thorough FAI is critical because it validates the production process before committing to full ramp-up. If problems or non-conformances are identified on the first article, they can be addressed and corrected prior to continuing production. This minimizes waste, rework, and potential impact to customers further down the supply chain.
What is Inspected During a First Article?
The first article inspection evaluates all attributes on the part print and applicable specifications. This includes:
- – Dimensional tolerances – size, lengths, hole position, surface finish, etc.
- – Material and mechanical properties – chemistry, hardness, tensile, melt flow index, etc.
- – Visual appearance – color, defects, flaws, burrs, etc.
- – Functional performance – leak testing, load testing, electrical, etc.
- – Marking and identification – part number, material, date code, etc.
- – Completeness – ensuring all specified features are present
Every dimension, note, specification, and tolerance should be inspected on the first part to verify conformance. The extent of testing depends on the complexity of the component and its end-use application. Simple parts may only require basic dimensional checks, while complex assemblies may need extensive functional testing.
FAI Inspection Tools and Equipment
A wide range of inspection tools, gauges, and instruments may be used to perform first article inspections:
- – Calipers, micrometers, pins, blocks – for dimensional measurements
- – Hardness testers, melt indexers – for material properties
- – Tensile, compression testers – for mechanical properties
- – Vision systems, microscopes – for visual examination
- – Leak, pressure testers – for functional verification
- – CMMs (coordinate measuring machines) – for high precision automated inspection
- – Profile projectors, optical comparators – for 2D part features
- – 3D scanners – for complex freeform shapes
The specific equipment used depends on the component geometry, tolerances, and inspection plan requirements. Custom gauges and fixtures are often designed for first article inspection of critical parts and assemblies.
Using programmable CMMs
and optical scanners to gather 3D point data enables complete digital analysis of the entire part vs. the CAD model. This automates the process and provides a permanent record of the initial part condition.
First Article Inspection Report
The results of the complete first article inspection must be documented in a First Article Inspection Report (FAIR). This report details the actual values measured for each inspected characteristic on the first part relative to the drawing or specification limits.
A simple FAIR lists every feature in the order presented on the print, including:
- – Feature name / characteristic number
- – Nominal dimension / specification target value
- – Tolerance range (upper and lower limit)
- – Actual measured value
- – Pass / fail indication
More detailed reports may also show the measurement method, equipment used, and any specific notes or abnormalities observed. The first article piece should be uniquely identified and retained as part of the FAIR documentation.
Photos are also commonly included to show the overall part condition and any noted defects. The complete first article package provides evidence that all features have been fully verified. This documentation can be quite extensive for parts with tight tolerances and many critical characteristics.
Approving the First Article
The first article inspection report must be reviewed and approved internally before production continues. Any out-of-tolerance dimensions or non-conforming conditions must be addressed. Common responses include:
- – Adjusting process settings to bring critical dimensions back in spec
- – Modifying tooling and equipment to improve first article results
- – Reworking or scrapping the first piece if defects cannot be corrected
- – Requesting an engineering change to widen the tolerance range if capable
- – Complete first article re-inspection after adjustments are made
Once all characteristics meet drawing requirements, the first article FAIR is signed-off by quality and manufacturing groups to formally approve part production. The approved report provides evidence of first article acceptance and becomes part of the permanent quality record.
Benefits of Performing Thorough First Article Inspections
While first article inspections require time and diligence upfront, they deliver significant benefits:
- – Verifies all part features meet design specifications before production ramp-up
- – Catches non-conformances early when relatively few parts are impacted
- – Ensures critical dimensions and functions are proven acceptable
- – Allows process adjustments before high volume production
- – Reduces downstream manufacturing issues and escapes
- – Provides a baseline record of initial production quality
- – Meets customer requirements and industry standards for quality
- – Avoids costly rework, scrap, and troubleshooting during production
- – Reduces product launch delays and speed time-to-market
By thoroughly validating all design and specification requirements on first part production, manufacturers can have high confidence in the injection molding process before committing to full-scale manufacturing.
First Article Inspections for Injection Molded Parts
Injection molding produces highly repeatable parts suitable for automated inspection. The first article process generally includes:
Preparation
- – Review all component drawings, models, specifications
- – Have all inspection equipment available and calibrated
- – Make sure proper material is used for first article parts
- – Program CMMs or automated inspection routines if used
Inspection
- – Visually examine part for flaws, completeness of features
- – Take dimensional measurements for all toleranced features
- – Perform hardness, melt flow, density checks per spec
- – Conduct appearance and functional tests if required
- – Verify all markings and identification details
Documentation
- – Record all measurements on the FAIR form vs. the print limits
- – Take images of part showing key features and overall condition
- – Note any defects or anomalies observed
- – Save CMM or automated inspection datasets
Review
- – Compare all results to print and specifications
- – Identify any out-of-spec measurements or nonconformances
- – Determine if adjustments or rework are required
- – Obtain approvals to continue with production
For plastic injection molding, the first article inspection focuses heavily on dimensional accuracy and visual appearance. Critical functional attributes and material tests may also be required depending on application requirements.
While first article inspections offer great value for new molding projects, their usefulness continues well after launch through continuous improvement initiatives.
Periodic first article re-validation helps ensure production quality is maintained over time. Measurement trends can be compared to initial results to identify dimensional drift or process deterioration. New inspection techniques can also uncover additional insights during these reviews.
First article data provides a benchmark to drive ongoing quality monitoring and process improvements. Optimizing the molding process and tool maintenance based on FAIR findings helps maintain peak performance and integrity as programs mature.