To prevent any negative impact on subsequent production quality caused by design changes, process adjustments, unplanned line stops, production changes, and line transfers, it is necessary to conduct a first article inspection during the job preparation verification and post-production verification phases. However, there are some common misunderstandings and areas for improvement when it comes to first article inspection.
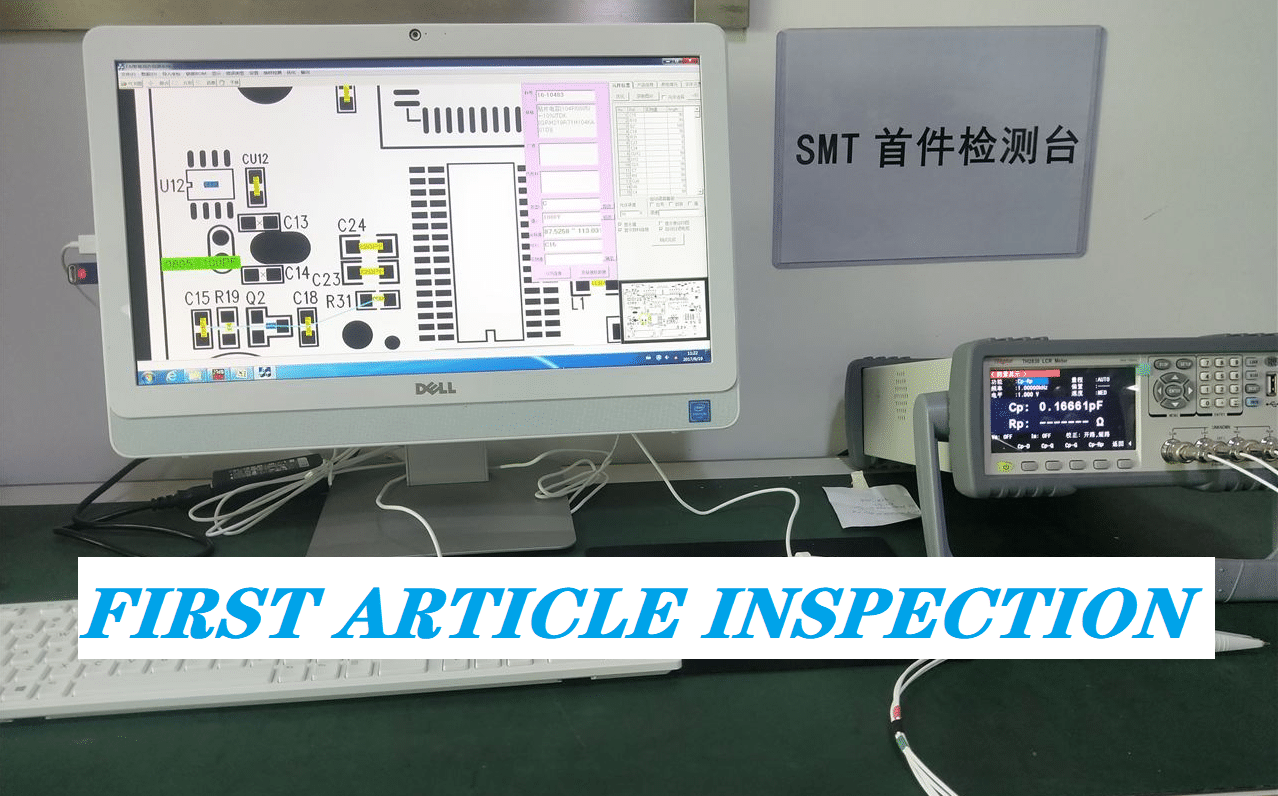
One common misunderstanding is that first article inspection is only necessary for new products or major changes. In reality, it should be conducted for every production run, as even small changes can have a significant impact on product quality.
Another issue is that some companies view first article inspection as a one-time activity, rather than an ongoing process. It’s important to conduct regular inspections throughout the production process to ensure consistency and prevent defects.
Additionally, some companies may rely too heavily on the first article inspection and not take other quality control measures. It’s important to use a combination of quality inspections, testing, and process controls to ensure product quality.
To improve the effectiveness of first article inspection, companies can invest in automation and digital technologies to streamline the process, reduce errors, and increase efficiency. They can also involve suppliers and customers in the inspection process to ensure that everyone is on the same page regarding quality standards.
First Article Inspection
It is a necessary means in on-site quality control, generally refers to: the inspection of the first or first few products processed at the beginning of each shift or after the process changes (such as personnel changes, material changes and tooling, machine tool adjustments, tooling tool replacement and grinding, etc.). Generally, 3-5 products of continuous production should be inspected, and subsequent products can be processed in batches after passing. Most parts in the automotive industry use this control method, but does the first article inspection we do play a quality control role?
1 – First article inspection failure case
A factory repeatedly appeared left front window control switch lifting glass is not sensitive, after investigation is the factory production of the sliding block height size exceeded the lower limit, the product is factory injection molding products, traced the first inspection record found that the height size 9.8 + 0.5 / -0.03 in the first inspection of 8 mold product data are: 9.78, 9.80, 9.77, 9.80, 9.77, 9.77, 9.79, 9.79, 9.79, the first inspection after the start of production, why are there still defective products?
Let’s take a look at how to do the first article inspection?
The purpose of the first article inspection is to confirm that the process is stable and has the process capability to meet the quality requirements. In layman’s terms, it is to confirm that qualified products can be manufactured stably.
2 – What are the criteria for passing the first article inspection?
Many friends regard the first piece of qualification as a passing standard, if you go back decades, a large number of processes are workers operating general equipment processing, the result of the work mainly depends on the skills of employees. Then the purpose of the first article inspection is to confirm that this process has the ability to produce qualified products, and it is correct to take conformity as an acceptance standard. Time has passed, most of today’s enterprises use automatic equipment, even intelligent equipment for production, the operator is a skilled worker, the work results are very dependent on the operator, then the first article inspection has evolved into a process capability (stability) identification method, the use of qualification as a standard is very inappropriate.
Let’s take a look at a case: out-of-tolerance
A factory machining workshop found that the size of parts was out of specification (requirements: 12 (+0/ – 0.15), measured : 12.01 – 12.02), 106 were inspected, 35 defects, and the failure rate was 42.68%;
Note the distribution of non-conformities, which is 12.01 – 12.02, with 48 pieces. Estimate, where is the approximate size distribution of qualified parts? By the way, it’s probably in the range of 11.98 – 12.00.
The problem arises, the qualified standard is 12 (+0/- 0.15), and the variation range of the processed product is 0.05. Why is it that equipment with such high processing accuracy has nearly 50% defective products?
People who do not understand statistical process control only need to remember that the passing standard of the first piece should be limited to the tolerance band center value of 1/5 – 1/3 to ensure the quality stability of mass production.
Based on the principle of statistical process control, if the process is stable, then 2/3 of the points will fall within the range of 1/3 of the control limit.
Therefore, in order to determine that the process meets the quality requirements, the corresponding size of the first article should be controlled within 1/3 of the center value of the specification limit, so that the estimated process capability is 1.0.
This reasoning is because testing a part is a small probability event, and its results should conform to the distribution of high probability. If the process drift of 1.5 standard deviations is taken into account, the acceptance criterion for the first article should be controlled within 1/5 of the center value of the specification limit.
If everyone agrees with this reasoning, you should adjust your first passing criteria. The control principle is the same in other industries, with one-sided tolerances considering one-sided probability distributions.
3 – When is the first article inspection done?
- Each work shift begins
- Replace the operator
- Replacement or adjustment of equipment, process equipment (including tool change)
Change of technical conditions, process methods and process parameters (such as roughness requirements change, inner hole hinge change to boring, change of tool pass or speed in NC program, etc.)
After the use of new materials or material substitutions (e.g. material changes during processing, etc.)
Replacement or re-testing of bath fluids, etc. (e.g. phosphating, nitriding, etc.)
4 – What should the first article inspection document?
The first thing to do is to record the quality characteristic value of the first article. Secondly, the most important is to record the operating conditions of the first piece of processing, including but not limited to the batch of raw material manufacturers, the actual value of process parameters (not the set value), environmental parameters, mold tool models and so on.
If it is a CNC machine, the processing time can also be recorded, as long as it can be traced back to the conditions of the first piece of processing.
The above records correspond to the quality influencing factors of the first article and the processing of the first article, and if a defect is found in mass production, the operating conditions of the first article and the first article can be compared with the existing thing on the spot, so as to find the cause of the defect.
There may be an embarrassing situation where a defective product occurs, but the operating conditions of the defective product are not much different from the first article.
Congratulations, you have discovered a new cause of quality influence, find a way to identify and control it.
5 – The contradiction between the first article inspection and the production schedule
The first article inspection generally needs to be judged by full-time inspectors, and some even need to be sent to the laboratory, and mass production cannot be carried out before the first article is judged. Of course, your first piece on site is not judged to be in mass production, and I can’t help it.
Imagine a scenario where after the start of production one day, all 10 stations have processed the first piece, but the inspection force is not enough, and the operators are waiting for the results.
There are three ways to resolve this contradiction:
- First, the first article inspection is carried out by the squad leader. Since you use him, you must believe him, but the first piece released by the squad leader must not be transferred to order, and can not be transferred until confirmed by full-time inspection.
- The second is to develop special inspection tools to improve the inspection speed. Note here that the rules for the first special inspection tool are also 1/3-1/5 tolerances.
- The third is to test with alternative characteristics. For example: CNC equipment does not need to be full-size inspection, only need to check the size related to the tool and positioning, shape and position tolerance and other dimensions are guaranteed by the machine and the software itself.
Compared to the previous first article work conditions, if the work conditions are consistent, it can also replace the first article inspection.
Note: First article inspection for engineering changes cannot be used as an alternative method.
Summary
With the application of advanced technology and the advancement of management thinking, the classic inspection methods should also be given new meanings. There are many such nodes in on-site quality management, and I hope that all friends will also start thinking about what inspection criteria need to be improved in today’s digital factory.