Inspecting complex shaped parts for defects is a challenging task, especially when the geometry of the part makes it difficult to access all surfaces. Traditional inspection methods can be time-consuming and prone to human error. In this article, we will explore how machine vision systems can be deployed to inspect complex shaped objects holistically, covering all 360 degrees of the surface.
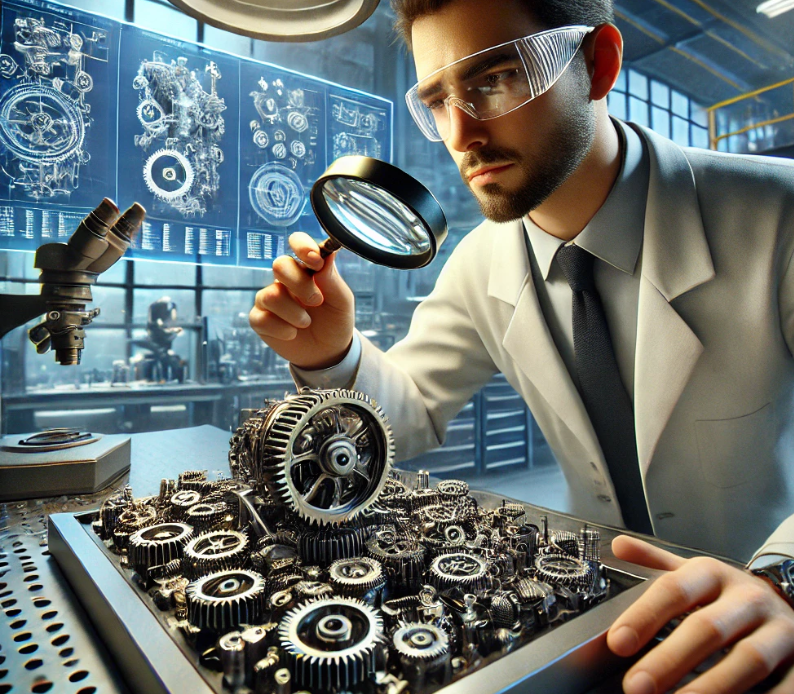
Common Challenges in Inspecting Complex Parts
Inspecting complex parts presents several common challenges, including hard-to-reach features, maintaining precision across scales, material property challenges, and data management and interpretation. These challenges require the use of specialized equipment and innovative methods, such as advanced imaging technologies and robotic systems, to ensure that all areas can be effectively inspected. Additionally, inspectors need to balance macro and micro perspectives to ensure that every detail complies with specifications. The properties of different materials can pose challenges to traditional inspection methods, necessitating the development of customized inspection solutions. Furthermore, the vast amount of data generated by high-resolution inspections needs to be effectively managed and interpreted to convert into actionable insights, supporting decision-making and continuous improvement of the manufacturing process.
Challenges of Complexity in Modern Manufacturing
Characteristic | Description | Example Challenges |
---|---|---|
Complex Geometric Shapes | Parts with irregular shapes, multi-axis features, and microscopic details. | – Inspecting internal cavities and deep holes – Capturing and analyzing microscopic details |
High Precision Requirements | Tolerances measured at the micrometer or even sub-micrometer level. | – Ensuring dimensional accuracy within tight tolerances – Detecting and measuring micro-defects |
Special Materials | Metals, composite materials, and ceramics pose unique challenges to detection. | – Titanium alloys causing interference in traditional detection methods – Carbon fiber composites requiring specialized inspection techniques |
Strict Standards | Must comply with industry and regulatory requirements such as ISO, ASME, or FDA. | – Adhering to ISO standards for dimensional accuracy – Meeting FDA requirements for medical device manufacturing |
Can a Machine Vision System be Deployed to Inspect Complex Shape Objects?
When it comes to inspecting complex geometries, the first question that arises is whether a machine vision system can be effectively deployed. The answer is yes, but it requires careful planning and design. The key is to ensure that the entire surface of the part can be inspected, which often involves moving the part in front of the camera or deploying multiple cameras to cover all angles. This is a crucial step before any image processing can take place.
Camera Inspecting Entire Surfaces
For a complex object, such as a tap, there are surfaces around the part and surfaces within, such as near the faucet. To inspect these areas, you need to decide how to practically move the part in front of the camera or deploy multiple cameras. This ensures that all aspects and angles are covered. In most cases, the image acquisition process is more complex than the image processing itself. Therefore, either the camera needs to be deployed along with a robotic arm to move in front of the part and capture all angles, or the part itself needs to be designed to move in front of the camera using some kind of motorized or automated movement.
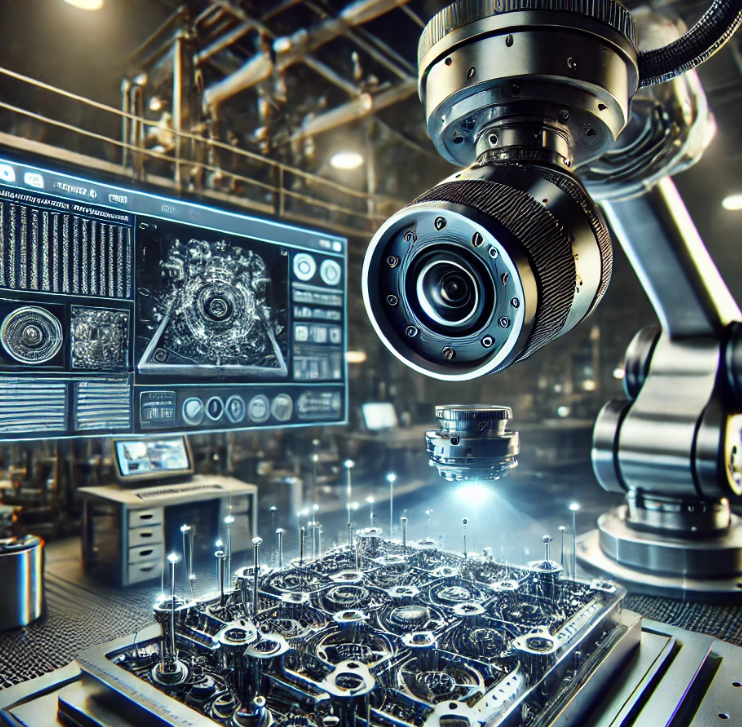
Image Acquisition is More Complex than Image Processing
When designing a machine vision system for complex geometries, the primary consideration is how to physically and practically image the part. In most cases, the complexity lies in the image acquisition process rather than the image processing. Once the image acquisition problem is solved, the entire solution process becomes much easier. This involves ensuring that the camera can capture all necessary angles and surfaces of the part, either by moving the camera or the part itself. Once this precondition is met, deploying software to process the captured images becomes a more straightforward task.
Why Choose IPQCCO for Complex Part Inspection?
Inspecting complex parts requires a combination of advanced technology, specialized expertise, and a commitment to excellence. At IPQCCO, we bring all these elements together to ensure the highest standards in complex part inspection. Here are the key reasons why you should choose IPQCCO for complex parts inspecting service:
1. Cutting-Edge Technology
We invest in the latest inspection tools to tackle a wide range of challenges:
Coordinate Measuring Machines (CMM): Our CMMs are designed for three-dimensional measurements, providing precise dimensional analysis for even the most complex parts.
Non-Destructive Testing (NDT): We use ultrasonic testing, X-ray, and computed tomography (CT) scans to inspect internal features without causing any damage to the parts.
Optical and Laser Scanning: High-resolution 3D imaging technologies capture the surface details of complex geometric parts with astonishing precision.
2. Customized Inspection Strategies
We understand that each part is unique, and our inspection strategies are tailored to the following factors:
Part Geometry: We select the most appropriate tools and techniques to fit the specific design of the part.
Material Properties: We adjust our methods to accommodate unique material characteristics.
Application Requirements: We ensure compliance with relevant standards and tolerance requirements.
3. Professional Technical Team
Technology alone is not enough. Our trained inspection team combines technical expertise with a keen eye for detail. Through regular training, they stay up-to-date with the latest inspection methods and industry trends.
4. Integrated Quality System
Our inspection processes are part of a broader quality management system. We use advanced software for data collection, analysis, and reporting, ensuring transparency and traceability for every inspected part.
Case Study of Complex Aerospace Parts Inspection on IPQCCO
Huayu Aviation Technology Co., Ltd. focuses on the design and manufacturing of aerospace components, and has recently developed a complex part with multiple internal channels, with a tolerance requirement of ± 0.005 millimeters. The customer is seeking us to conduct a comprehensive inspection of the part to ensure its quality and reliability. We have had detailed communication with the client to understand their needs and potential risks.
Testing Plan
CT scan preparation: After receiving the parts, we conduct a preliminary inspection to ensure that there is no external damage.
CT scan execution: Use CT technology to generate high-resolution 3D images and analyze internal structures.
Data analysis: A minor defect that may affect flight performance has been identified, which has not been recognized by traditional methods.
Solution and subsequent testing
We communicated with the customer and proposed a correction suggestion, suggesting reprocessing the parts. After reprocessing, we conducted another inspection and confirmed that the defects had been eliminated and the dimensions met the requirements.
Results and Feedback
Huayu Aviation Technology Co., Ltd. has successfully obtained qualified certification, avoiding potential flight performance issues and expressing high satisfaction with our technology and services. This case demonstrates the professional capabilities of cq-smart.com in the inspection of complex aerospace parts.
The Benefits of Collaborating with IPQCCO for Testing Services
- Reduce the risk of malfunctions: Early detection of defects can prevent costly recalls and liability issues.
- Enhancing customer trust: Providing reliable high-quality parts can strengthen customer relationships.
- Improve operational efficiency: Reliable testing reduces rework and production delays.
- Compliance and Market Access: Accurate testing ensures compliance with strict industry standards and smooth entry into the market.