Screws are widely used in many industrial products. Despite their simple structure, they are commonly used in the assembly of industrial products, requiring high precision.
As a result, both screws and screw holes typically require a 100% inspection. In the past, this task was performed manually by individuals. However, by automating the inspection of screws and screw holes, significant efficiency improvements and quality enhancements can be achieved. In this article, we will introduce the knowledge related to the automation of screw inspection.
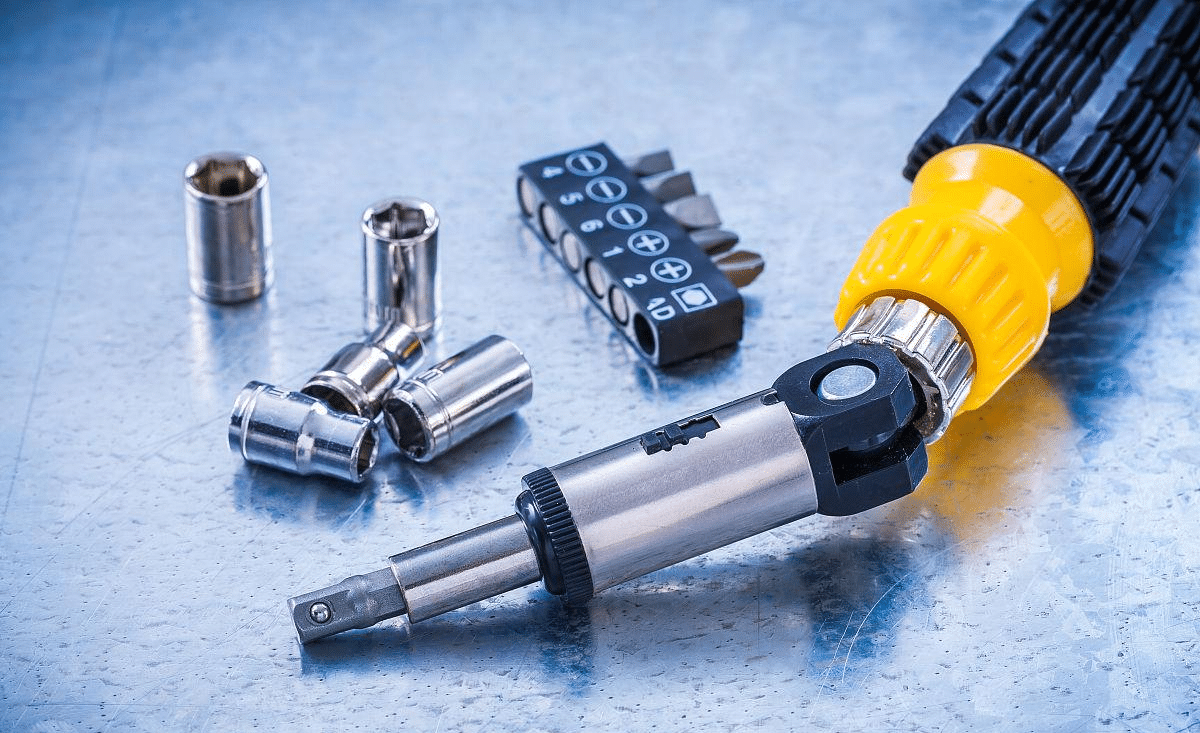
1. What is screw hole inspection?
What characteristics are required for screws and screw holes? We will explain the specific contents of screw hole inspection and also highlight the issues with manual screw hole inspection.
(1) Features required for screws and screw holes
The following are the four main characteristics generally required for screws:
- Fastening: The most common function of screws, which is to secure objects together and prevent movement.
- Joining: The ability to connect and join objects, such as in plumbing or piping.
- Tension: The function of preventing wires or ropes from loosening when pulled.
- Sealing: The ability to seal, like a lid on a bottle.
While these functions are required in a fixed state, operational use of screws may also require functions such as “conveying and movement,” “measurement and fine adjustment,” “increasing or decreasing power,” and “compression or compression resistance.”
Furthermore, although screws are commonly referred to as a single term, their shapes vary widely depending on the product they are used in and the desired functionality. Screws are classified into categories such as the head, threaded shaft, unthreaded cylindrical part, seating surface, and tip, each with further sub-classifications.
(2) Contents checked during screw hole inspection
Considering the diverse range of screw shapes and properly fastened screw holes, what items are typically examined during inspection?
The following are representative examples:
① Missing or misaligned screw threads
If there are missing or misaligned threads on the screw, it may not securely fasten into the screw hole. It may appear to be properly fastened when forcibly tightened, but leaving it as is could lead to damage.
② Screw damage
If the screw is slanted or damaged, it requires sorting. Even if the part of the screw that enters the screw hole is intact, it may not fulfill its fastening role. Visual inspection is necessary since this cannot be detected by simply inserting it into the screw hole.
③ Depth of the screw hole
If the screw hole is too deep or too shallow compared to the specified dimensions, the screw may not fit properly. This is due to differences in the length of the screw’s threads and the depth and number of threads in the screw hole.
④ Size of the screw tip
While attention is often focused on the screw threads, the shape of the screw tip is also crucial. It should snugly fit the bottom of the screw hole and avoid damaging unnecessary parts during fastening.
(3) Issues with screw hole inspection
As mentioned, there are multiple aspects to consider when inspecting screws. However, conducting all these inspections manually presents several issues.
- Time-consuming for 100% inspection
- Difficult to manage fastening force
- Possibility of oversight in visual inspections
Performing manual inspections incurs labor costs, which can lead to price increases or decreased profitability. Additionally, managing fastening force and potential oversights in visual inspections make it challenging to establish a stable inspection environment, potentially resulting in the release of defective products.
2. What is an automatic screw hole inspection device?
To address the issues with manual screw and screw hole inspections, automatic inspection devices have been developed. Let’s review examples of the configuration of an automatic inspection device and important considerations when considering its implementation.
(1) Configuration examples of automatic screw hole inspection devices
There are different types of automatic inspection devices for screws and screw holes, each with different inspection items and methods. Here are some examples:
① Actuator-driven type
This device involves inserting a screw into the screw hole using an actuator and detects abnormalities in the screw and screw hole based on the load applied during insertion. It offers high precision and can detect various defects, but the equipment itself tends to be relatively expensive.
② Probe inspection type
This device involves inserting a probe into the screw hole and examining the shape of the hole by observing conditions such as overcurrent or laser. It is a non-contact inspection method, so it does not exert a load on the screw hole like the actuator-driven type. Additionally, it has the advantage of lower running costs since the inspection device itself is less prone to wear and tear. Please note that these are just examples, and there may be other types of automatic screw hole inspection devices available. On the one hand, probe-type inspections cannot inspect the screw body.
③ Optical inspection type
This inspection device captures the appearance using a camera or similar device and analyzes the image to determine whether the product is good or defective. Similar to probe inspections, it is a non-contact method, allowing for cost and space savings. This type of inspection is mainly used for inspecting the screw body.
(2) Points to consider when choosing a screw hole automatic inspection device
What should be considered when choosing an automatic inspection device for screws and screw holes? Pay attention to the following two points in particular.
Can it be integrated into the current inspection line?
Can it inspect the required content?
① Can it be integrated into the current inspection line?
Even if you automate the inspection of screws and screw holes, completely changing the entire manufacturing process is a major undertaking. If it can be integrated into the current inspection process with minimal changes to the process, costs can be kept low. Moreover, there will be no adverse effects as the surrounding movements remain the same.
② Are the inspection items appropriate?
Each automatic inspection equipment has its own inspection method and predetermined inspection items. Ensure that it can detect the necessary inspection items with the required accuracy. If there is a mismatch, choosing equipment that can be customized is also an option.