What is important in blowing molding quality control? The equipment matters a lot for production, and the quality will be affected by many factors. Today, let’s learn about some common blow molding materials and how to improve the quality of blow molded products.
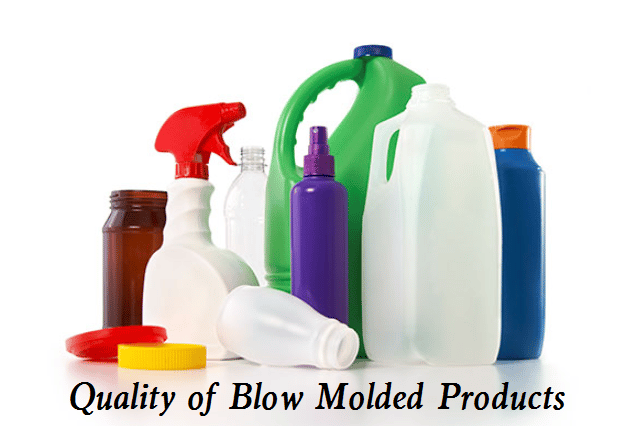
Tips for Improving Quality of Blow Molded Products
1) Blowing pressure
The blowing pressure can make the semi-molten tube blank blow and close to the mold cavity wall to form the desired shape, and also can cool the blow molded products. Generally, too large or too small blowing pressure of a large volume is not conducive to production, so the shape and pattern of pressure products can be clearer when selecting appropriate ones.
2) Speed
In order to shorten the blowing time to obtain blow molded products quickly, a large amount of air should be injected in a short time to ensure that the mold cavity can expand evenly and rapidly, and shorten the cooling time in the mold cavity.
3) Blow mold temperature
The mold temperature has a great influence on the appearance of blow molded products. Generally, the mold temperature should be cooled as evenly as possible. The mold temperature is related to the type of plastic, the thickness, and the size of the products. The mold temperature is too high, the cooling time is extended, the production cycle is increased, and the productivity is decreased. If the cooling is not enough at this time, the demoulding deformation of products will be caused, the shrinkage rate will increase, and the surface gloss will become poor. Generally, for plastics with high molecular chain rigidity, the mold temperature should be higher; For plastics with large molecular chain flexibility, the mold temperature should be lower.
Common Blow Molding Plastic Materials
Blow molding, also known as extrusion blow molding, is a rapidly developing plastic processing method. Typical blow molding products include small as bottles, barrels, cans, boxes, and all containers for packaging food, beverages, cosmetics, medicines, and daily necessities. From automobile manufacturing to the fuel tank, car shock absorbers, seat back, center bracket, armrest, and headrest covers. Most of the products we see in life are blow molded products. The selection of blow molding materials is related to the surface finish of plastic products. The common materials of blow molding products that can be used in actual production are PP, PE, and PVC, which have their own advantages and disadvantages.
- PP (Polypropylene) is a colorless, odorless, non-toxic, and translucent solid material with good chemical resistance, heat resistance, and electrical insulation, which has been widely developed and applied in many fields such as machinery, automobile, construction, textile, packaging, agriculture, forestry, fishery, and food industry.
- PE (Polyethylene) is a macromolecular organic compound formed by the addition and polymerization of ethylene. Commonly used food contact materials are non-toxic, tasteless, and odorless, which meet the hygienic standards for food packaging. PE is heat resistant, cooking resistant, cold resistant, freezing resistant, moisture-proof, gas resistant, and insulating. It is not easy to damage the products manufactured. It is beautiful, strong, impact resistant, and corrosion resistant. It can contain chemical raw materials, pesticides, lubricants, coatings, medicine, food liquid, and solid articles in hardware, electronics, electromechanical, and other industries.
- PVC is widely used in building materials, industrial products, daily necessities, floor leather, floor tiles, artificial leather, pipes, wires and cables, packaging films, foaming materials, sealing materials, fibers, etc.