Sheet metal fabrication is a critical process in manufacturing, requiring precise quality control to ensure components meet exact specifications. This article examines modern inspection methods, advanced tools, and systematic processes used in sheet metal quality assessment. From traditional measurement techniques to cutting-edge optical systems, we’ll explore how manufacturers achieve accuracy and consistency in their sheet metal products.
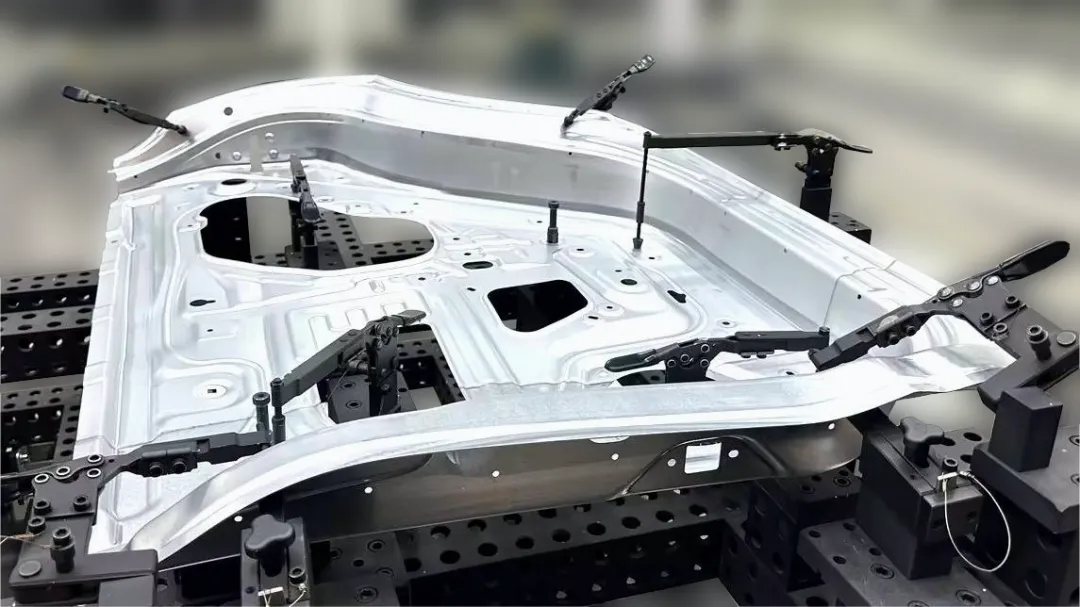
Critical Dimensions in Sheet Metal Inspection
Sheet metal parts must meet strict dimensional tolerances to function properly in their intended applications. The most commonly inspected dimensions include thickness, flatness, hole diameters, bend angles, and edge conditions. Thickness measurement is particularly crucial as it directly affects the part’s strength and weight characteristics. Modern measurement tools can detect variations as small as a few micrometers, ensuring compliance with engineering drawings.
Advanced measurement systems now combine multiple inspection functions into single devices, allowing simultaneous checking of several critical dimensions. This integration significantly reduces inspection time while improving accuracy.
Bend angle verification is another essential aspect of sheet metal inspection. Precise bending ensures proper fit and function in assembled products. Traditional protractors have been largely replaced by digital angle finders and 3D measurement systems that provide more accurate readings and automated data recording. Edge quality inspection checks for burrs, dents, or other imperfections that could affect assembly or performance.
Traditional Measurement Tools
Despite advancements in technology, traditional tools remain valuable for certain sheet metal inspection tasks. Calipers, micrometers, and height gauges provide reliable measurements for basic dimensional checks. Surface plates and straight edges are still used for flatness verification, especially for large parts that might not fit in automated systems.
Radius gauges help inspectors verify bend radii, while feeler gauges check gaps between mating surfaces. These manual tools require skilled operators but offer flexibility and immediate feedback without complex setup procedures. Many facilities maintain these traditional tools as backup systems or for quick checks during production runs.
Automated Optical Systems
Modern optical measurement systems represent a significant advancement in sheet metal inspection. These non-contact systems use high-resolution cameras, structured light, or laser scanning to capture complete 3D profiles of parts. Vision systems can process hundreds of measurements in seconds, comparing them against CAD models with micron-level precision.
Key advantages include elimination of operator influence, complete surface analysis, and automated data reporting. Some advanced systems incorporate artificial intelligence to identify potential defects or trends that might indicate production process issues. These systems are particularly valuable for complex geometries or high-volume production environments.
Sheet Metal Quality Inspection Methods
Many facilities now implement hybrid inspection strategies combining the following multiple methods to achieve comprehensive quality assessment while optimizing inspection cycle times:
Dimensional Verification
This fundamental method checks critical measurements including thickness, length, width, hole diameters, and bend angles. Modern approaches combine direct measurements with comparative analysis against CAD models. Advanced systems can measure hundreds of points in seconds, generating comprehensive deviation reports.
Surface Quality Analysis
Surface inspection evaluates finish quality, detecting scratches, dents, pits, or other imperfections. Techniques range from visual examination to automated optical scanning. Surface roughness measurement quantifies texture characteristics using parameters like Ra (average roughness) and Rz (maximum height).
Geometric Tolerance Assessment
This method verifies form and position tolerances including flatness, straightness, circularity, and parallelism. Specialized equipment measures these geometric characteristics with micron-level precision, ensuring components fit and function as intended in assemblies.
Sheet Metal Inspection Tools
Optical Comparators
Project magnified part profiles onto screens with overlay templates for rapid visual comparison. Effective for checking 2D contours, hole patterns, and edge conditions.
Coordinate Measuring Machines (CMMs)
Precision instruments that use touch probes to collect 3D coordinate data from parts. Capable of measuring complex geometries with micron-level accuracy.
Laser Scanners
Non-contact devices that capture complete surface data by projecting laser lines onto parts. Ideal for free-form surfaces and flexible materials.
Digital Height Gauges
Electronic measurement devices with vertical scales and touch probes. Used for dimensional checks and surface profile measurements.
Surface Roughness Testers
Specialized instruments that quantify surface texture using diamond-tipped stylus or optical methods. Provide numerical roughness values for quality control.
Automated Vision Systems
Camera-based inspection systems that compare parts to digital templates. High-speed solutions for production line quality checks.
Tool Type | Measurement Range | Typical Accuracy | Speed | Best For |
---|---|---|---|---|
Manual Calipers | 0-300mm | ±0.02mm | Medium | Quick manual checks |
Optical Comparator | Varies by model | ±0.005mm | Medium | 2D profile verification |
Portable CMM | 1-4m | ±0.015mm/m | Slow | Large part measurement & Complex 3D geometries |
Laser Scanner | Varies by system | ±0.01mm | Fast | Free-form surfaces |
Sheet Metal Inspection Process
- Preparation Phase: Review engineering drawings and specifications to identify critical inspection points and tolerances. Select appropriate measurement tools based on part features and required accuracy.
- Initial Sample Inspection: Perform comprehensive measurement on first-off samples to validate manufacturing process capability before full production begins.
- In-Process Verification: Conduct periodic checks during production runs to detect any process drift. Common methods include spot checks of critical dimensions and visual surface examination.
- Final Inspection: Complete detailed assessment of finished parts, often using multiple measurement methods. Document all measurements and compare against specification limits.
- Data Analysis and Reporting: Compile inspection results, calculate process capability indices, and generate quality reports. Implement corrective actions if non-conformances are identified.
Modern inspection processes increasingly incorporate automated data collection and analysis, reducing human error and enabling real-time process adjustments. Many facilities now integrate inspection directly with manufacturing equipment for closed-loop quality control.
Process Integration and Data Management
Modern sheet metal inspection doesn’t operate in isolation—it’s integrated with the entire manufacturing process. In-process gauging provides real-time feedback to production equipment, enabling immediate adjustments. Statistical process control (SPC) software analyzes measurement data to identify trends and prevent defects before they occur.
Digital twin technology is emerging as a powerful tool in sheet metal fabrication, creating virtual models that mirror physical parts throughout their lifecycle. This approach enables predictive quality control and virtual inspection before physical production begins.
Automated reporting systems generate inspection certificates and quality documentation, reducing paperwork and ensuring traceability. Cloud-based quality management systems allow access to inspection data across multiple facilities, supporting global quality standards and facilitating audits. The combination of advanced measurement technologies with digital process integration represents the future of sheet metal quality assurance.