To ensure product quality, it is necessary to strengthen the quality control of the production process. Quality control is the operational techniques and activities undertaken to achieve quality requirements. Its purpose is to ensure product quality by monitoring the process and eliminating factors that lead to dissatisfaction in all stages of the quality loop.
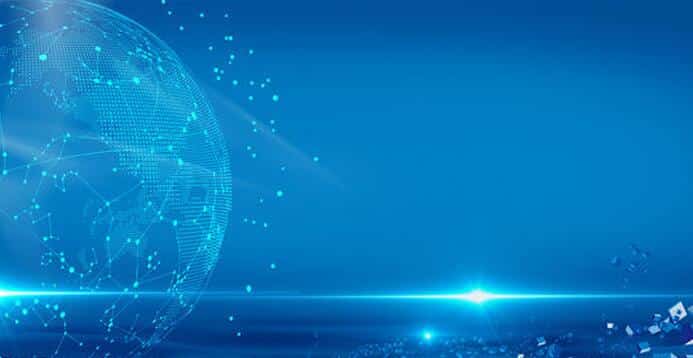
The quality of both component products and final products can be described by how much the quality characteristics fluctuate around the design target values. The lower the fluctuation, the higher the quality level. The highest level of quality is achieved when every quality characteristic value reaches the design target, i.e., the fluctuation is zero. But in practice, this is never possible. Therefore, we must carry out quality control of the production process to minimize fluctuations. Most of the world’s successful enterprises are mostly inseparable from strict production process quality control. The D1-9000 quality document of Boeing and the SPC control chart technology of Japan are documents about production process control technology. Ford Motor Company in the United States has a very strict quality specification system suitable for its own reality. This quality specification system basically operates in accordance with the quality operation procedures of QS 9000 (which includes ISO 9000). These system documents cover all aspects and processes of quality management, covering the entire product formation process, and specify and detail the work to be done in each process, as well as how to record various quality data. This not only ensures the quality of the product but also provides a lot of technical material for future quality improvement. In order to ensure and evaluate the implementation of quality standards, Ford conducts internal quality audits twice a year and formulates corrective measures for the problems detected by the audits, corrects them by the deadline, and strictly carries out follow-up inspections and controls.
Main Procedures Of Quality Monitoring In The Production Process
1. Oversee the factory to create a sound system for assigning tasks, create or amend the operating procedures as needed, adhere to the production discipline, and firmly follow them.
2. Maintain proper production order, equip the workstations with appropriate equipment, and oversee the efficient operation of the production channels. promoting environmental sustainability to reduce dust and pollution. Boost site management and actively apply “6S” management (organization, tidying, cleaning, cleanliness, quality, safety).
3. Oversee the factory’s completion of the necessary pre-production activities and arrange the production operation plan sensibly.
4. Organize factory maintenance tasks and maintain the technical integrity of the equipment by supervising the factory. The level of quality that the restored equipment must meet. To upgrade the tools of the trade, guaranteeing the precision of the work, cards, measurements, and cutting instruments.
5. Manage the quality of your resources and suppliers well. strictly inspect all arriving items before accepting them. Materials that are unqualified or in violation of the contract should be returned or rejected. To guard against damage and deterioration, make the storage of resources stronger. Boost service quality and supply on time. When the material department buys and sells the products, the material department is ultimately accountable for the quality of the materials.
6. Use the system documents to supervise and check the quality activities and try to count all kinds of information. Non-conforming factors (non-conformity refers to non-conforming requirements, divided into non-conforming products and non-conforming items) will always be found more or less, the important thing is what is the nature of the non-conforming factors found. If it is a general non-conformity, it has little impact on the quality of the final product, this non-conformity is relatively easy to correct; if it is a serious or systematic non-conformity, it is important to pay great attention to, because it will affect the normal operation of the system, so that the final product defects or scrap. Therefore, the quality system is set up to supervise and inspect the quality activities, so that the non-conforming factors can be cleared out in time, and the reasons for them can be identified, and the corresponding corrective and preventive measures can be actively adopted to solve the non-conforming factors completely in order to prevent the recurrence. When a nonconformity is found, it is necessary to control it, and it is required to analyze the causes, to learn from the past, to prevent the same problem from occurring again, which is the corrective measures. On the basis of the development of corrective measures, the factors that may lead to such non-conformity (human, machine, material, law, environment) to specify the constraints (system documents, standards, etc.) to ensure that the fluctuations of these factors do not exceed the scope of the constraints, which is the basic content of the prevention of non-conformity. Corrective and preventive measures are followed up and checked, and closed-loop zeroing management is implemented, so that the quality of the production process can be improved. Even so, some factors will fluctuate, and it is impossible to recognize the causes of fluctuations comprehensively and accurately at one time, which requires constant identification of the causes in the process monitoring, finding one, eliminating one, so that fluctuations are constantly approaching the goal of zero.
7. Supervise the factory to improve the quality of packaging. To develop packaging standards according to the characteristics of the product, packaging and inspection in strict accordance with the standards, the product packaging must be reworked. To continuously improve the product decoration, to achieve beautiful and generous.
8. Supervise the factory to conduct regular internal quality audits. Audit the establishment and implementation of the quality system, audit the continuity and effectiveness of the quality system. Identify non-conformities and audit the development and implementation of corrective measures.
Some Problems That Cannot Be Neglected in the Quality Control of Production Process
1. Pay attention to the enthusiasm of people. Quality control of the production process requires everyone to be a monitor, which places high demands on the quality and motivation of employees. Therefore, to create a good atmosphere, the implementation of the “cohesion” project, to truly “respect people, understand people, care about people”, mobilize the enthusiasm of people, creativity, development of human resources. In particular, enterprise leaders should strive to adhere to the people-oriented, training staff “everyone is a talent” thinking, to create for each person, to show their own opportunities to make them realize that in the production process, they are experts in the process or parts, each of their mistakes may bring unqualified results to the product, so that the company suffered losses . Sincerely do practical things for the staff, solve difficulties, strengthen quality awareness, enhance the sense of urgency and crisis of the enterprise staff; adhere to the “quality to win” quality management strategy, determine the correct quality concept, values, create a good quality environment, enhance corporate cohesion, combat power, and create the conditions for the implementation of total quality management.
2. Emphasize the technical training of employees. Comprehensive promotion of quality education, training and improve the quality of staff awareness and quality management skills, through various forms of education and training to create a work of employees who are not used to seeing poor quality and low efficiency; create an atmosphere where employees feel satisfied and self-fulfillment for self-improvement, so that the quality of the production process monitoring not only quality personnel become a consciousness. Cultivate quality personnel, improve the quality of the team, not only to make employees have quality awareness and master the technology of quality control. In foreign countries, some industrially developed countries have built quality management institutes, enterprises set up quality president or quality manager, the country has a quality award, these practices, we can learn from.
ISO 9004-2 standard in the “incentive” clause states: “to encourage employees to contribute to the improvement of quality by giving appreciation and rewards for achievements. ” In order to make quality improvement a conscious action of enterprise workers, we must rely on the role of a perfect quality incentive mechanism. If the reward and punishment system can effectively link quality with salary, quality with bonus, quality with technical title, administrative position promotion, etc., it can fully mobilize the enthusiasm of management, technical and operation personnel in the process monitoring to ensure the quality of products.