The so-called reverse engineering technology is to 3D scan the physical prototype, data acquisition, through data processing, coordinate dimensional reconstruction, and other processes, to construct a three-dimensional model with the same shape and structure. Then, innovation is achieved by copying the prototype or redesigning it on the basis of the prototype. Therefore, reverse engineering is not a simple 3D scanning and copying process. The purpose of reverse engineering is to use physical objects to obtain point clouds and optimize and innovate designs based on point clouds. Of course, reverse design is not mysterious. It is closely related to our lives. The upgrading of bicycles in daily life, the more flawless car streamline, is inseparable from reverse design.
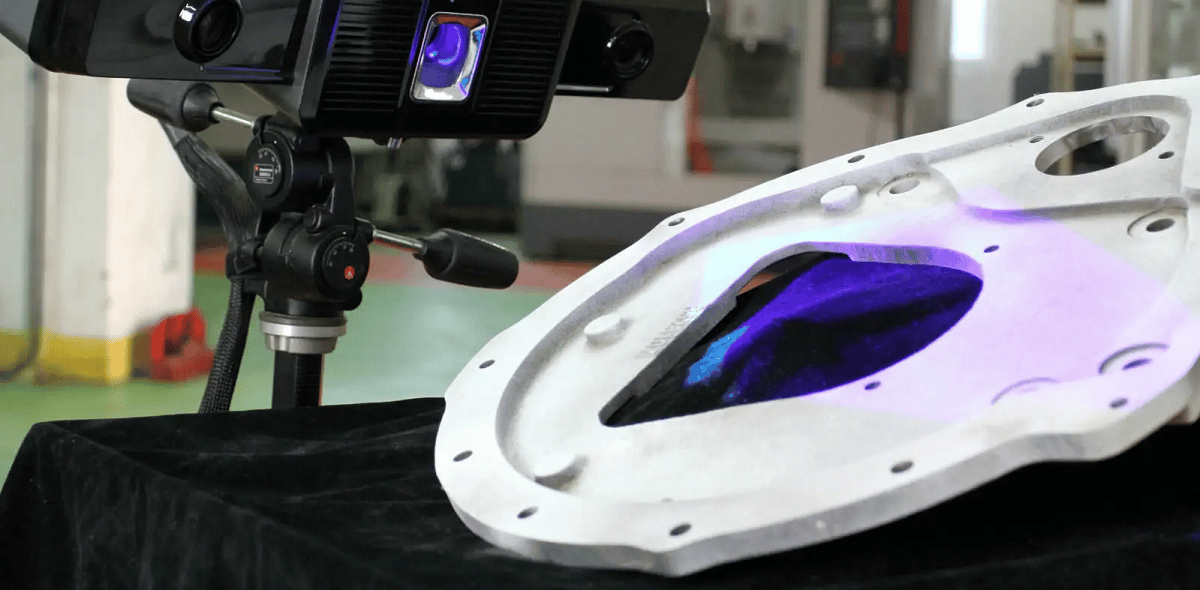
Reverse Engineering Application – When To Use Reverse Engineering?
Reverse engineering is mainly applied to the following aspects:
1. Obtain a parametric model that can be edited by three-dimensional software, which is convenient for machining enterprises such as CNC machine tools to process materials.
2. In order to obtain more reasonable data structures, such as the improvement of the streamlined shape of the car, the improvement of the turbine blade, etc. The data obtained by the scan is modified by reverse engineering to achieve the purpose of optimization and innovation.
3. In order to get 2D drawings. Machine plus enterprises generally pay more attention to the acquisition of two-dimensional drawings, reverse engineering can obtain a coordinate dimensional model of the object through the reverse design of the scanned data, and the two-dimensional drawing of any section of the physical object can be easily and quickly obtained in the drawing software.
4. Scanning provides an opportunity for a combination of reverse engineering and quality control. By capturing millions of points of each table to scan the inspected workpiece, obtaining its surface coordinate dimensional data with the relevant reverse engineering and detection software, and generating error reports, we greatly improve the work efficiency of the inspection link, improve the quality of the product.
IPQCCO Reverse Engineering Service
Reverse engineering has gained wide application in many aspects, and IPQCCO has also developed the reverse service module. Below is our service flow for reverse service design.
1. Obtain point cloud data through 3D scanner or provide point cloud data to customers.
2. The point cloud data is processed by software (geomagic, gom, etc.) to obtain the triangular mesh surface data. Including STL data for coordinate change, point cloud noise reduction, smoothing, optimization, simplification, and other preprocessing. The data obtained in this step can be used for coordinate dimensional engraving, 3D printing, comparison analysis, etc.
3. Through the reverse software, the reverse software can generally use UG, CATIA, GEOMAGIC DX, and other professional software to process the obtained triangular mesh surface data. Including patch fitting, section creation, curve extraction, and many other feature extraction methods, at this time, innovative design, optimization design, etc. can be carried out.
4. After a series of operations such as software calculation extension and shear, the reverse parameter model is obtained, which can be used for high-precision CNC machining and mold design.
Through the above four steps, we can complete the reverse engineering design for a part, through reverse engineering design we can not only obtain the parametric model, but also obtain the STL data of the model and compare detection, coordinate dimensional engraving, and at the same time obtain the parametric model and optimize the design.