Surface finish is an often overlooked aspect of precision manufacturing that can significantly impact a part’s functionality, appearance, and performance. Beyond dimensional accuracy, achieving the right surface finish is crucial in the aerospace and medical device industries. This blog delves into what surface finish is, its measurement, its importance, and how manufacturers achieve and control it in various processes.
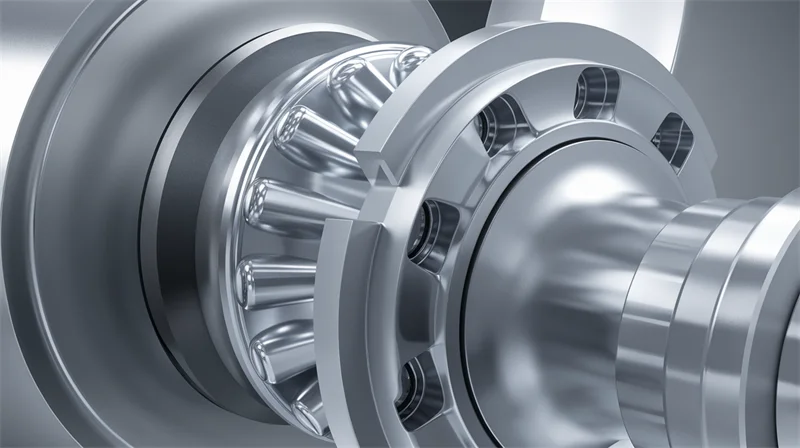
What Is Surface Finish?
Surface finish, also referred to as surface texture or roughness, describes the quality of a part’s surface in terms of its smoothness and the presence of irregularities. It is determined by:
1. Roughness: The fine irregularities on a surface, typically resulting from the machining or forming process.
2. Waviness: Larger, more widely spaced deviations caused by machine vibration or warping.
3. Lay: The predominant direction of the surface pattern, such as linear, circular, or random.
Why Surface Finish Matters
1. Functionality
Surface finish directly impacts a part’s performance. For example:
· Friction: A smoother surface reduces friction, which is critical for sliding components like shafts and bearings.
· Sealing: Precision finishes are essential in sealing applications, ensuring no leaks in gaskets or mating surfaces.
2. Durability
A poor surface finish can lead to stress concentrations, making parts more prone to wear, fatigue, or corrosion.
3. Aesthetics
In consumer products, the surface finish often influences buyer perception. A polished, defect-free finish conveys quality.
4. Coating and Adhesion
Surface finish affects how well coatings, paints, or adhesives adhere to a part. Certain finishes are better suited for these applications.
5. Heat Dissipation
In some cases, such as electronics, surface texture can be designed to enhance thermal conductivity and heat dissipation.

Measuring Surface Finish
Surface finish is quantified using parameters defined by industry standards (e.g., ISO, ASME). The most common are:
Ra (Roughness Average)
The average deviation from the mean surface profile. Lower Ra values indicate smoother surfaces.
Rz (Average Maximum Height)
Measures the height difference between the highest peak and lowest valley in a sample length.
Surface Profilers
Devices like stylus profilometers and optical scanners provide precise measurements of surface roughness.
How Surface Finish Is Achieved in Manufacturing
1. Machining
· Turning and Milling: Controlling feed rate, speed, and tool sharpness to achieve desired finishes. High-speed machining often yields better results.
· Grinding: Used for ultra-smooth finishes, particularly in hard metals.
2. Abrasive Processes
· Polishing: Removes minor imperfections and achieves a mirror-like finish.
· Lapping: Involves rubbing two surfaces with an abrasive slurry to achieve ultra-flat finishes.
3. Coating and Plating
· Techniques like anodizing, electroplating, or powder coating can enhance surface finish while adding functionality.
4. Surface Treatments
· Shot Peening: Improves fatigue resistance by compressing the surface.
· Etching or Texturing: Adds micro-patterns for specific functions, such as grip or aesthetics.
Challenges in Achieving Consistent Surface Finish
A. Material Properties
Some materials, like soft plastics or brittle ceramics, are more challenging to finish consistently.
B. Tool Wear
Dull tools can degrade surface finish quality over time, requiring frequent maintenance or replacement.
C. Process Variability
Factors like machine vibration, environmental conditions, and operator skill can introduce inconsistencies.
Applications of Surface Finish
1. Aerospace
o Critical for aerodynamic efficiency and fatigue resistance in turbine blades and airframes.
2. Medical Devices
o Implants and surgical tools require highly polished, biocompatible surfaces.
3. Automotive
o Engine components, such as pistons and crankshafts, rely on precise finishes for performance and longevity.
4. Electronics
o Smooth finishes are necessary for heat sinks and connectors to ensure proper functionality.
Emerging Trends in Surface Finish
Emerging Trends in Surface Finish
1. Advanced Coatings
Nano-coatings and self-healing surfaces are paving the way for improved wear resistance and durability.
2. Additive Manufacturing
Post-processing methods like CNC machining or chemical polishing are being developed to refine 3D-printed surfaces.
3. Automation and AI
Automated inspection systems, powered by AI, are improving consistency and quality control in surface finish measurements.
4. Sustainability
Eco-friendly finishing processes, such as water-based polishing compounds and energy-efficient equipment, are gaining traction.
Surface finish plays a pivotal role in precision manufacturing, influencing everything from functionality to appearance. By understanding the factors that impact surface finish and implementing robust measurement and control processes, manufacturers can meet the demanding requirements of modern industries. As technology advances, the ability to achieve and maintain precise surface finishes will continue to enhance product performance and reliability, setting new standards for quality in manufacturing.