In order to safely and smoothly conduct business with a new company, it is necessary to visit the factory and inspect the site. Factory audits are conducted to understand the state of management and manufacturing processes.
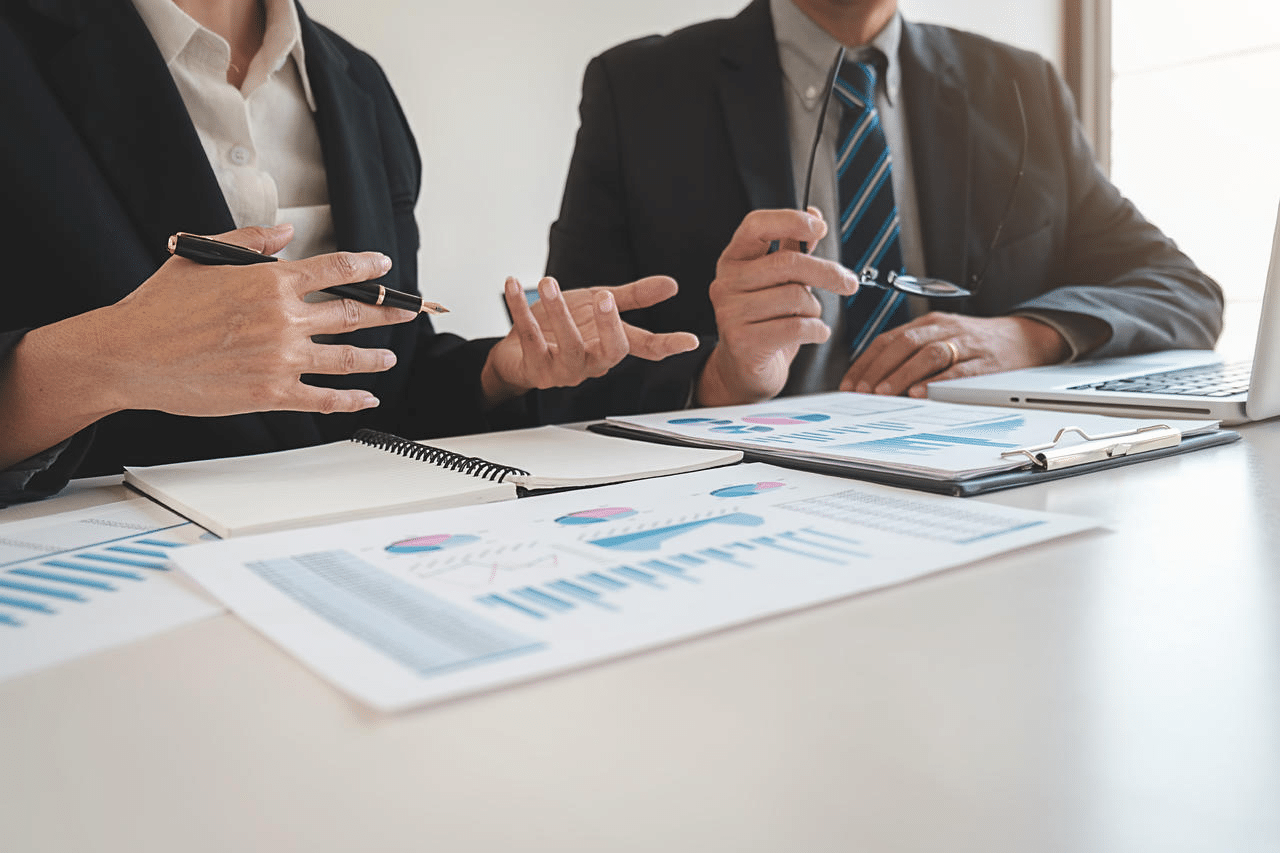
The purpose of factory audits is not only for new suppliers but also for existing suppliers to provide guidance on factory technology and quality improvement. Even if a factory is manufacturing products smoothly, a factory audit may uncover deficiencies. It is not uncommon for products not to be manufactured as requested and for problems to occur after production. It is not only the factory that is at fault, but also the company that did not conduct a thorough factory audit.
In this post, we introduce factory audits to check a company’s credibility, technical capabilities, product workmanship, and accuracy, etc. Please make use of this information for secure business transactions between companies.
1. What Is A Factory Audit?
It is important that factory audits be conducted with a clear purpose. There is no point in conducting a factory audit if it is just a paperwork audit without a purpose. It is required to have a clear objective and to focus on the contents of the audit to be checked.
1-1. What is to be determined?
We will be looking at the current status of the client factory and the anticipated risks that may occur in the future. Another key point is whether the factory’s production level is capable of reaching the required level of quality. If it is not at the required level, the purpose is to identify areas for improvement.
1-2. Confirmation of Product Accuracy
While it is important that the requested product is manufactured smoothly, product accuracy is an important issue that affects the credibility of the company. In the case of difficult products, if the product accuracy is not sufficient, the loss will be significant.
Even if the factory produces the work as requested, there may be complaints after production that the product is not finished adequately.
The occurrence of a claim is evidence of a problem on both sides. The company that commissioned the work must carefully check the factory’s production process and accuracy, and must work to understand and realize the technical level. The objective is also to confirm that the contractual matters are being properly executed.
2. What Areas Will Be Checked in Factory Audit?
Factory audits are conducted using the Factory Audit Check Sheet. It contains a checklist of important checks to prevent omissions and diagnostic errors. It is important to know what specific areas will be checked. Factories that undergo audits can also prepare in advance to ensure a smooth completion.
2-1. Work Processes and Records
The work processes involved in production and what kind of maintenance is being performed are also important items to be checked. If there is unevenness or variation in the work process, product quality will not be consistent, and production itself will not be stable. Maintenance records are the key to understanding what efforts are being made to ensure that operations are free from variation. By checking the records, we can also learn about the factory’s sincere attitude.
2-2. Thorough implementation of 5S in the factory
5S is an acronym for the five key words: seiri (orderliness), seiton (orderliness), seiso (cleanliness), seiketsu (cleanliness), and shitsuke (discipline). They are words that every factory manager should know, and they must be properly addressed.
Organizing means separating the necessary from the unnecessary and discarding what is deemed unnecessary. Organization is also used in workspace and information management. In the production process, it can also apply to artificial things, such as the next set-up for smooth operation.
Seiton means that necessary items are placed in their proper places and displayed in a way that is easy for everyone to understand.
Cleanliness implies a constant effort to beautify the environment and to make the entire plant user-friendly. Cleaning and cleanliness are interlinked; they are about maintaining a clean state. We must also be conscious of maintaining pleasant conditions that do not cause discomfort to those who work in the factory and those who come to the factory.
2-3. Storage of Raw Materials
The storage of raw materials necessary for production is also an item to be checked during factory audits. It is important to take care that raw materials are not mixed with other materials and that efforts are made to prevent accidents from occurring, for example, by properly performing first-in, first-out (FIFO) storage. If the materials are placed on the floor, the risk of accidents and defective products also increases.
2-4. Checking waste
Check the waste in the garbage cans and also the production efficiency of the factory. If there is waste that should not have been produced, it means that a loss has occurred due to a mistake. The waste bins will also reveal the defect rate of the entire factory.
2-5. Separation of defective products
Rarely, accidents occur in which defective products are mixed in with shipped goods. Defective products must be segregated, but it is also important to separate them according to the cause of the defect. The frequency of collection is also a key point to focus on.
Factories that randomly collect defective products and do not calculate the percentage of defective products need to be improved.
3. Types Of Factory Audits
There are three types of factory audits. There are internal audits (first-party audits) in which the company itself is audited, second-party audits in which interested suppliers and others are audited, and third-party audits by ISO auditors who have no vested interest in the company.
The audit checks the environment around the factory, including the storage of garbage and other items. This is because there are cases where the sanitary environment within the factory premises deteriorates due to the scattering of garbage by crows and pigeons.
How visitors to the premises are checked and security measures are also evaluated as part of the company’s risk management.
4. Key Benefits for Third-Party Factory Audit
Deficiencies that could not be detected in the factory and points that are difficult to notice can be recognized anew by having a third party’s eyes diagnose them.
The company can aim to reduce the defect rate by using raw materials in a waste-free manner, and improve work efficiency by reviewing the production process.
A factory audit will help you determine whether you can do business with us in the future. The purpose of the factory audit is not only to find out where the problems are, but also to determine how to improve the problems and whether the problems can be improved.
The factory’s response to any points that need to be improved is also an important aspect of the audit. Information on what needs to be improved should be shared within the factory, and the entire factory should thoroughly make rules and follow them. Since this will affect the credibility of the company, please keep a high awareness of crisis management.
Conclusion
Factory audits are necessary to predict the situation of suppliers and possible risks. Variations in work processes and maintenance records make it impossible to maintain consistent quality. It is also important that defective products are carefully handled in the way they are stored so that no foreign objects or other defective products are mixed in with shipments.
A factory audit conducted by a third party will reveal points that need to be improved. The purpose is not only to improve problem areas, but also to evaluate how the company is addressing the problems that have occurred. Please be aware of crisis management in order to increase the level of trust in your company and to ensure safe and smooth transactions.