Calculating and managing Cost of Poor Quality (CoPQ) is important to maintain stable sales and improve customer satisfaction. This article will talk about what is CoPQ, as well as accurate inspection methods and benefits in quality control to reduce the cost of poor quality.
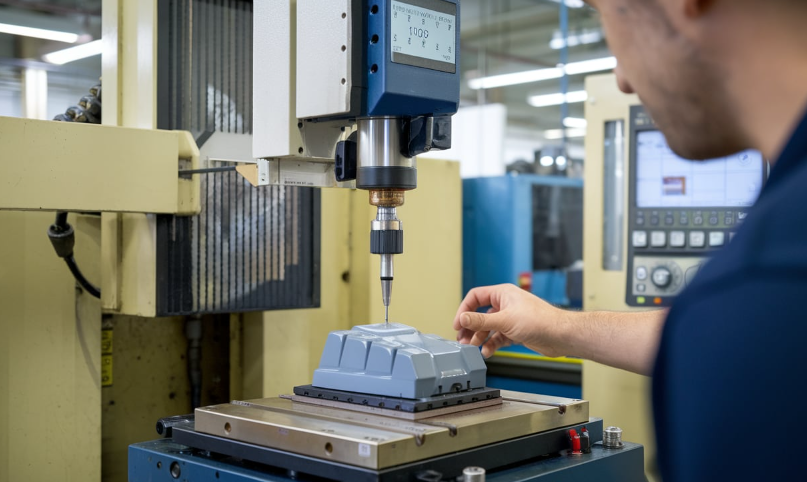
What Is Cost of Poor Quality (COPQ)?
The Cost of Poor Quality (CoPQ) represents the total expenses incurred by an organization due to the production of goods or services that fail to meet established quality standards. This includes financial losses from errors, defects, and inadequate work, and is classified into four primary categories: prevention costs (expenses for quality planning and training), appraisal costs (costs related to monitoring and measuring quality), internal failure costs (losses from defects identified before delivery, necessitating rework or disposal), and external failure costs (expenses from defects found after delivery, leading to warranty claims and returns). Why it is important to measure CoPQ? Understanding and managing these costs can help companies identify areas for improvement, enhance profitability, and ultimately boost customer satisfaction and market position.
What Are the Hidden Costs of Poor Quality Control?
There are lots of hidden risks and costs associated with inadequate or poor quality control, these risks can severely impact a company’s stability and reputation. While visible costs like scrap and rework are often acknowledged, the more elusive hidden costs can be even more detrimental.
- Nonconformances: Products that fail to meet specifications can incur additional costs due to rework and lost time.
- Customer Complaints: Addressing complaints can be resource-intensive and may erode customer trust and loyalty, this may bring long-term financial repercussions.
- Lost Sales: Poor quality can directly result in missed business opportunities as customers turn to competitors offering superior products or services. Customers who encounter poor quality are less likely to return, leading to a decrease in repeat business.
- Late Delivery: Quality issues can cause production delays, resulting in long cycle times and missed deadlines that strain customer relationships and affect future contracts.
- Supplier Incapability: Relying on suppliers who fail to meet quality standards can complicate the supply chain and increase costs.
- Excessive Raw Material Orders: Inadequate quality control may necessitate over-ordering materials to counteract defects, the inventory costs will increase.
- Degraded Brand Image: Consistent quality failures can damage a brand’s reputation, it is more difficult to attract and retain customers.
When it comes to the cases of costs of poor quality (control), there are two examples. In 2019, a major automobile manufacturer recalled over 300,000 vehicles due to defects in engine components, with the recall cost estimated at $600 million. If advanced inspection technologies, such as Non-Destructive Testing (NDT) or Coordinate Measuring Machines (CMM), had been employed, defects could have been identified and resolved at a lower cost. Another one, a medical device manufacturer faced lawsuits due to undetected microscopic cracks in a batch of surgical instruments during quality control. These cracks caused the instruments to fail during surgeries, leading to severe complications for patients. The financial repercussions included millions of dollars in legal settlements, regulatory fines, and loss of market share.
Uses and Benefits of Accurate Inspection – How Important Is Precise Quality Inspection?
Accurate inspection is essential to make sure products meet specified industry standards and customer expectations.
- Avoids Defects: Find part or product defects before they reach customers, including those that are usually difficult to detect, to reduce the likelihood of returns and complaints.
- Reduces Costs: By catching defects early in the production process, companies can avoid the higher costs associated with rework, scrap, and recalls, this can lead to significant savings over time.
- Improves Efficiency: Regular inspections can help identify bottlenecks and inefficiencies in manufacturing. Addressing these issues will ensure companies streamline operations and improve overall productivity.
- Protects Brand Reputation: Consistently delivering high-quality products helps build a strong brand reputation. Satisfied customers are more likely to return and recommend the brand to others, which can lead to increased sales.
- Compliance with Regulations: Many industries are subject to strict regulations regarding product quality. Accurate inspections ensure compliance with these regulations so as to avoid fines and legal issues.
- Enhances Employee Morale: When employees know that their work is subject to quality inspections, it can foster a sense of pride and responsibility. This can lead to improved performance and a more positive work environment.
- Identifies Potential Problems Early: Inspections can reveal potential issues before they escalate into serious problems. This early detection allows companies to take corrective actions promptly.
- Collects Valuable Data: Quality inspections provide data that can be analyzed to improve manufacturing processes, and further used for product improvement and innovation.
- Meets Customer Expectations: Good-quality products after precise inspection will meet or exceed customer expectations.
- Improves Competitiveness: In a competitive marketplace, companies that prioritize quality through accurate inspections can differentiate themselves from competitors, attracting more customers and increasing market share.
- Significant ROI: The return on investment (ROI) of quality inspection is huge, as it directly correlates with enhanced product quality, reduced costs, and improved customer satisfaction. By investing in accurate quality inspection processes, companies can minimize defects and errors, leading to lower rework and scrap costs. Studies indicate that for every dollar spent on quality management, businesses can expect an additional $6 in revenue, a reduction of $16 in costs, and a $3 increase in profits.
What Are Accurate Inspection Methods to Reduce Cost of Poor Quality?
CMM (Coordinate Measuring Machine) and NDT (Non-Destructive Testing) are commonly used inspection methods in quality control and management.
1. CMM Inspection Methods:
- Contact Measurement: utilizes a probe to physically touch the object’s surface and gather data points along the X, Y, and Z axes, ensuring precise dimensional measurements.
- Scanning Probes: measure points on an object’s surface continuously, generating a comprehensive point cloud used for detailed CAD model comparisons.
- Optical Measurement: employs laser or vision systems to measure object dimensions without physical contact, which is particularly suitable for fragile components.
- Laser Scanning: captures an object’s geometry by projecting laser beams and calculating the time it takes for the light to return, ultimately forming an intricate 3D model.
- Gage Repeatability and Reproducibility (Gage R&R): used to assess the measurement system’s precision, ensuring that observed variations in measurements result from the production process, not the measurement method.
2. NDT Inspection Methods:
- Ultrasonic Testing (UT): utilizes high-frequency sound waves to detect internal defects in materials, and it is frequently applied for weld inspections and thickness measurements.
- Radiographic Testing (RT): employs X-rays or gamma rays to examine an object’s internal structure, to assist in the identification of defects such as cracks and voids.
- Magnetic Particle Testing (MT): entails applying a magnetic field to ferromagnetic materials and employing iron particles to detect surface and near-surface defects.
- Dye Penetrant Testing (PT): applies a liquid dye to the surface of a part, and makes trapped dye in surface defects emerge after excess dye removal. A developer is then applied, revealing these defects.
- Eddy Current Testing (ECT): uses electromagnetic induction to detect surface and near-surface defects in conductive materials, as well as to measure conductivity and thickness effectively.