Coating is one of the surface treatment technologies in metal processing. By generating a thin film on the surface of the cutting tool, the performance of the original tool material, which is the base material, is enhanced. It is possible to create excellent tools that combine hardness (high sharpness) and toughness (resistance to chipping).
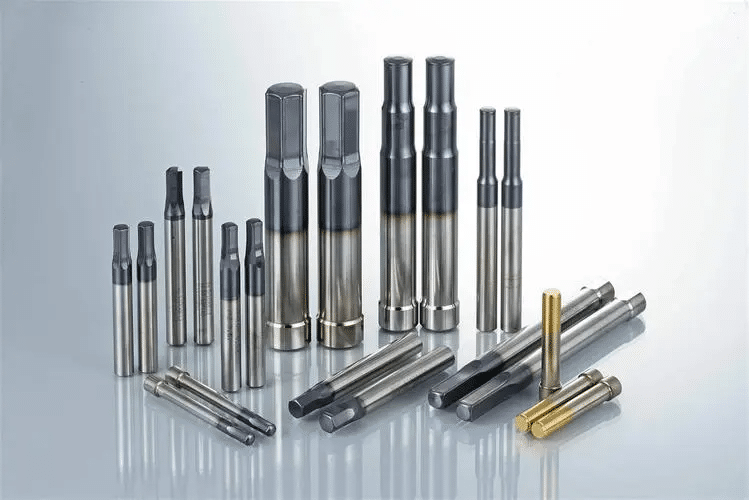
Coated tools are widely used as high-precision, high-efficiency cutting tools and stamping dies. This article explains the types of coating films and coated tools used in metalworking sites and their film deposition methods.
What Is Coating?
Coating is a surface treatment technology that creates tools that combine the conflicting properties of “hardness” and “toughness” by vaporizing another material on the surface of the tool that serves as the base material. The materials used for coating have high properties such as wear resistance and heat resistance, but they cannot make tools by themselves. It is only when it is together with the tool material that serves as the base metal that its performance can be demonstrated.
Advantages Of Coatings
- Improved hardness – Improved sharpness of blades, improved discharge of chips
- Improved wear resistance – Improved tool life, reduced tool cost and tool setup
- Improved heat resistance – Reduced machining time due to high-speed machining
- Decrease in affinity with the workpiece – Prevention of workpiece adhesion and built-up edge
Types Of Coating Films
There are various types of coating tools (coating films), and nitrides such as titanium and chromium are vapor-deposited on tool materials such as high speed steel, cemented carbide, cermet, and ceramics to form thin films. It is necessary to select the optimum coating tool according to the work to be processed and the details of processing.
Ti (Titanium) Coating
This is a coating film made of titanium nitride. It is the mainstream coating mainly used in cutting tools and molds.
TiN coating (titanium nitride)
It is a hard coating film with excellent wear resistance. As a typical coating film, it is widely used in steel processing applications. Due to its high corrosion resistance and beautiful appearance, it is also used as a coating for ornaments.
TiAlN coating (aluminum titanium nitride)
This coating film is made by adding Al (aluminum) to titanium nitride. Since it has better heat resistance than TiN coating, it is ideal for high-speed cutting with high cutting temperatures and dry machining without using coolant.
TiCN coating (titanium nitride carbide)
This is a coating film in which C (carbon) is added to titanium nitride. Compared to TiN coating, it has better welding resistance, so it is suitable for low-speed cutting of steel materials. In addition, because of its high sliding properties and good glide, it is also ideal for molds such as punches.
TiC coating (titanium carbide)
This coating film is formed by reacting titanium nitride with C (carbon). Compared to TiN coating, it has particularly high hardness and slidability, making it ideal for molds and machine parts and jigs with a lot of sliding.
TiSiN coating (silicon nitride)
This coating film is made by adding Si (silicon) to titanium nitride. Among titanium-based coatings, it has the highest hardness and heat resistance, so it is used for high-speed cutting, dry machining, and special processing in harsh environments.
Cr (Chromium) Coating
This is a coating film made of chromium nitride. It is mainly used as a coating for molds and machine parts.
CrN coating (chromium nitride)
It is a hard coating film with excellent sliding properties. As a typical coating film, it is widely used in molds and machine parts. In particular, the adhesion property (bonding between materials) to copper is low, and it is highly effective in copper cutting.
AlCrN coating (chromium nitride)
This is a coating film in which Al (aluminum) is added to chromium nitride. It is a coating film with enhanced characteristics such as wear resistance and heat resistance, and is used in cutting tools and jigs.
DLC (Amorphous Hard Carbon Film) Coating
DLC stands for “Diamond-Like Carbon” and is a coating film with properties similar to diamond. It has excellent hardness, wear resistance, and sliding properties, and is used not only in cutting tools but also in a variety of products, including precision molds that require mold release and engine parts that require seizing resistance.
In addition, the adhesion to the workpiece (bonding between materials) is low, and it is especially effective in cutting non-ferrous metals such as aluminum and copper. This coating technology is indispensable for copper processing for electronic components and aluminum processing for automobile engines. Depending on the ratio of graphite to diamond and the hydrogen content, the properties of the coating film can be changed.
Coating deposition method, difference between PVD and CVD
Coating deposition methods can be broadly classified into two types: the chemical CVD method and the physical PVD method. These film formation methods cover the surface with a gaseous substance, so they are also called “vapor phase plating”. Since the coating varies depending on the film formation method, the film thickness and adhesion to the base metal are used, so they are used according to the workpiece and processing method.
Types Of Film Deposition Methods
CVD method (chemical vapor deposition method)
The CVD method (Chemical Vapor Deposition) is a film formation method that uses chemical vapor deposition. A chemical reaction (thermal CVD method) occurs at a high temperature of nearly 1000°C to form a thin film on the surface of the base metal.
It has excellent coating adhesion, but because the film is formed at high temperatures, the base material is limited and the dimensional accuracy and strength are slightly reduced. It is used for cutting tools that require adhesion such as rough machining, and coatings for molds and jigs. (Generally, it is classified into thermal CVD using gas, plasma CVD using plasma, and optical CVD using laser)
PVD method (physical vapor deposition method)
PVD (Physical Vapor Deposition) is a film formation method using physical vapor deposition. The coating material is ionized with plasma to produce a thin film on the surface of the base metal.
Since the film is formed at a low temperature (400~600°C), there is no dimensional change or strength reduction of the base material, and it is widely used in coating cutting tools such as drills, milling cutters, and end mills that require high strength. (Generally classified as vacuum deposition, sputtering, and ion plating)
Summary
In this article, we explained the types of coating tools and CVDs and PVDs. When adding a coating to a conventional tool, depending on the thickness of the thin film, it may affect the processing content, such as “tool dimensions change” and “chip discharge property changes” . It is important to use different tools according to their types. As coating tools become mainstream, we hope that this will be a hint for choosing a coating.