The high-strength fasteners when the wind turbine is running are subjected to the combined loads of axial force, bending moment, transverse force, and torque while bearing the gravity load, thermal load, and aerodynamic load transmitted by the blades and transmitted to the main force structure. In addition, wind turbines are often operated in areas rich in wind resources, and even offshore wind power is subject to extreme weather or environments such as typhoons, severe colds, corrosion, and thunderstorms. Fan vibration detection, performance testing, and quality control of high-strength fasteners have become important parts that cannot be ignored.
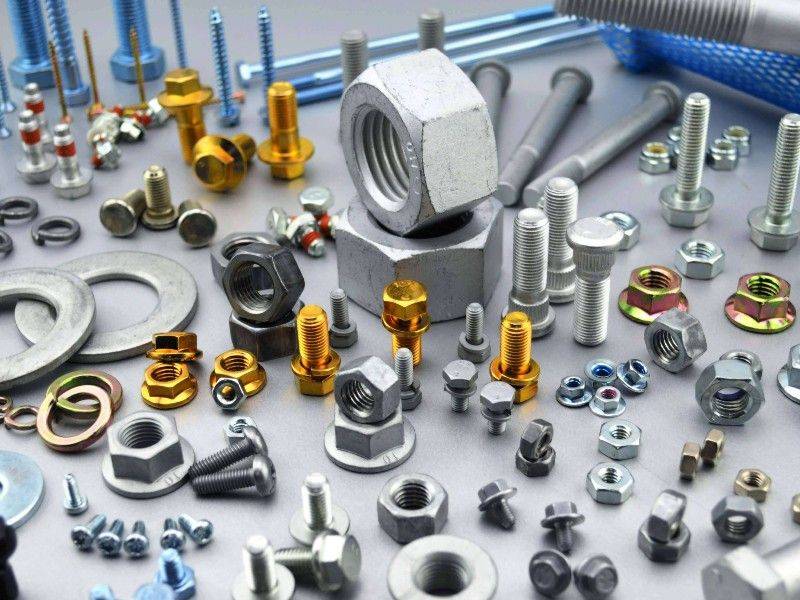
Considering the quality control direction of high-strength fasteners, the test items that may be involved can be classified as follows:
1. Quality control of raw materials
The advantages and disadvantages of raw materials directly affect the comprehensive mechanical properties and safety of high-strength fasteners for wind power.
Test items: chemical composition analysis, tensile test, load retention test, hardness test, retempering test, impact test, wedge load test, shear test, fatigue test, locking performance, torque coefficient, fastening shaft force, friction coefficient, anti-slip coefficient, screw-in test, gasket elasticity, toughness test, hydrogen embrittlement test, etc.
2. Quality control of processing technology
The manufacturing process of high-strength fasteners includes forging, cutting and heat treatment, etc., and the dimensional tolerance and geometric tolerance of fasteners should be strictly implemented in accordance with the requirements corresponding to the grade.
Test items: thread pass and stop gauge, surface roughness, thread large diameter, medium diameter, small diameter, tooth shape angle, pitch and other dimensions.
3. Quality control of heat treatment process
Taking the 10.9-grade high-strength fasteners for wind power as an example, the heat treatment process is realized by spheroidization degradation and tempering, and the process control and supervision of the implementation of the heat treatment and tempering process of high-strength fasteners should be strictly strengthened.
Test items: microstructure, decarburized layer depth, carburized layer depth, grain size rating, inclusion content, low magnification structure, etc.
4. Surface treatment quality control
In order to reduce the risk of hydrogen embrittlement in processes such as pickling and electroplating and ensure service life, sandblasting + non-electrolytic Dacromet coatings are usually used to provide surface corrosion protection.
Test items: neutral salt spray test (NSS), acetate mist test (AASS), copper accelerated acetate spray test (CASS).
5. Non-destructive testing supervision
NDT does not damage or affect the performance of the inspected high-strength fasteners, and detects whether there are defects or unevenness in the inspected parts, and then determines whether the inspected high-strength fasteners are qualified or not.
Test items: ultrasonic testing, radiographic testing, magnetic particle testing, penetration testing.
6. Product failure analysis
Failure analysis is to determine the cause of fastener failure, which is of great significance to improve product quality, improve production technology, avoid the recurrence of similar failure accidents and arbitration failure accidents. The causes of failure of fasteners are multifaceted, and the main reasons must be found in the analysis, focusing on the analysis of the fracture of the failed part and the use of the stress state, to find out the typical characteristics and related factors, and to verify.
Failure analysis items: macroscopic morphology analysis, electron microscopy analysis, metallographic analysis, chemical composition analysis, microhardness analysis, mechanical property test, non-destructive testing, residual stress test, etc.