In recent years, a labor shortage has become a problem at many manufacturing sites. Due to the declining birthrate and aging population, there is a shortage of human resources in all industries, so more and more companies are hiring foreign technical interns. However, in order to hire interns, they must go through a number of procedures, such as obtaining a status of residence and visa, applying to a management organization, and applying for certification of a technical internship plan.
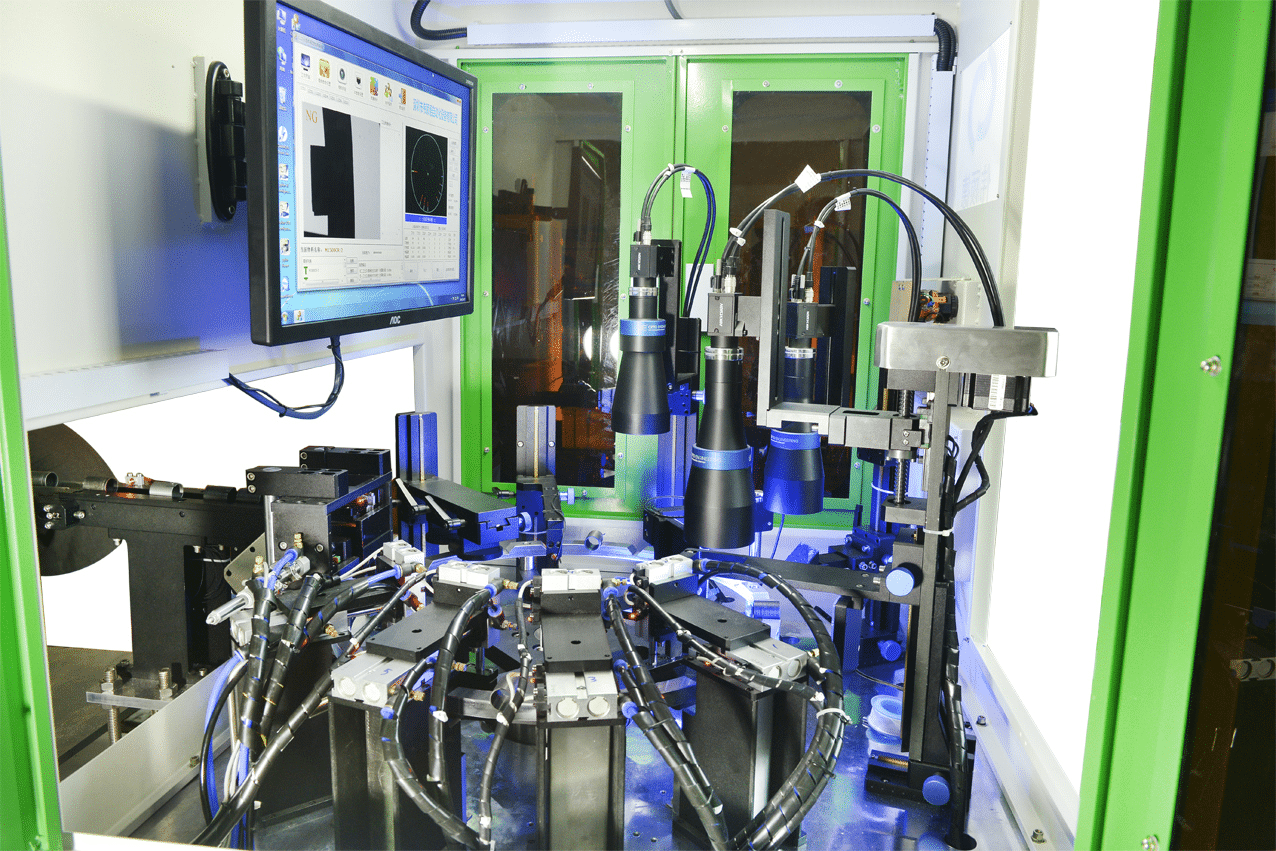
Fortunately, the shortage of manpower for visual inspection at manufacturing sites can be solved by visual inspection using images. However, when introducing a system, it is necessary to determine whether it is suitable for your company.
Therefore, in this article, we will introduce the mechanism of visual inspection using images, the range of detection, and recommended systems.
Visual Inspection Using Images
In the manufacturing industry, labor shortages have become chronic due to the effects of the declining birthrate and aging population, but in recent years, visual inspections using images have been shifting as an alternative inspection method to humans. Let’s take a closer look at what visual inspection using images is.
What Is Visual Inspection?
Visual inspection is to check for external defects in products and parts and make a quality judgment.
This is an essential process for guaranteeing and maintaining products manufactured in-house, and mainly checks the surface of products for defects and defects such as scratches, stains, chips, deformation, and burrs.
The pass/fail judgment is based on the standards set by the company, and if there are vague standards such as scratches or discoloration, the inspection is conducted based on a “sample product that shows the limit of good and defective products” called a “limit sample”. If visual inspection is omitted, defects such as defective products being distributed in the market and feedback to the front-end process will occur.
If a defective product flows into the market, not only will it incur the cost of collecting it, but it will also greatly erode trust in your company. In addition, since the occurrence of defects cannot be fed back to the previous process, it is not possible to improve and improve quality. In other words, visual inspection is an essential process in the manufacturing industry.
Appearance Inspection Using Visual
Visual inspection using images is becoming popular as an alternative to visual inspection performed by humans. In humans, the eye is a camera, and the brain is equivalent to software. Images are processed by both hardware such as cameras and lighting and the software that powers them. The combination is called an “image processing system” or “image sensor”.
The visual sensor outputs the position, angle, dimensions, shape, quantity, etc. of the product from the image data captured by the camera, and makes a judgment on the quality of the product by comparing it with the data registered in advance. In other words, image inspection is an automatic inspection instead of visual inspection with the naked eye.
Benefits of Visual Inspection
Here are the benefits of image testing:
Increase inspection efficiency and productivity
Compared to visual inspection, imaging requires less time to process. Therefore, improvement in inspection efficiency can be expected. In particular, AI-based visual inspection can further improve inspection efficiency because the inspection process can be automated.
Since human inspection is performed with the naked eye, it is difficult to recognize small scratches and dirt. In some cases, it may be necessary to use a microscope. Using a microscope improves the accuracy of the inspection and reduces the risk of missing a miss, but it is undeniable that the efficiency is reduced.
On the other hand, if you use a high-quality camera, you can detect even the smallest scratches instantly. By introducing image inspection, inspection efficiency can be improved.
In addition, since image inspection can be performed with fewer personnel than visual inspection, workers who have been in charge can be transferred to the production process. Increasing the number of personnel in the production process also leads to improved productivity.
Improvement and stabilization of inspection quality
Visual inspection using images can improve and stabilize inspection quality. The problem with visual inspections has been that there are differences depending on the proficiency level of the worker performing the inspection. However, in image inspection, good or bad is judged based on pre-set criteria.
By having standards in advance, inspection quality can be stabilized and uniform can be achieved. In addition, even minor defects that are difficult to judge and detect by visual inspection can be detected, improving inspection quality.
Preventing Human Error
Since visual inspection is performed by humans, it is difficult to inspect products with particularly large quantities without mistakes. In addition, if inspection workers continue to inspect on a daily basis, human error may occur due to physical fatigue and condition. Of course, human error can occur due to the low level of proficiency of the operator.
On the other hand, with machines, there is no human error due to poor condition like humans, so stable inspection quality can be achieved.
Reduce long-term costs
In machine-based image inspection, it is expensive to introduce inspection machines and AI. In addition, the initial cost of building a production environment such as a workflow is also required. In this way, although there is an initial cost at the time of introduction, the number of workers can be reduced after deployment, leading to long-term inspection costs.
In addition, it is expected that visual inspections will require sudden replenishment of personnel. In that case, it takes time and cost to train so that accurate inspections can be performed, but by introducing image testing, the difficulty of hiring and training human resources will be eliminated.
Disadvantages of Visual Inspection
As mentioned above, image inspection can reduce costs compared to visual inspection in the long run, but the introduction of equipment and systems such as cameras and lighting incurs initial costs such as installation and development costs.
In addition, specialized inspection equipment has the functions necessary for visual inspection, but it has the disadvantage of being expensive and not versatile. It will be necessary to carefully select according to your budget, environment, and inspection targets.
Range that can be detected by Visual Inspection
We have summarized the range of defects that can be detected by image inspection by industry and product:
- Metal industry: cracks, chips, burrs, dimensional misalignment, deformation, rust, nests, bubbles, bruises, etc.
- Food industry: tears, stains, burns, dents, scratches, foreign matter, printing errors, mixed with different products, etc.
- Resin industry: silver streaks, scratches, stains, streaks, discoloration, air bubbles, etc.
- Electronic device industry: Adhesion of dirt and foreign matter, short circuits, wire breaks, insufficient solder, etc.
- Daily necessities industry: Presence or absence of printing, faintness, mistakes, label tears, label misalignment
- Medical industry: Liquid level height, sealing seals, contents, label misalignment / tearing, printing errors, etc.
- Forming and sheet industry: pinholes, fish love, gels, bubbles, cracks, cracks, etc.
The above is just one example, but conventional visual inspection must detect many types of defects with the human eye, and there is a limit to its capabilities. However, with image inspection, as already explained, human error due to fatigue and condition of inspectors does not occur, and it is possible to find defects stably.