Check sheets are one of the types of 7 basic quality tools, which help you collect and organize data. Now we’ll go over check sheet uses and importance in quality control, as well as its types and difference between check sheets and checklists.
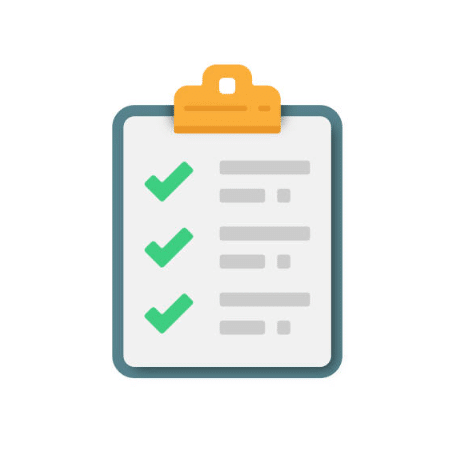
What Is A Check Sheet in Quality Control?
A check sheet in quality control is a simple tool used to collect and organize data in a structured and easy-to-use format. Check sheets are typically used to record the occurrence of specific events or the frequency of certain types of defects or issues. Check sheets can be used in quality control in a variety of ways, including:
- Recording defects or errors: Check sheets can be used to record the occurrence of defects or errors in a specific process or product. This can help identify patterns or trends in the data that may indicate the root causes of the defects or errors.
- Tracking progress: Check sheets can be used to track progress towards specific quality control goals. For example, a check sheet may be used to track the number of defects in a product over time, allowing quality control personnel to see if their efforts to reduce defects are effective.
- Identifying opportunities for improvement: Check sheets can be used to identify opportunities for improvement in a specific process or product. By recording data on the frequency of defects or errors, quality control personnel can see where improvements need to be made to maintain consistent quality standards.
Why is a check sheet important in quality control?
- It provides a simple and structured way to collect data: A check sheet provides a simple and structured way to collect data related to specific quality control concerns. This makes it easier to collect and organize data that can help identify patterns, trends, and opportunities for improvement.
- It improves communication: A check sheet can improve communication among quality control personnel by providing a common and easy-to-understand format for collecting and sharing data. This can help ensure that everyone is on the same page and working towards the same goals.
- It helps identify areas for improvement: By collecting data on specific quality control concerns, a check sheet can help identify areas where improvement is needed. This can include identifying the root causes of defects or errors and developing effective solutions to address them.
- It helps monitor performance: A check sheet can help monitor performance over time by tracking progress on specific quality control concerns. This can help ensure that quality standards are being maintained and that any issues are addressed in a timely and effective manner.
- It supports continuous improvement: By analyzing the data collected on a check sheet, quality control personnel can identify opportunities for continuous improvement. This can include introducing new processes or tools to improve quality, refining existing processes, or implementing corrective actions.
Difference Between a Check Sheet and a Checklist?
A check sheet is a structured form used to collect data by counting the frequency or occurrence of specific events or defects. Check sheets typically involve tallying marks on a sheet to indicate the occurrence of the event or defect. On the other hand, a checklist is a list of predetermined items or steps that need to be verified or completed. Checklists are used to ensure that all necessary tasks or requirements have been fulfilled. Unlike a check sheet, a checklist does not involve recording data or counting occurrences. In summary, the main difference between a checksheet and a checklist is its function. A check sheet is used to collect and record data, while a checklist is used to ensure that all necessary tasks or requirements are completed.
Main Types of Check Sheets
- Defect check sheet: A defect check sheet is used to record the type and number of defects found in a product or service. Each defect type is listed on the check sheet, and when a defect is found, a mark or tally is made in the appropriate column. Defect check sheets are useful in identifying common types of defects and the frequency of their occurrence.
- Attribute check sheet: An attribute check sheet is used to record whether a specific attribute or characteristic is present or absent. The check sheet typically lists the attribute or characteristic in question along with columns for recording whether it was present or not. Attribute check sheets are useful in collecting data on qualitative characteristics such as color, shape, or texture.
- Measurement check sheet: A measurement check sheet is used to record the measurement of a specific characteristic. The check sheet usually includes a scale for recording the measurement and space for recording the date, time, or other relevant information. Measurement check sheets are useful in collecting data on quantitative characteristics such as length, weight, or volume.