Quality Inspection is an important process to ensure quality by evaluating whether the products of manufactured parts and products conform to the specified values. In particular, inspections of appearance, dimensions, and shape can not only prevent the outflow of defective products by determining whether OK or NG is possible but are also useful for identifying the cause and preventing recurrence by obtaining detailed information on defects and defects and conditions.
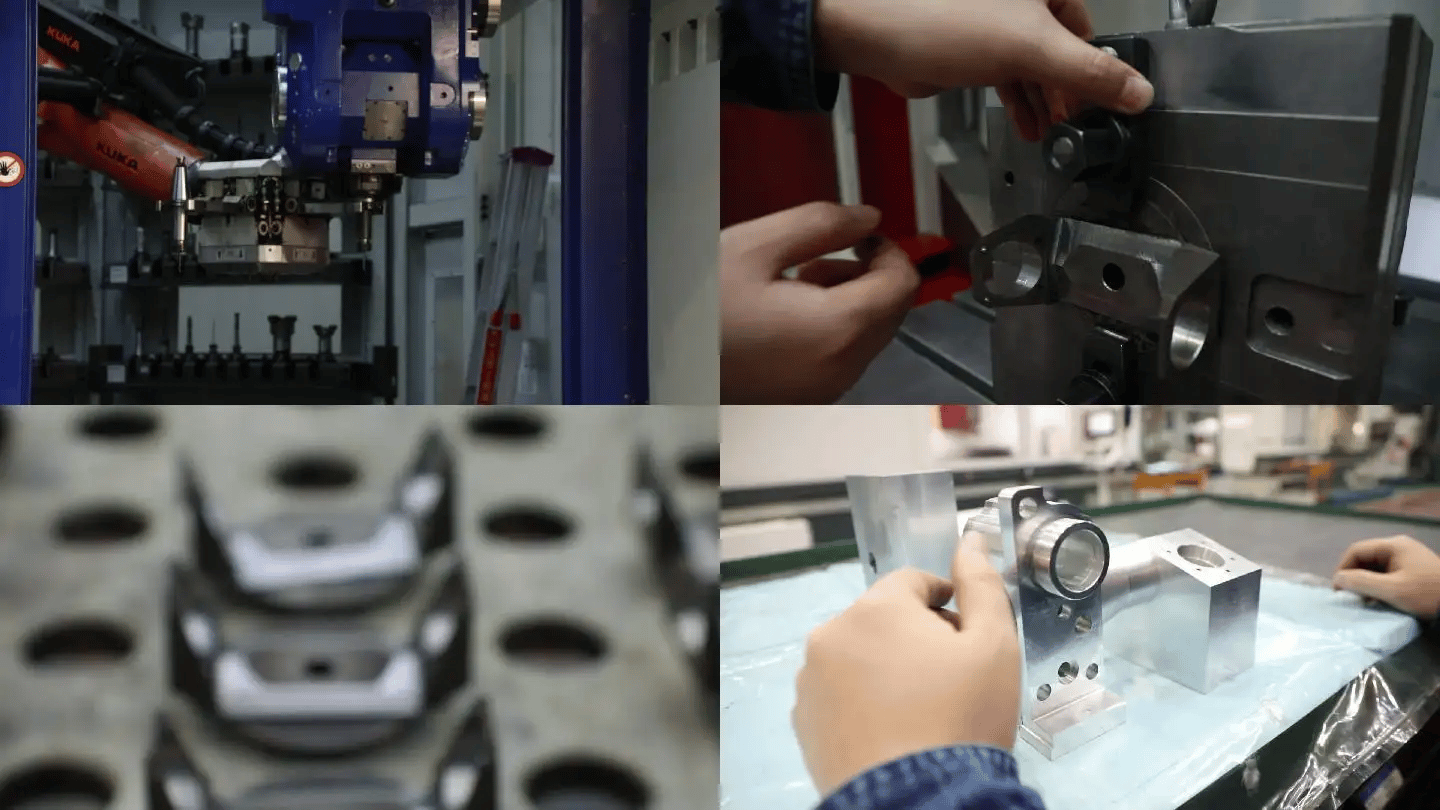
In addition, in the case of products consisting of multiple parts, it is possible to prevent the outflow of defective products by inspecting all of them during the assembly process. For example, the state of adhesion and welding, the process quality of electronic components, and the mounting condition of electronic substrates greatly affect the quality and performance of post-processes and finished products.
How To Conduct The Inspection For Parts & What To Do?
The inspection can be broadly divided into the following two methods:
Sampling Inspection
Multiple samples are extracted from the lot to be inspected, inspected, and the pass or fail of the lot is judged from the results.
Challenges of Sampling
While it is possible to reduce the labor, time, and cost of inspection, even if the extracted sample is a good product, there is a possibility that defective products will be mixed in the lot. At the same time, even if the majority of the lots are good, there is a possibility that the entire lot will be NG because the sample was defective, resulting in loss.
Total Inspection
Inspect all manufactured products or parts, etc. The biggest advantage is that it prevents the outflow of defective products and ensures the quality of all parts and products in the lot.
Challenges Of Total Inspection
While total inspection is ideal, depending on the inspection method and the number of objects, there are many cases where the inspection time and cost do not match the takt time and unit price of the product. In addition, there are many cases where conventional inspection equipment does not provide the ability to respond to the required inspection items, accuracy, speed, and stability, and automation and cost reduction of total inspection are not progressing.
Realization Of Accurate And Stable Automatic Total Inspection
In recent years, technological innovations in profile measuring instruments, 3D displacement meters, 3D cameras, lighting systems, and 3D image processing using new technologies and measurement principles have made it possible to automatically inspect all units of all units that acquire 3D information in-line with high accuracy and stability.
In-line 3D inspection not only prevents the outflow of defective products, but also instantly acquires and processes accurate 3D information such as appearance, dimensions, and shape. This enables simultaneous implementation of multiple inspection items, which was previously difficult.
Various Parts Quality Inspection Methods and Their Issues
Currently, various methods such as AOI, AVI equipment, and near-infrared cameras are used in parts manufacturing for inspection. This section explains typical non-destructive testing methods used at manufacturing sites and various issues in inspection.
Sensory Inspection (Visual Inspection, Etc.)
A typical sensory test using the five human senses is a visual inspection performed by an inspector. We also use touch, taste, hearing, and smell to test the product. In many cases, there is no cost for the introduction of special equipment or equipment.
- Labor costs increase in proportion to the number of inspectors and inspection man-hours. Inspection of all mass-produced products is extremely costly.
- It is necessary to secure and train inspection personnel, and experience and proficiency are required.
- Test results vary depending on the inspector.
- There is a limit to the object to be inspected. For example, it is difficult to inspect the smallest parts of precision parts.
- Even skilled people can make human error, making it difficult to make a complete pokayoke.
X-Ray Inspection
Due to the difference in the amount of absorption in the transmission route of X-rays irradiated to an object, it is widely used to inspect internal defects and foreign matter contamination such as food. For FA, dedicated integrated inspection equipment such as AXI equipment is typical.
- Installation, notification, management, and operation in accordance with laws and regulations are required. Generally, a qualified person (such as an X-ray work supervisor) and a controlled area are required.
- Depending on the object, it takes time to image, making it difficult to respond to total inspection.
- If a defect is found after assembly or sealing, the yield will decrease.
- When imaging from one direction in two dimensions, three-dimensional objects need to be imaged from multiple directions, which takes more time.
- Fine peeling and cracks in electronic devices are difficult to detect.
Infrared Inspection
Infrared rays are invisible light between visible light and microwaves and are classified into near, middle, and far infrared rays depending on the wavelength. Infrared rays are emitted from the front or back surface of the object, and the radiated light from the surface is detected by an infrared camera for image processing and judgment. Internal cracks and surface scratches can be detected by changing the number of infrared rays. There are various other types of cameras, such as cameras that capture thermal effects in bands such as near-infrared rays without irradiating light.
- When the object contains parts with different reflective, absorbing, and transmission characteristics of infrared rays, it is difficult to detect anomalies.
- If the object is thick or the thickness is not uniform, it is difficult to detect internal cracks.
- Seeing light irradiation for a long time may harm eye health, so operation management and caution are required.
Ultrasonography
UT (Ultrasonic Testing), it uses the directivity of elastic vibration waves (sound waves) with a high frequency that exceeds the audible range to image and measures the presence or absence of reflected signals (echoes) and the strength of an object. It is possible to inspect internal cavities (voids), peeling, cracks, etc. from the surface of the object.
- Depending on the thickness of the object, the inspection may be difficult.
- When inspecting the atmosphere, it is necessary to contact the probe with the surface of the object because the propagation characteristics are reduced, and the object is limited.
- Due to the large measurement spot, it is difficult to inspect the shape of small parts.
- Not suitable for visual inspection such as scratches and irregularities on the surface of the object.
Overcurrent Flaw Detection
It is called ET (Eddy current testing) and investigates defects in metallic materials from changes in the generated state of eddy currents. A high-frequency voltage is applied to the coil to generate an alternating magnetic field, and an eddy current is generated by placing an object in the magnetic field. When the overcurrent generation state differs due to material, defects, dissimilar metals, shape changes, etc., it is captured as a signal by a detection coil and analyzed. Since it is possible to make quick judgments using only electrical signal processing, it is widely used from automatic flaw detection tests and inspections on production lines to piping inspections in the nuclear field.
- The object is limited to metal.
- Due to the short measurement distance, the inspection conditions are limited.
Contact Inspection (Contact Displacement Meter)
Manual measuring instruments such as calipers and micrometers are typical, but contact displacement sensors are commonly used in-line. By making the contactor touch the object directly, the height, thickness, warpage, etc. are measured from the displacement.
- Since the contactor comes into direct contact, it is difficult to use it on delicate products such as soft materials, food, and electronic components.
- Due to the small measuring surface, the inspection of large objects requires multiple sensors or multiple measurements.
- Grooves smaller than the contactor cannot be measured.
2D Image Inspection (Image Sensors, Area Cameras)
In general, it is a method in which an object is imaged in a rectangular area with a camera and inspected using the image. It is used for general purposes, such as determining the presence or absence of parts and determining whether it is OK or NG based on the contour shape.
- Since it is determined by the amount of reflected light, accurate height measurement is not possible.
- Objects with depth, such as curved surfaces and spheres, are difficult to measure because they are only partially focused.
- Irregular reflection of light, such as uneven metals, makes it difficult to cope with lighting conditions.
- Since it is distinguished by the shade of the image, the appearance defect cannot be stably detected depending on the surface condition of the object.
1D Non-Contact Inspection (Point Laser Displacement Meter)
Conventional one-dimensional laser displacement meters (triangulation, confocal method, etc.) generally irradiate a single point on the surface of an object with a red point laser and measure the height of that point based on the difference from the reflected light.
- Since it is measured at a point, it takes time to move to the stage to measure multiple points.
- In the case of an object with depth, it may be difficult to measure because a blind spot is created by blocking the reflected light.
3D Scanning Inspection – Solving All Inspection Challenges
Until now, in-line inspection has mainly been based on presence/absence discrimination and OK/NG discrimination, and there have been many cases where sampling inspections have been performed offline for items that require high accuracy. But with these methods, there are some disadvantages such as increased inspection process and costs, risk of outflow of defective products, difficulty to identify and analyze the cause of defects, and decrease in yield rate due to time lag with manufacturing, so there were various challenges involved. In recent years, in-line total inspection using 3D information has been attracting attention as a means of solving these problems.
- Cost reduction through automation
- Prevention of outflow of defective products by total inspection
- Quickly acquire accurate 3D information, including height, without reducing takt time
- It is not affected by the material, color, luster, and shape of the object, enabling stable inspection.
- Simultaneously inspect multiple items such as appearance, dimensions, and shape to streamline the process.
- Real-time inspection to improve yield rates
- Detailed inspection data of all units can be used for the prevention of the recurrence of defects, trend analysis, statistics, traceability, predictive maintenance, etc.
- Real-time data acquisition can also be used for feedback control of equipment
IPQCCO will utilize measuring instruments, 3D displacement meters, 3D cameras, and lighting systems that use the pattern projection method to obtain stable and accurate data using new technologies and measurement principles. By processing the data acquired by these data in 3D images, it is possible to perform automatic total inspection corresponding to various objects, conditions, and inspection items without affecting the takt time.