In the world of manufacturing, we repeatedly create and test prototype models to ensure quality and design products that meet planning requirements. In this design process, there is a development technique called “rapid prototyping” that accelerates the creation of prototype models that were previously performed by hand with the power of technology. This time, we will explain the basics and benefits of rapid prototyping, and the points for successful product development with rapid prototyping.
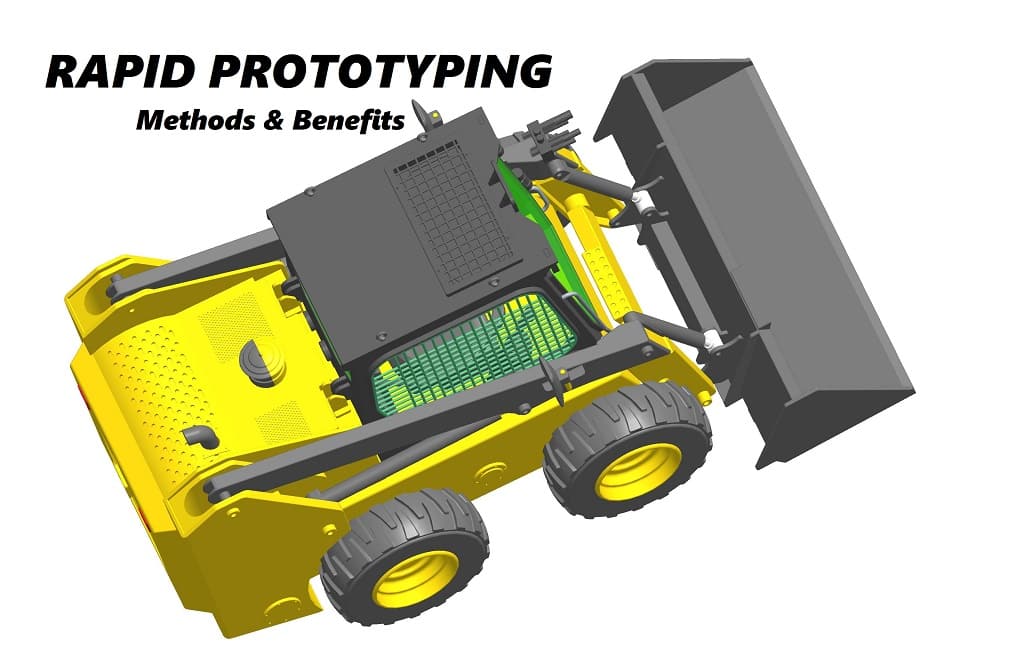
What is Rapid Prototyping?
Rapid prototyping is a prototyping development technique that uses 3D technology to quickly create prototype models of products.
Rapid prototyping is roughly done in the following steps:
- Prepare 3D data that is a digital image of the product
- Divide 3D data into slices to generate “slice data”
- Enter slice data into a molding device called an “RP machine”
- A modeling device stacks a physical model based on slice data in the real world
Originally, large commercial machines such as stereolithography machines and powder sintering machines were the mainstream of RP machines, but the presence of 3D printers that have appeared in recent years has dramatically increased the popularity of rapid prototyping.
Rapid Prototyping Methods
The above procedure uses a manufacturing method called “additive manufacturing method” and is mainly classified into the following methods.
- Stereolithography
Stereolithography is a method that uses “photo-curable resin” and ultraviolet lasers. Photo-curable resin is a special material that is cured by ultraviolet rays, and is shaped by repeating the operation of piling up resin and irradiating it. Since the resin cures immediately after light irradiation, the molding speed is fast, and the advantage is that complex molding can be smoothly reproduced.
- Thermal Dissolution Lamination Method
Thermal dissolution lamination (FDM) is a method of dissenting and laminating resin dissolved by heat. It takes time to cool after lamination, and the dimensional accuracy is low, but the introduction hurdle is low because the equipment is inexpensive.
- Powder Method
There are two main types of powder method: sintering nylon powder with a thermal laser, and curing and laminating gypsum powder. Nylon has excellent strength and enables the creation of prototype models that can withstand assembly tests on actual machines. On the other hand, gypsum is excellent in low cost and quick modeling, and can be colored at the time of output.
Benefits of Rapid Prototyping
Learn three benefits of using rapid prototyping in product development.
- Significantly Reduce Time-To-Market
Rapid prototyping speeds up planning, design, prototyping, and feedback cycles to significantly reduce product lead times to market. In recent years, product development has become more liquid and shortened in the product lifecycle, so it is a major advantage to increase market competitiveness.
- Streamline Engineering Effort and Costs
When prototyping is done by hand, skilled technicians need to spend a long time creating clay models (clay) and mockups (wood). Rapid prototyping, on the other hand, can mechanically create prototypes, significantly reducing engineering effort and costs.
It is difficult to make a difference between requirements and the image of the actual product
It is important to improve design accuracy in order to commercialize that is true to the concepts defined in the requirements definition and requirements definition. Rapid prototyping speeds up the prototyping and verification cycle, and improves design accuracy through repeated fine-tuning. In addition, unlike simulations on computers, detailed verification using physical prototypes is possible. As a result, it is difficult to make a difference between the product image at the planning stage and the product actually made.
How To Successfully Develop Products Through Rapid Prototyping?
Here are two key points to successful product development with rapid prototyping.
- Collaboration with CAD/CAE
The 3D data from which the prototype is produced is created using 3DCG tools and CAD (computer design) software. After data creation, it is effective to verify the shape and material with CAE (computer simulation) software before molding with an RP machine. By linking CAD and CAE, it is possible to identify problems in the design process at an early stage.
2. Use of 3D Scanners
In order to create 3D data, there is an approach to scanning the real thing with a 3D scanner, in addition to a digital-based method using CAD and the like. When using 3D scanning for rapid prototyping, the following situations are assumed:
- When developing parts of a device, scan the body for accurate dimensions
- Explore improvements from existing scan data
- Combine scan data with CAD-created data
Immediately after scanning, it is output as “point cloud data” composed of points. After that, depending on the application, it is necessary to convert it to “mesh data” with simple faces affixed and CAD data holding detailed formulas.
Rapid Prototyping Reduces Product Development Lead Times
In the manufacturing industry in the future, due to the diversification and fluidization of market needs, a development system that can handle high-mix, low-volume production will be required. Companies must streamline their product development cycles more than ever before.
However, as times change, so does technology. 3D printers and CAD to help with rapid prototyping have become more widespread than ever before. Rapid prototyping, which focuses on the design process and enables speedup, is still effective. It is also effective to utilize automation technologies such as industrial robots that can speed up the manufacturing process.
Let’s increase market competitiveness with the aim of shortening the lead time of product development in preparation for the next era.