In precision parts manufacturing, quality control (QC) is essential to ensure products meet exact specifications, maintain safety, and uphold industry standards. In fields like aerospace, automotive, and medical devices, even a minor flaw can result in costly consequences. This blog delves into essential quality control techniques and tools used in parts inspection, with insights on current trends that help manufacturers achieve flawless results.
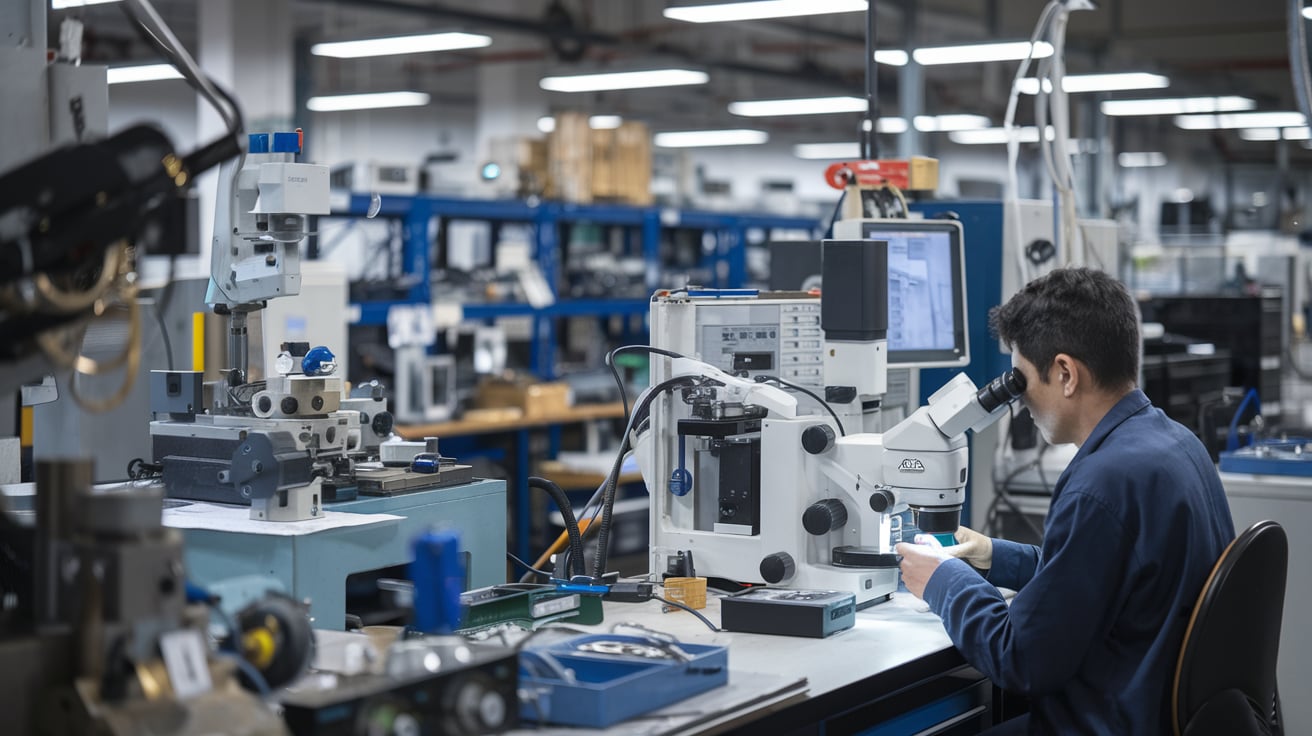
1. Importance of Quality Control in Precision Parts Manufacturing
For manufacturers, QC is not merely a compliance activity but a guarantee of part integrity. High precision parts require exact tolerances, as errors can impact performance, safety, and lifespan. Effective QC reduces rework, minimizes recalls, and enhances customer satisfaction, making it a cornerstone of quality assurance strategies.
Common QC objectives in precision parts inspection include:
· Ensuring parts adhere to specified tolerances and dimensional accuracy
· Verifying material integrity and surface finishes
· Detecting defects that may affect functionality, such as microcracks or uneven surfaces
· Documenting and reporting inspection results for traceability and audits
2. Key Techniques in Quality Control
Precision inspection techniques have evolved to detect ever-smaller deviations and imperfections, enhancing part reliability and reducing waste. Here are some critical methods used across industries:
Coordinate Measuring Machine (CMM) Inspection
CMMs are widely used for parts requiring high accuracy. By using probes, they map part dimensions and geometries against digital models, offering micron-level accuracy.
· Applications: Common in aerospace, automotive, and tooling.
· Advantages: Capable of measuring complex shapes and features with high precision.
· Limitations: CMMs can be time-consuming and are typically less effective for very high-speed production lines.
Optical Inspection and Vision Systems
Optical inspection uses cameras, lasers, and sensors to assess part dimensions, contours, and surface quality. It is fast and suitable for non-contact inspection, ideal for delicate parts or surfaces.
· Applications: Electronics, medical devices, and consumer goods.
· Advantages: High speed and versatility; effective for surface defect detection.
· Limitations: Limited effectiveness with parts that lack defined surface contrast.
X-Ray and CT Scanning
X-ray and computed tomography (CT) provide a non-destructive way to inspect internal structures. They allow inspectors to see through solid parts, making them valuable for detecting internal voids, porosity, or hidden defects.
· Applications: Critical for parts in medical, aerospace, and automotive industries.
· Advantages: Non-destructive internal inspection, capable of detecting sub-surface flaws.
· Limitations: High equipment costs and longer inspection times than surface-level methods.
Ultrasonic Testing
Ultrasonic testing uses high-frequency sound waves to detect subsurface flaws or variations in material density. It is especially effective for weld inspection, bonding verification, and checking material uniformity.
· Applications: Common in aerospace, structural engineering, and heavy machinery.
· Advantages: Non-destructive and precise for detecting internal flaws.
· Limitations: Requires skilled operators and may have limitations with certain material thicknesses.
3. Advanced QC Tools for Precision Parts Inspection
The range of inspection tools available today reflects advancements in technology, each suited to specific QC requirements:
Laser Scanners
Laser scanners offer quick and accurate surface inspection, making them ideal for assessing part geometries and surface conditions in three dimensions.
· Advantage: High-resolution 3D scans for detailed shape and surface assessments.
· Use: Commonly integrated with CMMs or used as standalone systems.
Digital Microscopes
Digital microscopes provide magnified views of small or detailed parts, helping to identify surface-level defects, burrs, or tiny cracks that may impact performance.
· Advantage: High magnification without contact, preserving surface integrity.
· Use: Suitable for medical components, electronics, and miniature parts.
Surface Roughness Testers
Surface finish impacts performance and durability in many parts, particularly those with frictional components. Roughness testers evaluate surface profiles and ensure they meet specifications.
· Advantage: Quantitative assessment of surface texture.
· Use: Vital for gears, seals, bearings, and other friction-sensitive components.
4. Modern Trends in Parts Inspection
To keep pace with increasing industry demands for precision and efficiency, parts inspection has undergone significant changes. Several trends are shaping QC in today’s manufacturing landscape:
Automated Inspection Systems
Automation minimizes human error and enables high-speed inspection. Integrating automated systems with robotics and conveyors allows manufacturers to perform real-time QC on the production line, increasing throughput.
· Example: Automated optical inspection systems use machine learning to identify deviations faster and with higher accuracy than manual inspection.
Data-Driven QC with Digital Twins
Digital twin technology pairs real-time data with digital models of parts, enabling predictive maintenance and quality tracking. QC processes can identify issues before they escalate, optimizing production and quality control efforts.
AI and Machine Learning in Defect Detection
Artificial intelligence (AI) and machine learning (ML) are increasingly used for defect detection. By analyzing images and sensor data, AI systems can detect anomalies more effectively, learning to improve their accuracy over time.
Portable and On-Site Inspection Solutions
Portable QC tools allow inspectors to conduct quality checks on-site rather than in dedicated labs. Handheld scanners, portable CMMs, and ultrasonic devices enable rapid checks without moving parts from the production line.
5. Challenges in Precision Parts Quality Control
While advanced QC tools and techniques offer great benefits, there are challenges to consider:
· Cost and Investment: Advanced QC equipment like CT scanners and automated systems require significant investment. Small manufacturers may find it difficult to balance QC costs with production budgets.
· Skilled Workforce: With the increasing complexity of QC tools, manufacturers need trained operators and inspectors with technical skills, which can be a barrier.
· Data Management: Modern QC generates vast amounts of data, which requires proper storage, analysis, and integration with production systems for effective usage.
Precision parts inspection is an essential component of quality control in modern manufacturing. By selecting the right QC techniques and keeping up with the latest trends, manufacturers can ensure consistent, high-quality output, which is critical in today’s competitive landscape. Advanced inspection tools and techniques continue to evolve, promising improved accuracy, efficiency, and quality across industries. Investing in the right QC approach not only improves product reliability but also enhances reputation, customer satisfaction, and competitiveness in the marketplace.