Precision isn’t just a buzzword in the fast-paced manufacturing world—it’s the lifeblood of successful operations. Quality control is the cornerstone of excellence, especially in CNC (Computer Numerical Control) machining, where millimeters of matter and tolerances can make or break a project. But how does CNC quality control ensure delivery quality that meets—and often exceeds—expectations? Let’s dive into the intersection of technology, precision, and client satisfaction.
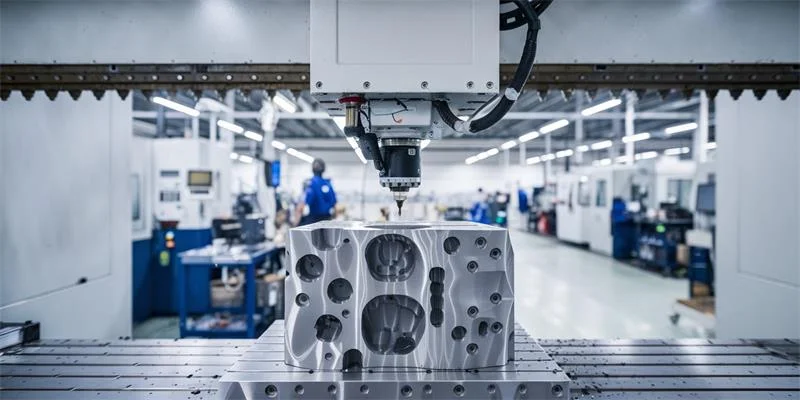
Why CNC Quality Control Matters
Imagine this: a critical component for an aerospace engine fails in operation because its dimensions were slightly off. The result? Potential millions in losses, not to mention safety risks. Quality control in CNC machining is the safeguard that prevents such scenarios. It’s not just about catching mistakes; it’s about proactively designing systems that ensure errors don’t happen in the first place.
CNC quality control ensures delivery quality in three critical ways: precision manufacturing, real-time monitoring, and adherence to stringent standards. These elements don’t just promise high-quality output; they guarantee it.
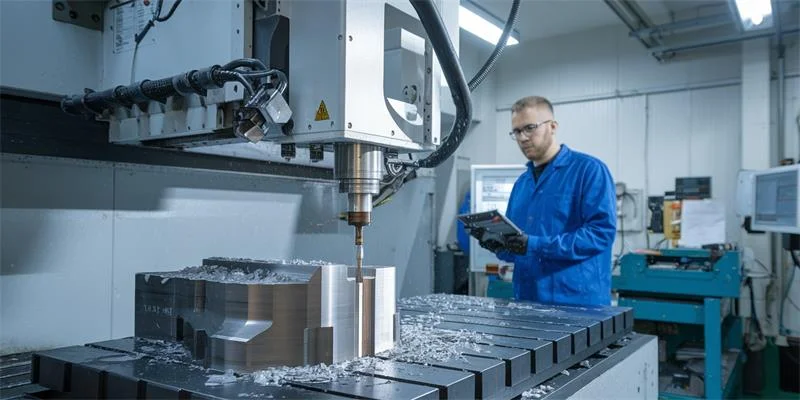
Precision Manufacturing: The Foundation of Excellence
CNC machines are marvels of modern engineering, capable of shaping metals and other materials into intricate designs with astonishing accuracy. But even the most advanced machines require oversight.
Quality control begins at the design stage. Engineers create detailed CAD (Computer-Aided Design) files that serve as blueprints for CNC machines. However, transferring a digital design into a physical product can introduce variability. This is where quality control shines, ensuring that the output matches the design to the letter.
Using advanced tools like Coordinate Measuring Machines (CMMs) and laser scanners, technicians measure dimensions with micrometer-level precision. These measurements confirm that every part—whether it’s the thousandth unit or the very first—meets exact specifications.
Real-Time Monitoring: Detecting and Correcting Issues
Gone are the days when quality control was a post-production step. Today, it’s embedded into the manufacturing process itself. Real-time monitoring technologies allow manufacturers to detect and address issues as they arise.
For instance, sensors integrated into CNC machines can measure variables like temperature, vibration, and tool wear. Deviations from the norm trigger alerts, prompting immediate corrective actions. This approach minimizes waste, reduces downtime, and ensures consistent quality.
Non-contact inspection methods, such as optical or laser measurement systems, add another layer of precision. These systems are fast, accurate, and versatile, making them ideal for inspecting parts without slowing production.
Meeting Standards: Quality That Speaks Globally
In an increasingly globalized market, adhering to international quality standards isn’t optional—it’s a necessity. Certifications like ISO 9001 and AS9100 demonstrate that a manufacturer operates with a commitment to quality, safety, and consistency.
CNC quality control ensures compliance with these standards through rigorous documentation and testing. Every step, from material selection to final inspection, is tracked and recorded. This meticulous approach not only ensures delivery quality but also builds trust with clients across industries like aerospace, automotive, and medical devices.
Delivering Excellence: From Factory to Front Door
It’s one thing to produce a high-quality part; it’s another to ensure it arrives at its destination in perfect condition. Delivery quality encompasses more than just the product itself—it includes packaging, transportation, and communication with clients.
For example, CNC manufacturers often use protective packaging tailored to the specific dimensions of their parts. This prevents damage during transit, ensuring the end user receives a component ready for immediate use.
But the human element is just as important. Clear communication about production timelines, quality assurances, and shipping updates strengthens relationships with clients. When manufacturers invest in these processes, they don’t just deliver parts—they deliver peace of mind.
The Future of CNC Quality Control
As industries evolve, so too will the demands placed on CNC machining. The rise of automation, AI, and IoT (Internet of Things) is already transforming quality control. Predictive maintenance powered by AI, for instance, allows machines to anticipate failures before they occur. Similarly, IoT-enabled devices can provide real-time updates on a part’s status throughout its lifecycle.
These advancements promise to make CNC quality control even more robust, ensuring delivery quality remains a hallmark of excellence in manufacturing.
Building Trust, One Part at a Time
CNC quality control isn’t just about producing parts that meet specifications—it’s about delivering trust. Every accurately machined component tells a story of meticulous planning, advanced technology, and an unwavering commitment to quality.
For clients, this means products they can rely on, timelines they can trust, and partnerships that drive success. And for manufacturers, it means a reputation for excellence that opens doors to new opportunities.
So, the next time you hold a perfectly machined part, remember: behind that piece of precision engineering lies a world of quality control dedicated to ensuring delivery excellence.