In today’s competitive marketplace, ensuring high-quality products and services is crucial for the success and reputation of any organization. Two key terms that often come up in quality management discussions are “quality inspection” and “quality assurance.” While they both contribute to maintaining quality standards, they differ in their approach and objectives. In this comprehensive article, we will explore the fundamental differences between quality inspection and quality assurance, shedding light on their roles, processes, and significance within the realm of quality management.
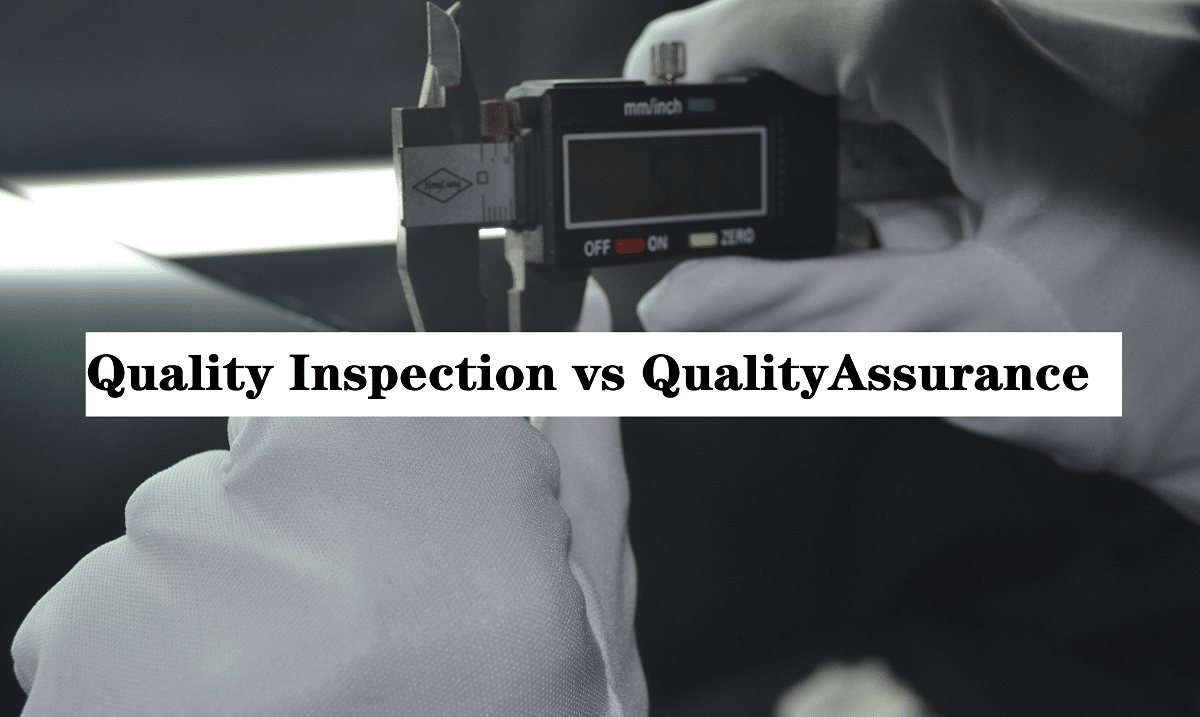
1. Defining Quality Inspection
Quality inspection refers to the process of examining and evaluating products, services, or processes to determine their compliance with established quality criteria. It is a reactive approach focused on identifying defects, deviations, or non-conformances in the final output or during specific stages of production. Quality inspection typically involves visual inspections, measurements, tests, and sampling to assess the quality level of the inspected item.
2. Understanding Quality Assurance
Quality assurance, on the other hand, encompasses proactive activities that are designed to prevent defects, errors, or deficiencies in products, services, or processes. It involves systematic planning, implementation, and monitoring of processes to ensure that quality requirements are met throughout the entire lifecycle. Quality assurance aims to establish robust systems, procedures, and controls to consistently deliver products or services that meet or exceed customer expectations.
3. Focus and Objectives
The primary focus of quality inspection is on identifying and addressing defects, errors, or non-conformances after they have occurred. It aims to identify issues that have already taken place and ensure that they are corrected or resolved before the products or services reach the customer. Quality inspection is essential for maintaining minimum quality standards, verifying compliance with specifications, and preventing the delivery of substandard goods or services.
In contrast, quality assurance concentrates on preventing defects and non-conformances from happening in the first place. It emphasizes the proactive implementation of standardized processes, quality control measures, and continuous improvement practices to ensure that products or services consistently meet or exceed customer expectations. Quality assurance aims to build a culture of quality throughout the organization and focus on preventing issues rather than merely identifying them.
4. Timing and Placement
Quality inspection typically occurs at specific stages of the production process or as a final check before the product is delivered to the customer. It is a point-in-time activity that occurs after the product or service is completed or during critical checkpoints to identify any deviations from the defined quality criteria. Inspections can be conducted on a sample basis or on the entire batch, depending on the nature of the product and the inspection requirements.
On the other hand, quality assurance is an ongoing and continuous process that starts from the initial stages of product development or service design. It encompasses various activities such as establishing quality objectives, defining quality standards, implementing quality control measures, conducting internal audits, and implementing corrective and preventive actions. Quality assurance is embedded within the organizational processes and operations to ensure consistent quality throughout the entire value chain.
5. Roles and Responsibilities
Quality inspection is primarily carried out by trained inspectors or quality control personnel who possess expertise in evaluating product or service quality. They are responsible for conducting inspections, measurements, tests, and evaluations to determine the conformity of the inspected item with the established quality criteria. Inspectors play a critical role in identifying defects or non-conformances and initiating appropriate actions for resolution.
In the case of quality assurance, the responsibility lies with various stakeholders throughout the organization. Quality assurance personnel, quality managers, and cross-functional teams collaborate to establish quality policies, define quality objectives, implement quality management systems, and monitor the performance of processes. They are responsible for creating and maintaining a culture of quality within the organization and ensuring that all activities are aligned with quality standards and customer requirements.
6. Relationship and Integration
While quality inspection and quality assurance are distinct concepts, they are interconnected and complementary in a quality management system. Quality inspection is an integral part of the quality assurance process, as it helps verify the effectiveness of quality control measures, identify areas for improvement, and ensure that the established quality standards are being met. The insights gained from inspections contribute to the continuous improvement efforts of quality assurance.
Quality assurance, in turn, provides the framework and infrastructure for effective quality inspection. It establishes the processes, guidelines, and controls that govern inspections and ensures that they are carried out consistently and in alignment with the organization’s quality objectives. Quality assurance integrates quality inspection as part of a broader quality management approach to achieve overall organizational excellence.
7. Continuous Improvement and Customer Focus
Both quality inspection and quality assurance contribute to the overarching goal of continuous improvement. Quality inspection helps identify areas for improvement, defects, and non-conformances, which can then be addressed through corrective actions or process improvements. It provides valuable data and feedback that can drive enhancements in product design, manufacturing processes, and service delivery.
Quality assurance, on the other hand, focuses on the proactive identification and prevention of potential issues. By establishing robust quality management systems, conducting regular audits, and implementing preventive actions, organizations can continuously enhance their processes, reduce variability, and deliver consistent quality to their customers. Quality assurance fosters a customer-centric approach by aligning organizational objectives with customer expectations and preferences.
Quality inspection and quality assurance are distinct yet interrelated concepts within the realm of quality management. While quality inspection focuses on identifying and addressing defects after they occur, quality assurance takes a proactive approach to prevent defects from happening in the first place. Quality inspection is a reactive, point-in-time activity, whereas quality assurance is an ongoing, continuous process that permeates the entire organization.
Both quality inspection and quality assurance are vital components of a comprehensive quality management system. By integrating these two approaches, organizations can ensure that their products, services, and processes consistently meet or exceed customer expectations, driving customer satisfaction and long-term success.