In modern manufacturing, precision and accuracy are essential for ensuring the quality and reliability of parts. Industries like aerospace, automotive, medical devices, and energy demand high standards, and Coordinate Measuring Machine (CMM) inspection has become a key component in meeting these requirements. Here we will explain what CMM inspection is, its benefits, application tools, software, reporting, and even a real-life case to help you understand its importance.
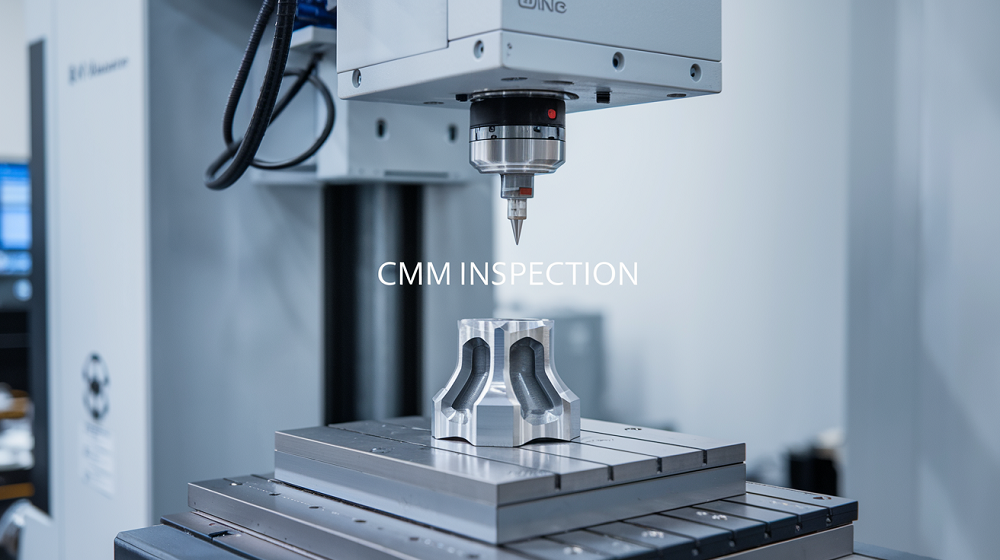
1. What Is CMM Inspection for CNC Machine?
A Coordinate Measuring Machine (CMM) is a high-precision device used to measure the geometry of parts. It collects data points from a part’s surface using a probing system, which can physically touch the part or use optical methods to gather measurements. These measurements are used to confirm if a part meets the required dimensions, tolerances, and alignments.
CMMs eliminate the inconsistencies and errors commonly associated with manual measurements. They handle everything from simple dimensions like length and width to more complex geometric dimensioning and tolerancing (GD&T) features such as flatness, perpendicularity, and circularity.
How Does CMM Inspection Work?
Here is how the CMM inspection programming:
- Probing System: The system moves along three axes (X, Y, Z) to collect data points.
- Coordinate Systems: Measurements are taken in Cartesian, cylindrical, or spherical coordinate systems, depending on the application.
- Data Analysis: CMM software processes the collected points to determine dimensions, angles, and GD&T parameters.
The accuracy of a CMM is what sets it apart. While manual tools may allow for errors, a CMM provides micrometer-level precision, ensuring the part meets design specifications.
Why Use CMM Inspection?
Here are the main reasons you should pick up CMM inspection for your product quality control:
Accuracy
CMMs deliver consistent and precise measurements that are far beyond the capabilities of traditional tools. For example, a CMM can measure tolerances as tight as two microns, making them invaluable in industries where even the smallest deviation can cause problems.
Efficiency
CMMs automate the inspection process, significantly reducing time spent on quality checks. A task that could take hours manually can be completed in minutes with a CMM, even for complex parts.
Reduced Human Error
Because the process is automated, it minimizes variability caused by operator skill or technique. This ensures consistent, repeatable results.
Versatility
Modern CMMs are adaptable to a variety of applications. From inspecting large aerospace components to tiny medical implants, they can handle a wide range of sizes, shapes, and materials.
When and Where to Use CMM Inspection?
CMM inspection is used in industries that demand precise measurements:
- Aerospace: For components like turbine blades and fuselage panels, where tight tolerances are necessary for performance and safety.
- Automotive: To validate parts such as engine components, frames, and gears.
- Medical Devices: To inspect surgical tools, implants, and prosthetics.
- Energy Sector: To measure parts used in turbines, pipelines, and energy systems.
CMM inspection is commonly performed during First Article Inspections (FAI), which verify new part designs before production. It is also used for in-process inspections to monitor production quality and for final inspections before a product ships to the customer.
2. CMM Inspection Methods
CMM inspection methods mainly include contact measurement and non-contact measurement.
1. Contact measurement
Contact measurement is a method of obtaining the size and shape of an object by measuring the position change of the probe by contacting the probe with the surface of the object being measured. The advantages of contact measurement are high measurement accuracy and strong adaptability, but the measurement speed is relatively slow.
2. Non-contact measurement
Non-contact measurement is a method of obtaining the size and shape of an object without contacting the surface of the object being measured through optical, electromagnetic and other principles. The advantages of non-contact measurement are fast measurement speed and no damage to the object being measured, but it is greatly affected by environmental factors.
3. CMM Inspection Standards
In order to ensure the accuracy and reliability of CMM product testing, various countries have formulated a series of CMM product testing standards. These standards mainly include:
1. International standards
The ISO 10360 series of standards issued by ISO (International Organization for Standardization) stipulates the functions, inspection methods and inspection procedures of CMM.
Why ISO Certification Matters in CMM Inspection
ISO certification plays an important role in ensuring inspection quality. A certified CMM inspection provider follows internationally recognized standards for accuracy and reliability. This gives manufacturers confidence that their parts are being evaluated to the highest benchmarks.
ISO-certified CMM inspections are especially important for industries like aerospace and medical devices, where non-compliance can have serious consequences. Choosing a certified provider ensures that the inspection process is thorough and accurate.
2. National Standards
The GB/T 16854 series of standards formulated by my country stipulates the terminology, classification, technical requirements, test methods, etc. of CMM.
3. Industry Standards
Different industries have formulated corresponding CMM product testing industry standards based on their own characteristics. For example, the aviation industry standard HB 747994 “General Technical Conditions for Coordinate Measuring Machines” and so on.
Following these standards will help improve the quality and efficiency of CMM product testing.
4. CMM Inspection Machines
CMM (Coordinate Measuring Machine) is a precision measuring device widely used in the field of quality inspection in the manufacturing industry. According to its structure, measurement principle and function, CMM equipment can be divided into the following types:
- Manual CMM: The operator manually drives the probe for measurement. It has a simple structure and low cost, but the measurement speed and accuracy are greatly affected by the operator’s skills.
- Electric CMM: It uses a motor drive to achieve automatic measurement. It has a fast measurement speed and high accuracy. It is suitable for mass production scenarios.
- Pneumatic CMM: It uses a pneumatic probe for measurement. It has high speed, high accuracy and good adaptability. It is suitable for the measurement of complex workpieces.
- Laser CMM: It uses a laser probe. It has the characteristics of non-contact, high accuracy and high speed. It is suitable for the measurement of surface shape and contour.
- Optical CMM: It uses an optical sensor for measurement. It has the advantages of non-contact, high resolution and high accuracy. It is suitable for the measurement of small size and precision workpieces.
Basis for Selecting CMM Machines
When selecting CMM equipment, the following factors should be considered:
- Measurement requirements: Determine the type and function of the required equipment based on the workpiece type, measurement items and accuracy requirements.
- Measurement range: Select an appropriate measurement range to ensure that the workpiece can be fully covered during the measurement process.
- Accuracy requirements: Select CMM equipment that meets the accuracy indicators based on the workpiece processing accuracy and quality requirements.
- Measurement speed: Consider the production cycle and measurement efficiency and select an appropriate measurement speed.
- Equipment cost: Consider the cost of equipment purchase, maintenance and calibration, and select CMM equipment with high cost performance.
- Ease of operation: Select CMM equipment that is easy to operate, maintain and troubleshoot.
- Environmental adaptability: Select CMM equipment with strong anti-interference ability and good stability based on the production site environment.
Calibration and Verification of CMM Machine
In order to ensure the measurement accuracy and reliability of CMM equipment, it must be calibrated and verified regularly.
(1) Calibration: CMM equipment calibration mainly includes the following steps:
① Check the appearance and structure of the equipment to ensure that the equipment is not damaged, deformed or loose.
② Check key components such as probes, guide rails and drive systems to ensure their normal operation.
③ Use standard instruments such as standard balls and gauge blocks to calibrate the equipment’s measurement system.
④ Calibrate the equipment according to the equipment manual and calibration specifications.
(2) Verification: Verify the measurement function of CMM equipment, mainly including the following aspects:
① Use standard workpieces of known dimensions for measurement to check the measurement accuracy of the equipment.
② Measure the same workpiece multiple times and analyze the stability and repeatability of the measurement data.
③ Check the measurement function of the equipment under various environmental conditions to ensure its environmental adaptability.
Through regular calibration and verification, the measurement accuracy and reliability of CMM equipment are guaranteed, providing effective guarantee for product quality inspection.
5. CMM Inspection Tools
CMMs rely on various tools and accessories for accurate measurements:
- Probes:
- Touch-trigger probes measure single points by making contact with the part.
- Scanning probes collect continuous data by moving across the part’s surface.
- Non-contact probes use lasers or cameras for optical measurements.
- Rotary Tables: Allow parts to rotate for better access and measurement of cylindrical surfaces.
- Calibration Balls: Ensure the accuracy of the CMM by calibrating probe tips.
- Universal Fixturing: A modular system for securely holding parts during inspection, making setup faster and more reliable.
6. CMM Inspection Software
The software used with CMMs is just as important as the machine itself. It manages data collection, analysis, and reporting.
- Acquisition Software:
This software controls the CMM during measurement. It ensures the machine follows the correct probing paths and records accurate data. - Analysis Software:
After the data is collected, analysis software evaluates dimensions, tolerances, and GD&T features. It also generates detailed inspection reports for quality assurance.
When choosing software, it’s important to ensure compatibility with the CMM hardware, ease of use, and robust reporting capabilities. Many manufacturers offer their own first-party software, but third-party options are also available for more advanced analysis and reporting.
7. CMM Inspection Reports
CMMs generate reports that summarize the results of an inspection. A typical report includes:
- Feature List: Displays all inspected features, such as holes, edges, and surfaces.
- Tolerances: Specifies the acceptable deviation range for each feature.
- Measured Values: Shows the actual dimensions recorded during the inspection.
- Pass/Fail Indicators: Indicates whether each feature met the required specifications.
- GD&T Analysis: Evaluates features like flatness, perpendicularity, and runout.
These reports provide valuable insights into part quality and help manufacturers identify areas for improvement.
Example of a CMM Report Chart
Below is an example report chart for a component inspection:
Feature | Nominal Value | Measured Value | Tolerance | Pass/Fail |
---|---|---|---|---|
Hole Diameter | 10.000 mm | 10.002 mm | ±0.005 mm | Pass |
Hole Position (X) | 50.000 mm | 50.003 mm | ±0.010 mm | Pass |
Surface Flatness | 0.020 mm | 0.025 mm | ≤0.030 mm | Pass |
Parallelism | 0.010 mm | 0.011 mm | ≤0.012 mm | Pass |
Perpendicularity | 0.005 mm | 0.008 mm | ≤0.010 mm | Pass |
This chart allows manufacturers to quickly identify features that pass or fail inspection, ensuring that issues are addressed before parts move to the next stage of production.
How to Read a CMM Inspection Report
While inspection reports may seem technical, they are straightforward with a little guidance:
- Check the Feature List: Look at the features being inspected and their corresponding tolerances.
- Review Measured Values: Compare the measured values to the nominal dimensions.
- Analyze Pass/Fail Results: Identify any features that didn’t meet specifications.
- Examine GD&T Results: Pay attention to geometric tolerances, as these often affect part functionality.
Uses these reports helps manufacturers ensure their parts meet design requirements and avoid downstream issues.
8. CMM Inspection Case: Solving a Production Bottleneck
A mid-sized automotive manufacturer faced a recurring issue where their engine components didn’t meet specifications, causing costly delays in production. They decided to implement CMM inspection to solve the problem.
- Problem Identification:
Components were failing quality checks during assembly, but the root cause wasn’t clear. Manual measurements were inconsistent, and the process was time-consuming. - CMM Implementation:
The company invested in a CNC CMM with a touch-trigger probe and scanning capabilities. They programmed the CMM to measure critical dimensions on every part immediately after machining. - Results:
Within weeks, the manufacturer identified that a machining tool was wearing out prematurely, causing dimensional errors. By replacing the tool more frequently, they eliminated the defect. The CMM also reduced inspection time from 30 minutes per part to just 5 minutes. - Impact:
Production delays were reduced by 50%, and rework costs dropped significantly, saving the company thousands of dollars annually. The CMM also provided detailed inspection reports, which helped the team improve their overall process.
This case highlights how CMM inspection can not only catch defects but also improve overall efficiency and profitability.