Parts inspection work is an important part of the mechanical maintenance process, machinery, and its parts are through the inspection to determine their technical condition and the process measures to be taken, and then, through the quality inspection to determine the technical quality after repair.
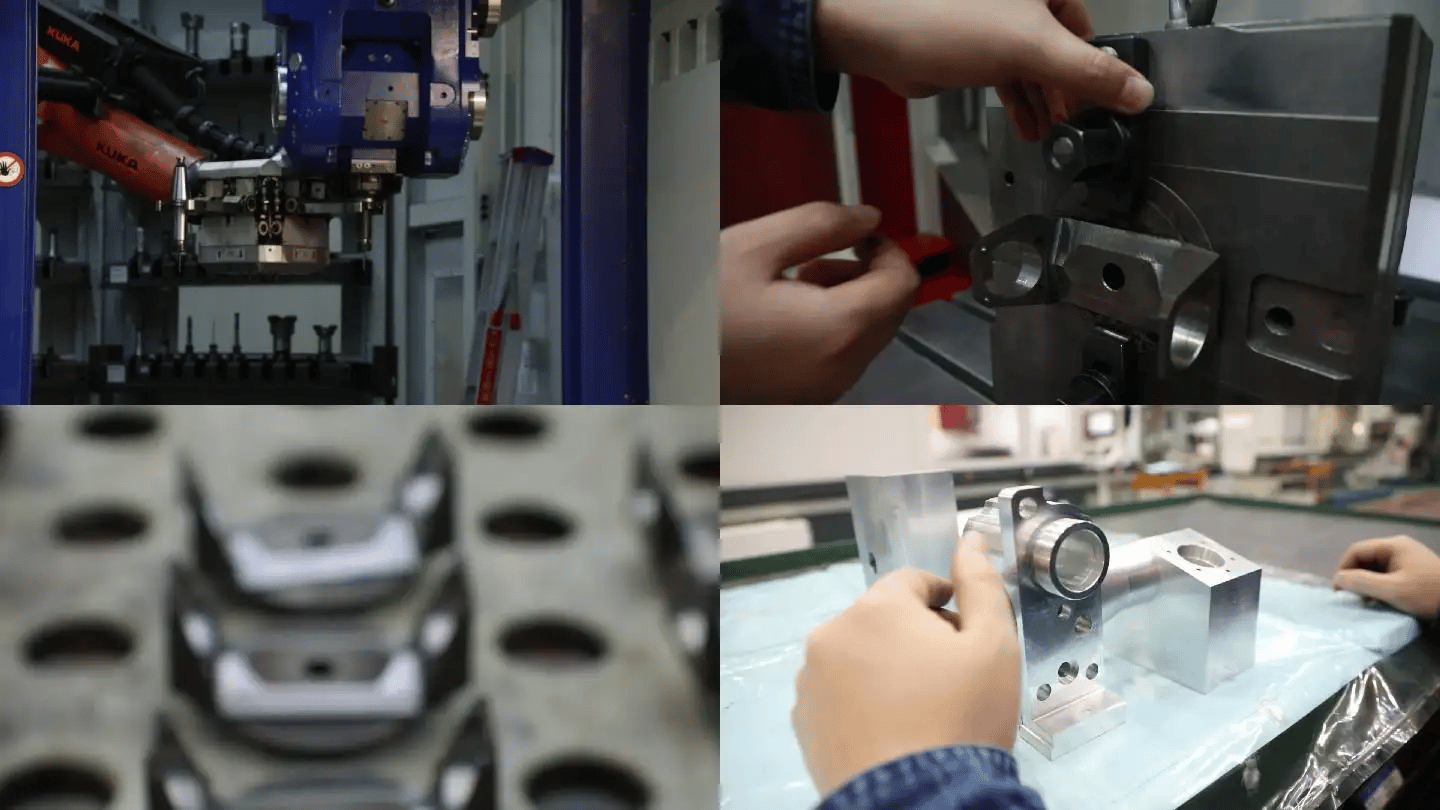
1. The main content of parts inspection
In the mechanical overhaul, parts are generally inspected one by one, and their main contents can be divided into the following aspects.
▶ 1) inspection of the geometric accuracy of the parts
Geometric accuracy includes dimensional accuracy and shape and position accuracy, but the overhaul work is sometimes not the pursuit of an individual part’s geometric size, but the requirement of relative fit accuracy, which is often an important part of the inspection work.
Shape and position accuracy are common in overhauling, such as roundness, cylindricity, concentricity, coaxiality, parallelism and perpendicularity.
▶ 2) Inspection of surface quality
The inspection of the surface quality of the parts in the inspection work is not only limited to the inspection of the surface finish, but also the inspection of the used parts surface for defects such as scratches, burns and hair pulling.
▶ 3) Inspection of mechanical properties
According to the characteristics of mechanical overhaul, in addition to the mechanical properties of the parts material in the hardness of a check, other indicators are generally not checked, but the parts manufacturing and overhaul process touched by certain properties, such as balance conditions, spring stiffness, etc., can not be ignored.
▶ 4) Inspection of hidden defects
Parts in the manufacturing process, there may be internal slag, cavities and other original defects, in the process of use may produce microscopic cracks. These defects can not be found directly from general observation and measurement, but they may have serious consequences for machinery, therefore, in the mechanical overhaul, it is necessary to purposefully carry out a comprehensive inspection of certain parts.
2. Methods of parts inspection
There are many methods of parts inspection, and new inspection techniques are evolving day by day. But from the actual work of mechanical maintenance, can be summarized as follows.
▶ 1) feeling inspection method
This is a method to identify the technical condition of the parts without checking the equipment, only by the intuitive feeling of the inspector. This method is simple, and in the mechanical overhaul, it is also easier to distinguish the defects of a large number of disassembly inspection parts. However, this method can not be used to check the high precision requirements of the parts, and requires inspectors have more experience.
▶ 2) Instruments, tools inspection method
A large number of inspection work is carried out with instruments and tools. As the principle of action and types of instruments and tools vary, it can be divided into general-purpose gauges, special gauges, mechanical instruments and meters, optical instruments, electronic instruments, etc.
▶ 3) Physical inspection method
This is a method of detecting the technical condition of parts by using changes caused by physical quantities such as electricity, magnetism, light, sound and heat through the workpiece. This method is also realized in combination with the instrument and tool inspection method. This method is usually used to check the internal hidden defects of the parts without damaging the parts themselves, existing commonly known as nondestructive testing. Nondestructive inspection techniques are increasingly developed in recent years, and now widely used in production are magnetic particle method, penetration method, ultrasonic and ray method.
3. Sensory inspection of parts
▶ 1)Visual inspection
Visual inspection is the main content of sensory inspection, such as fractures and macro cracks of parts, obvious bending and twisting deformations, burns and abrasions on the surface of parts, and severe wear and tear, which can usually be identified directly with the naked eye. In order to improve the accuracy of visual inspection, in some cases it can also be done with the help of a magnifying glass. In order to make up for the lack of visual inspection of the interior of certain walls, endoscopy with the help of optical fibers as light transmission is also available.
▶ 2) Auditory inspection
The method of determining the presence or absence of defects in mechanical parts by virtue of the hearing ability of the human ear is a long-established inspection method. This method has been used for decades in the daily inspection of railroad vehicles. Inspection of the inspected workpiece knocking, when the parts are not defective, the sound is crisp, and when there is internal shrinkage, the sound is low, if the internal cracks, the sound is hoarse, therefore, according to the different sound, you can determine whether the parts have defects.
▶ 3) Tactile inspection
Touching the surface of the part with your hand, you can feel its surface condition. Relative shaking of the mating parts can feel its mating condition. The machinery in operation, by touching its parts, can feel its heating condition, so as to judge its mechanism condition.
4. Measures to ensure the quality of parts inspection
▶ 1) Strictly grasp the technical standards
Most mechanical parts and mating parts have prescribed technical standards, which is the main basis of inspection work, in the absence of a reliable basis to believe that the need to modify the standards, to strictly comply with these standards, never allow the lowering of standards, and the unqualified parts into use.
▶ 2) Select inspection equipment in accordance with the requirements of the inspection object
Inspection equipment should be selected in accordance with the nature and scope of the inspection items, but also pay special attention to the requirements of precision.
For example, in the length measurement, when the required accuracy in the range of 1mm, with a steel ruler can be; when the required accuracy in the range of 0.1mm, it is generally used vernier calipers; when the required accuracy in the accuracy of 0.01mm, it is necessary to use a micrometer, percentage table; when the required accuracy in the accuracy of 0.001mm, it is necessary to use a comparator. If the accuracy of the inspection equipment is lower than the accuracy required by the object to be measured, it is simply impossible to meet the quality inspection requirements, and attention must be paid to prevent.
▶ 3)Improve the technical level of inspection operation
Inspection operation technology level directly affects the inspection accuracy, whether it is the self-inspection of the maintenance personnel or the inspection of full-time inspectors, the operator is required to master the inspection equipment used and clear inspection requirements of the object to be inspected. For this reason, attention should be paid to the improvement of inspection technology, special training should be provided for the use of special and important inspection equipment, and various inspectors should be relatively stable.
▶ 4) Reduce inspection errors
Any inspection results are inevitably error, its impact is multifaceted, for this reason should be prevented and eliminated from the following aspects.
● The inspection equipment has its own accuracy level, and it should be regularly calibrated and maintained with care to keep it at its proper accuracy.
● Correction of errors caused by temperature. Among the environmental factors affecting inspection accuracy, the influence of temperature is the greatest. For example, the influence of line expansion in length inspection and the change of nature caused by temperature change in electronic devices should be corrected as necessary in more precise measurement.
● The error caused by improper operation or inaccurate reading is mostly accidental, so the average value of multiple measurements can be taken, which can greatly reduce its degree of error.
▶ 5)Establish a sound inspection regulation system
Reasonable inspection system is the organizational guarantee to improve the inspection work, to establish a job responsibility system, clear responsibility, everyone keep the gate, and suggest a certain acceptance handover system and measurement and calibration system, etc.